In today’s blog post we dive into the precision-driven world of laser cutting, a technology reshaping industries with its unparalleled accuracy and versatility. Below, we explore its essence, diverse applications, and how it measures up against traditional cutting methods.
Table of Contents
- What is Laser Cutting
- Applications of Laser Cutting
- Comparison with Plasma Arc Cutting
- Comparison with Mechanical Cutting Techniques
- Technological Advancements in Laser Cutting
- Environmental and Safety Considerations
- Cost Analysis and Efficiency
- Material Limitations and Challenges
- Future Trends and Potential
- Conclusion
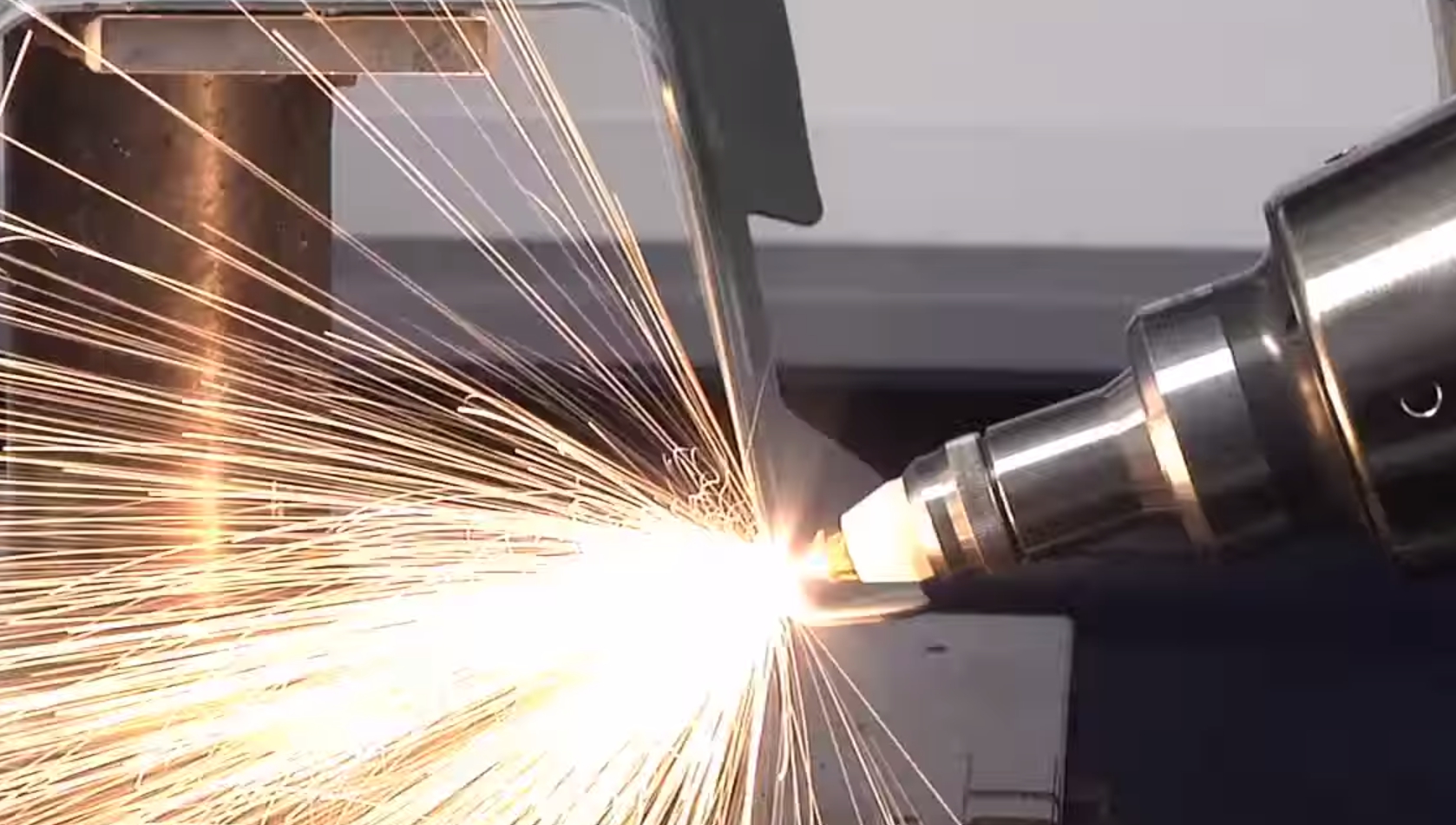
A Working Laser Cutting Head: the emergence of laser cutting techniques has significantly improved our ability to create and modify materials (Image Courtesy of TradeMachines)
1. What is Laser Cutting
Cutting is an intuitive application of laser devices. When converging a beam of photons onto a small spot, the resulting high energy density can easily vaporize materials. Thus, by moving the beam along a designed path, the workpiece can be separated into individual parts. Laser cutting techniques have now evolved into multiple forms, including vaporization cutting, fusion cutting, reactive fusion cutting, thermal stress cracking, scribing, and cold cutting. Each one of them involves different operating modes (pulsed or CW), energy level, and utilization or not of an assist gas. The choice of the optimal plan depends on material physical properties, light sources and other factors. Today, laser cutting has become the most common laser manufacturing technology, well-established in numerous industrial fields. The market share of laser cutting was 23% of the worldwide industrial laser applications in 2007, confirming it as one of the most firmly established laser techniques.
