Introduction
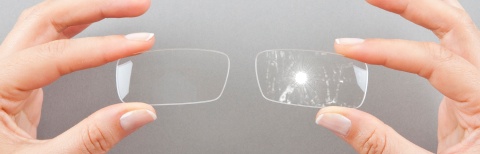
Coated (left) vs Uncoated (right). Both are equally transparent glasses. Courtesy of Metsuki
While materials like glass have the wonderful property of transparency, they also reflect a huge amount of light. This reduces their see-through characteristic. Anti-reflective (AR) coatings, as their name suggests, are thin smooth transparent layers applied on a surface to remove the glare being reflected.
The possibility of anti-reflection is easy to assume. Because, why can’t some substance exist that is completely transparent and absolutely non-reflective? In short, a material that is like a one-way door for light. But the actualization of anti-reflection is far trickier than we might expect. In fact there aren’t any such ‘special’ materials. Anti-reflection is a consequence of light’s wavelike behavior and the geometry of the mediums it passes through.
Invention of AR Coatings
In the late 1800s, Lord Rayleigh, a British Nobel prize winning physicist, first discovered the strange phenomenon of anti-reflection. Glass reacted with the environment and tarnished with time. So Rayleigh was finding a counter to this degradation of transparency. But to his surprise, he discovered that a slightly tarnished glass in fact allowed more light through than a brand new one.
In 1935, Olexander Smakula, a Soviet physicist, rediscovered and perfected the technique of AR coating. Consequently, he is widely regarded as the inventor of AR coatings. Although a major breakthrough in optical technology, the German military successfully kept it as a secret until the beginnings of World War II. And this led to a parallel research conducted by Katharine Blodgett in the United States. Incidentally, she was the first woman to receive a PHD upon successfully developing her ‘invisible’ glass. Also, Blodgett achieved anti-reflection simply with a layer of watery soap films.
AR Coating Specifications
Industry-made AR coating initially centered around high-end optics research. For the process of putting a thin transparent layer (usually under 100 nanometers) without degrading the overall optical quality was costly. However, with the recent breakthroughs in nanotechnology, commercial use of AR is becoming more and more viable.
Magnesium Floride – MgF2 – is the most common AR coating material used today. MgF2 is relatively cheap and has the desired coating properties. MgF2 layers are typically as thin as 50 nm and block almost all reflected light in the visible range.
There are a variety of materials used as AR coating, each one suited to best block reflected light in specific ranges of the electromagnetic spectrum. The shorter the incident wavelengths get, the thinner the layer needs to be to block these reflections. UV-AR is a popular layering material for blocking UV rays, which requires thinner layering at about 5-10 nm.
Below is a diagram showing the different materials and the range over which they work for blocking reflected light.
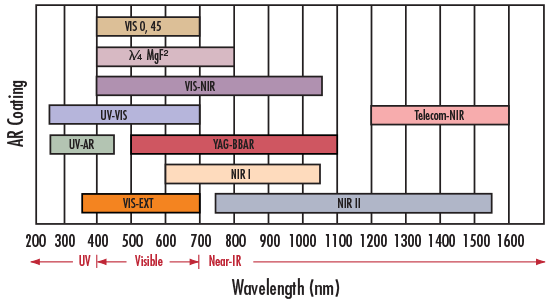
AR coating materials by their respective wavelength range. Courtesy of Edmund Optics
AR in Cutting Edge Optics
Research with lasers demands a high level of precision. Modern laser experiments work with complicated set-ups, using multiple lenses, beam splitters and mirrors. Sometimes a single beam deviates multiple times before it reaches the detector. All such optical devices in its path must have specialized AR coating to be resistant to temperature and pressure differences. On the other hand, lasers typically operate around a single wavelength, which does simplify the coating process a little.
