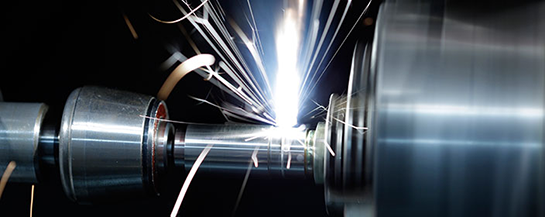
Working Laser Welding Machine. Laser welding techniques are a series of novel joining processes. (Courtesy of Coherent, Inc.)
What is Laser Welding?
While laser cutting is used for separating parts of an object, laser welding is a process that joins together separated materials. When a laser beam hits the material surface, the absorbed energy could cause heating, melting, and evaporation. To achieve the joining of different workpieces, the laser beam has to create a pool of molten material (weld pool) at the overlapping surface of the workpieces.
The most important laser welding approach is the deep penetration welding, which accomplishes material joining by creating a keyhole in the weld pool. In this scenario, the focused beam produces an incident power density that is sufficient to initiate vaporization. Multiple internal reflections of the beam form a narrow, deeply penetrating vapor cavity – a keyhole. Surrounded by molten material, the keyhole can form a narrow weld bead by traversing the beam relative to the workpiece.
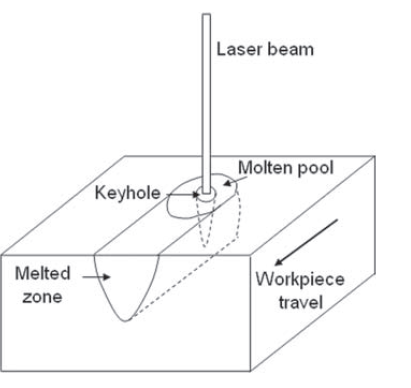
The schematic principle of laser keyhole welding. Courtesy of John. C. Ion
Today, laser welding techniques have evolved into multiple branches. As important industrial manufacturing processes, they perform welding on various metallic and nonmetallic materials.
Applications of Laser Welding
Laser welding techniques are gradually replacing the traditional methods for manufacturing large and complex heavy machines such as aircrafts. Previously, aircraft manufacturers such as Boeing had to adopt mechanical fastening approaches such as riveting. This was because the common aluminum aerospace alloys 2024 and 7075 are difficult to weld by fusion. However, riveting process itself involves many stages such as drilling, burring, sealing and placing the rivets. Not only it is an expensive method, but also it incurs weight penalties arising from the weight of the rivets themselves and the need for overlapping or strengthened joints. Most importantly, rivet holes can also become sources of cracking and corrosion. Hence, aircrafts made by mechanical fastening methods are subject to a much shortened lifetime.
The introduction of laser welding provides a perfect solution for these issues. First, it is a significantly simplified single-step process with high productivity. Additionally, it can not only provide potential weight saving of up to 10%, but also cost 20% less compared with adhesive bonding and riveting. Because of these intriguing advantages, companies such as
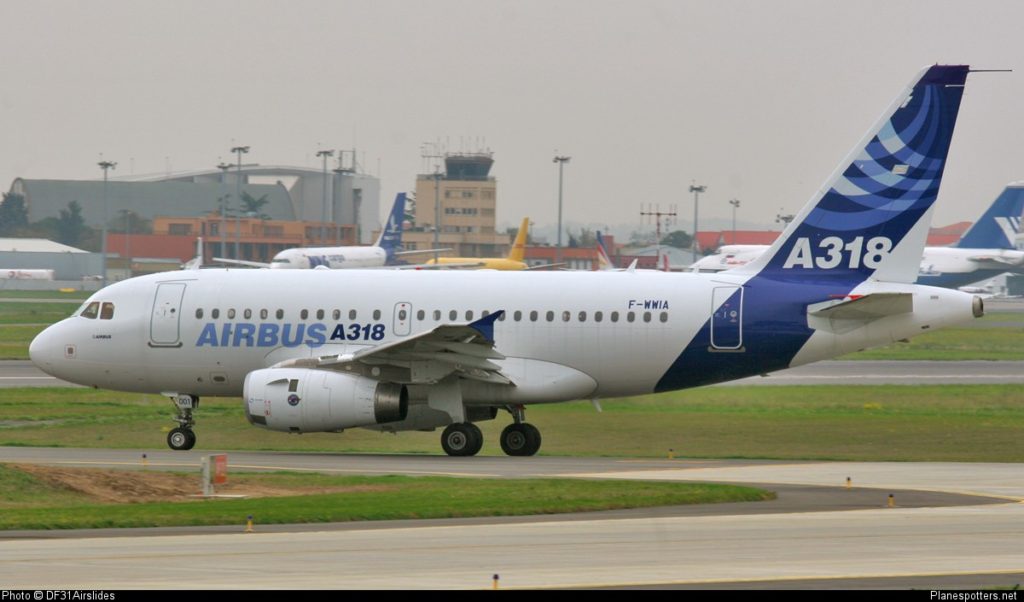
Airbus A318, the plane whose stringers are welded by CO2 laser beams. Courtesy of Airbus.