2. Applications of Laser Cutting
Laser cutting is never built as an isolated technique, rather, it has to be incorporated with other production approaches so as to maximize manufacturing versatility and efficiency. Perhaps the most prominent example lies in the modern production lines of automobiles.
Laser cutting combined with hydroforming has become an overwhelming technological trend in manufacturing of automobile components. Hydroforming is a process in which tubes and other hollow members are produced by forcing a fluid into a preform. The first application obtaining noticeable interest was the rear axle suspension used in the 1994 BMW 5 series. Today, automotive industry adopts hydroforming to produce vehicle frames, engine cradles, roof pillars and suspensions particularly in trucks and SUVs.
Hydroforming assisted by laser cutting is able to produce automobile parts with increased plate size, thickness and accuracy. Compared with traditional cutting methods such as plasma cutting, this technique boasts not only improved efficiency and productivity, but also clean and accurate cut edges in both square and bevel configurations. In addition, distortions in components made by laser cutting are significantly low. Hence, parts fabricated this way usually demand minimal secondary processing. This is the major reason that all circular holes down to 3mm in diameter are now laser cut, rather than drilled or punched. The most significant rewards of high accuracy in laser cutting are gained downstream. Designs are carried out with minimal deviation, components fit together more closely, while seamless joints benefit the final automobiles with superior structural robustness.
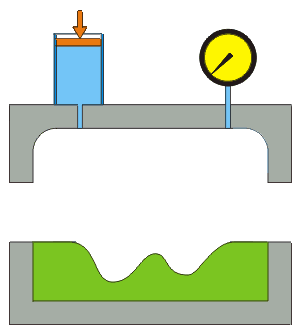
An animated process of hydroforming (Courtesy of Wikipedia)
The first car constructed with prefabricated laser-cut metal parts was Ford Capri II. Today there is a great interest in the use of robot-mounted fiber optic beam delivery from a Nd:YAG laser for cutting features in hydroformed parts.
3. Comparison with Plasma Arc Cutting
Laser cutting challenges many conventional techniques including plasma arc and waterjet cutting, which utilize thermal and mechanical processes.
By accelerating a jet of hot plasma, plasma arc achieves cutting mainly on electrically conductive materials, and is particularly effective for metals of high thermal conductivity. Today, most plasma equipment with air or oxygen is employed for two-dimensional cutting of sheet materials. Plasma arc cutting is able to process materials at moderate speed. The edge quality can be improved by operations under water, and the productivity can be increased if using multiple torches held by gantries.
Nonetheless, compared with plasma arc technique, laser cutting exhibits superiority in several areas. First, it boasts a higher cutting speed on thick materials, especially when a square edge of high quality with a narrow kerf width is required. Additionally, unlike plasma arc cutting which works mostly on metals, laser cutting also works on non-metal materials. Most importantly, laser cutting technique offers a higher accuracy and a smaller heat affected zone (HAZ). The non-contact mode of operation along with relatively low running costs makes laser cutting a preferred choice for many applications. In contrast, plasma arc cutting requires frequent replacements of the nozzle.