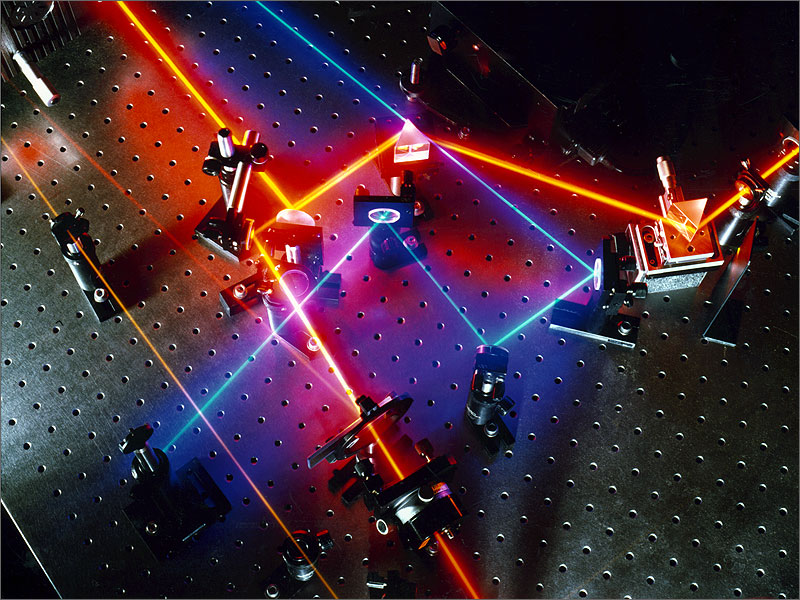
A regular laser experiment. Every path deviation of the laser beam brings in additional reflection and scattering components. Courtesy of ErekAlert
Current astronomy pushes the limits of detecting faint radiation. Vital information is lost if radiation is reflected. Additionally, it also produces unwanted noise due to scattering. Reflected rays from telescope lenses produce unwanted stray light as they bounce around in the interior. This lowers the quality of the observation. Some convex lenses have multiple AR layers that can bring reflection down to 0.01%. Accordingly, the process is complex and expensive. However there is the additional benefit of anti-reflection at angles outside normal incidence.
Additionally, more and more astronomy is focused around individual wavelengths instead of a range of them. As in the case with lasers, AR coating process simplifies when targeting limited wavelengths.
AR in Consumer Products
In our era of online social networks, popularity in photography has greatly increased. And camera companies are bringing in all sorts of tech for their digital and smartphone products. All camera lenses have AR coatings, making cameras and smartphones the biggest market for the AR tech. That is, any picture involving incoming light such as during sunrises, sunsets, or street lights at night, would contain unwanted effects. AR coated camera lenses can produce far better contrast ratios by removing such noise captured by the sensor.
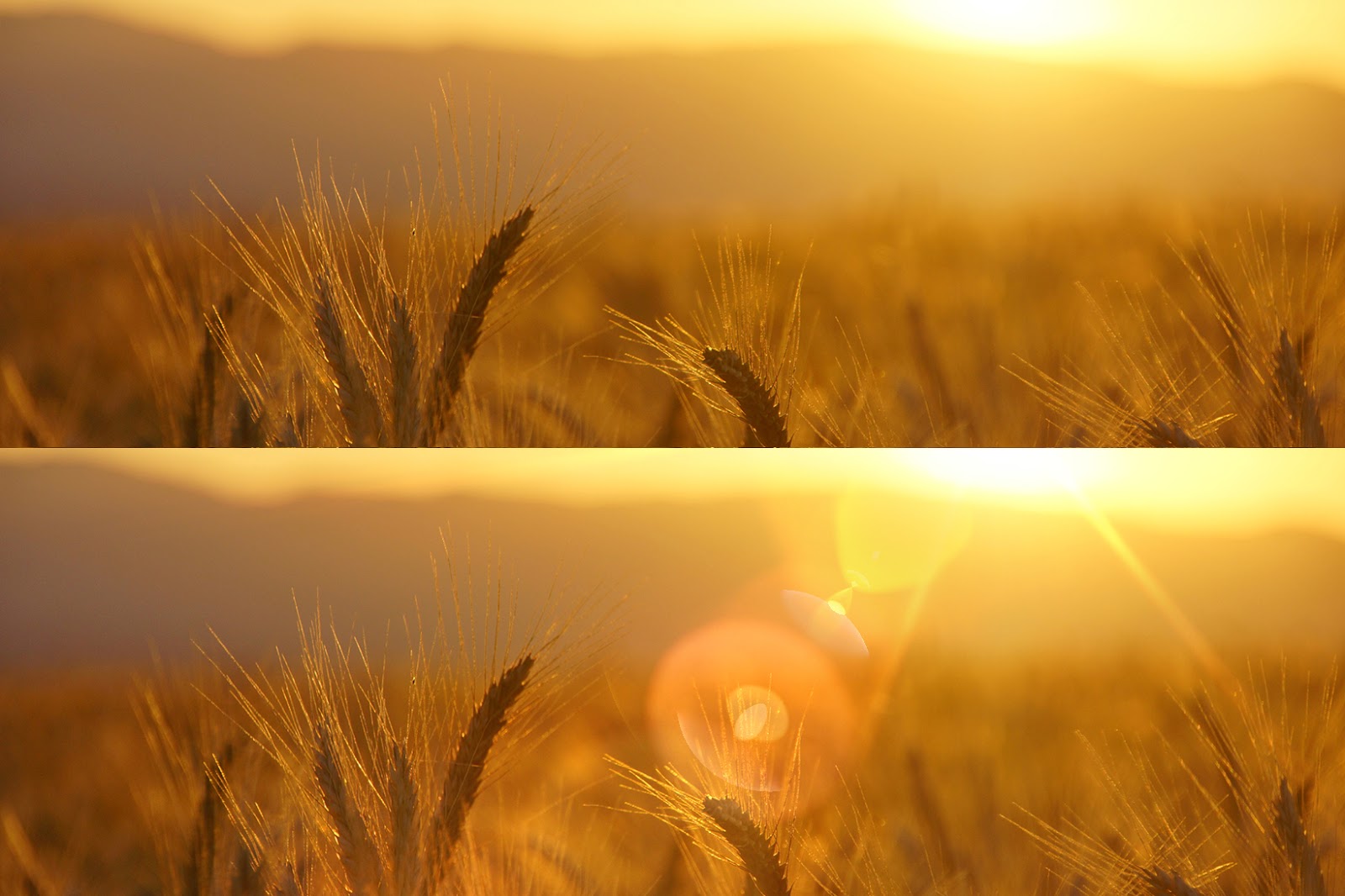