EADS Airbus have invested heavily in laser welding as a replacement for riveting in non-critical applications. One application involves joining stiffening stringers to the skin of the fuselage. The stringers are welded from two sides at 10m per minute, using two 2.5kW CO2 laser beams. This design limits the heat affected zone (HAZ) within the stringer, and does not impinge on the skin. It took almost 10 years for the approach to be sufficiently mature for this application. Now the process is working in series production of the Airbus 318, and will play a vital role in more future aircraft types.
Comparison with Electron Beam Welding
Of all the competing welding methods, the principle of electron beam welding is the closest to that of laser keyhole welding. It utilizes a focused high-energy beam of electrons rather than photons to create keyhole and occurs within a vacuum chamber. This guarantees that contaminants do not jeopardize welding quality. Electron beam welding is particularly effective for joining thick parts of up to 100 mm. Moreover, since reflective alloys such as aluminum and copper contain many free electrons, they are more amenable to welding by electrons than photons. Additional benefits of using electron beam welding are low distortion and high penetration under high welding speeds.
Despite of these advantages, laser welding still wins in many aspects. First, the size of the vacuum chamber imposes limits on workpiece in the plan of electron beams. Also, while laser beams can switch between workstations to eliminate down time, loading and pumping of the vacuum chambers can take up to several minutes, leading to low productivity. Furthermore, electron beam welding systems might encounter more practical problems. For example, welding parts of certain geometry may be difficult because electron beam unit cannot move close to the joint line. However similar problems do not happen in laser welding systems as optics with long focal lengths can provide a large stand-off distance. Also, both magnetic and electric fields can easily affect electron beams. More importantly, electron beam welding performs poorly on parts with dissimilar electromagnetic properties.
Comparison with Fusion Welding
Fusion welding is another type of competing joining approach. Two representatives of it are MIG (metal inert gas) and MAG (metal active gas). They achieve welding by an electric arc and an inert shielding gas and CO2. MIG is particularly suitable for welding aluminum and its alloys, and MAG primarily targets carbon steels, low alloy steels and stainless steels. Fusion welding processes have a number of favorable properties. First, they can work in both manual and automatic modes, and secondly, the operations are easy to learn. Also, if multiple passes are implemented, MIG and MAG are able to work on many common metals and alloys with a wide range of plate thicknesses and welding positions.
Compared with laser welding, fusion welding techniques suffer from several disadvantages. The most prominent one is the high energy input, which results in greater distortion in welded parts. Additionally, because of a hemispherical or elliptical weld-bead formation, a single-pass welding has limited penetration. Because of this, joining thick parts requires special pre-treatment prior to welding. Thus, laser welding approaches are usually preferable when a single pass, fully penetrating weld of low distortion is required. Most importantly, laser welding demonstrates better performance on long welds with a regular geometry. For high throughputs, the procedures can further be simplified as no joint preparation is needed for thick parts.
If you liked this article, please share and subscribe!