4. Comparison with Mechanical Cutting Techniques
Mechanical cutting – a traditional technique – also suffers from a series of problems. Cutting using dies often results in inconsistent size due to the existence of material elasticity. Knives cannot cope well with sharp profiles requiring rapid changes in direction. Compared to these methods, water jet cutting is now a popular mechanical approach adopted by many factories in the world.
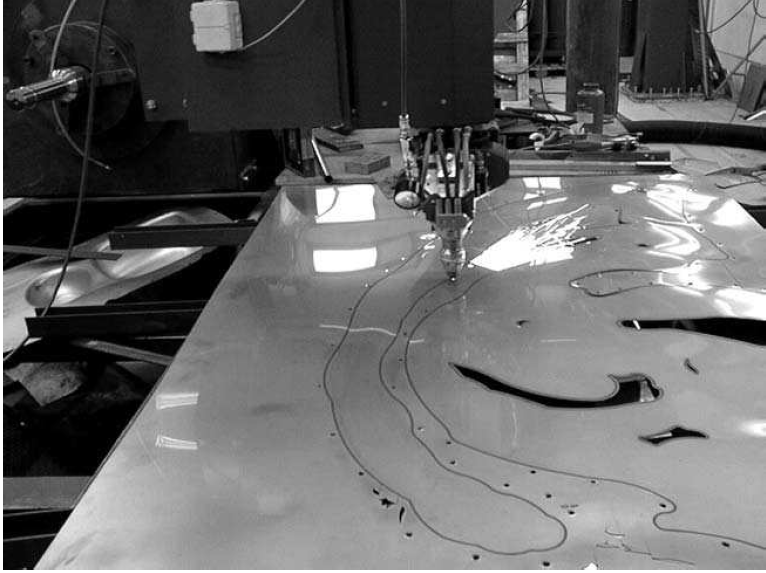
A laser machine is cutting a flat aluminum alloy sheet (Courtesy of Petri Metsola)
Waterjet cutting machines typically use pressurized water of up to 400MPa to cut materials. A high pressure pump forces the water through a small diameter sapphire or diamond nozzle (0.1-0.8mm) at speeds of about 800m/s. Abrasive particles when mixed with water can enable cutting of metals, composites and other hard materials. Silica, silicon nitride, garnet or alumina with diameters of 0.1-0.5mm are usual choices as abrasive particles. Water jet cutting is actually an erosion process and generates no HAZ. These properties are essential in some applications, especially in the aerospace industry. Waterjet cutting works great on inhomogeneous materials such as marble and concrete that could fracture on heating, and composites that delaminate when heated.
Compared to laser cutting, waterjet cutting shows better performance on reflective materials such as copper and aluminum, as well as heat-sensitive materials such as high alloy steels and titanium alloys. However, it suffers from a slow cutting speed, and hence a relatively low throughput. Most importantly, when cutting materials up to 100 mm thick, waterjet cutting exhibits problems with the edge profile. Due to the high energy of the jet, the top of the cut edge is smooth, but becomes rougher and striated lower in the workpiece as abrasive particles scatter. In contrast, laser cutting features high accuracy of cut edges. It is more suitable for three-dimensional out-of-position cutting, and normally provides the best combination of quality and productivity.
5. Technological Advancements in Laser Cutting
Innovations: Recent years have seen significant leaps in laser cutting technology. Laser power has surged, with high-powered fiber lasers now exceeding 12 kW, enabling faster cutting speeds and the ability to process thicker materials. Precision has also improved, with cutting tolerances now often within +/- 0.05 mm, facilitating intricate designs and high-quality finishes.
Software Developments: The integration of advanced software has transformed laser cutting into a more automated and efficient process. CAD/CAM systems have become more sophisticated, allowing for precise control over the laser cutting path and optimization of material usage. Automation software now supports real-time adjustments during cutting, reducing errors and enhancing productivity.
6. Environmental and Safety Considerations
Eco-Friendliness: Laser cutting stands out for its minimal environmental impact compared to traditional methods. It’s highly energy-efficient, often requiring less power due to its precision and speed. Waste production is significantly reduced as laser cutting produces cleaner edges and can utilize materials more effectively, minimizing offcuts.