Camera lenses with coating (top) eliminate lens aberrations otherwise formed by incident light (bottom). Courtesy of Wallpapers
Opticians no longer view AR coating in corrective lenses as a luxury. In some countries like Japan, there is an 80% market penetration. Indeed, it is definitely a major draw to its customers. Reducing the glint and making the eyes more visible to others is a must. Especially in our times of selfies and video chats. But the viewers themselves also benefit as they perceive less peripheral glare. Moreover, this greatly reduces strain. And viewers are less likely to remove their specs.
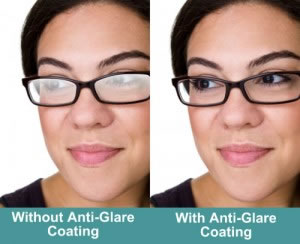
AR coated glasses are visually pleasing due to their invisible surface. Courtesy of ReplaceALens
With ever-improving processes in manufacturing, AR coating is finding its way into any product that has some transparent sheet. Indeed, most modern cars have AR coating on their headlights. Switched on lights no longer produce halos around them. Watches, interior windows, glass cabinets, projector lamps, all have AR coatings as an option for those who can afford.
Limitations of AR
Maintaining AR coated lenses is a challenge. While scratches in any optical lens is bad, the AR layer makes scratches much more visible. The reflection of the glass increases if the thin coating is scrapped off. Cleaning with water is essential to avoid this. AR also works best for light falling normal or perpendicular to the transparent surface. As the angle increases, the range over which anti-reflection occurs reduces.