Safety Measures: Safety in laser cutting operations is paramount. Operators must use personal protective equipment (PPE) such as safety glasses to protect against laser radiation. Modern laser cutters often come with enclosed cutting areas and interlock systems to prevent accidental exposure to the laser beam. Compliance with safety standards and regular training ensures a safe working environment.
7. Cost Analysis and Efficiency
Initial Investment vs. Operational Costs: The initial investment for a laser cutting system can range significantly, from approximately $40,000 for a basic setup to over $1 million for advanced industrial models. This cost is a function of the laser’s power, size, and additional features. Maintenance costs are relatively low compared to mechanical cutting systems due to fewer moving parts and no tool wear. However, operational costs must consider power consumption and the potential need for gas in some laser types, like CO2 lasers.
Efficiency: Laser cutting is renowned for its efficiency and speed. For instance, a modern fiber laser cutter can process thin sheets of metal at speeds up to 1,500 inches per minute, significantly faster than traditional mechanical cutting methods. This efficiency translates into shorter production times and lower labor costs, making laser cutting cost-effective for high-volume production runs.
Cost Benefits in the Long Term: Although the upfront cost of laser cutting equipment is higher, the long-term savings are substantial. The precision of laser cutting reduces material waste, and its speed minimizes operational hours, leading to a lower cost per part, especially in large-scale operations. For businesses focusing on custom or intricate designs, the ability to quickly and accurately produce parts without the need for expensive tooling further adds to the cost benefits.
In summary, while the initial investment in laser cutting technology may be higher, the efficiency, speed, and lower long-term operational costs can make it a more cost-effective solution compared to traditional cutting methods.
8. Material Limitations and Challenges
Material Restrictions: Laser cutting, while versatile, does have its limitations with certain materials. For instance, metals like copper and aluminum are highly reflective, posing challenges for some laser types. Thickness is another limitation; for example, https://www.findlight.net/blog/hwg-and-pir-fibers-co2-laser-beam-delivery-resolved/CO2 lasers can typically cut steel up to 25 mm thick, but efficiency drops significantly as material thickness increases. Materials like tempered glass, which can shatter under laser cutting, and certain plastics that emit hazardous fumes when cut, also present challenges.
Solutions to Challenges: Overcoming the challenges in laser cutting involves both technological advancements and operational techniques. For reflective materials, fiber lasers with a shorter wavelength are more effective. To manage heat affected zones (HAZ), pulse laser settings can minimize thermal input, preserving the integrity of the material. Reducing kerf width and improving precision is possible to achieve with nozzle adjustments and optimizing gas flow, which helps to eject molten material more effectively and maintain a narrow, focused beam.
9. Future Trends and Potential
The future of laser cutting holds promise for expanding into new industries and applications. In the medical field, for instance, laser cutting is ready to play a crucial role in fabricating intricate devices like stents and implants with unmatched precision. In the energy sector, the manufacture of solar panels and fuel cells may increasingly rely on laser cutting for its ability to work with delicate materials. The burgeoning field of flexible electronics, including wearable devices, also presents a vast frontier for laser cutting, enabling the precise shaping of conductive materials and polymers.
Advancements in laser cutting technology will soon push the boundaries of what’s currently possible. Ultrafast lasers, operating in femtoseconds (10^-15 seconds), are on the horizon, promising even finer precision and reduced thermal impact, mitigating the heat-affected zone issue. The integration of AI and machine learning could lead to smarter laser cutting systems that optimize cutting paths in real-time, enhance material utilization, and predict maintenance needs. Additionally, developments in laser sources may extend cutting capabilities to previously challenging materials, such as thicker metals and new composites, expanding the versatility of laser cutting across various industries.
10. Conclusion
Laser cutting technology stands at the forefront of manufacturing innovation, distinguished by its precision, efficiency, and versatility. Its ability to produce clean, precise cuts across a diverse range of materials has cemented its role in industries from aerospace to fashion. The technology’s adaptability to intricate designs and its compatibility with digital manufacturing processes underscore its growing importance. As we look to the future, the potential for laser cutting is boundless. It is abundant with emerging applications and technological advancements poised to overcome current limitations and open new avenues for exploration. The ongoing evolution of laser cutting promises not only to enhance its current applications but also to unlock innovative uses in sectors yet to fully embrace its capabilities.
If you liked this article, you might also be interested in our Guide to Laser Scan Heads.