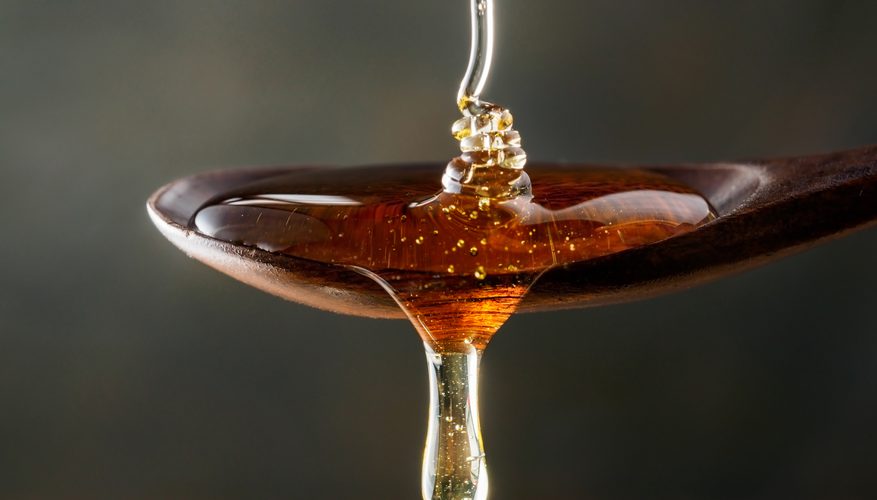
Viscosity is a defining property of a liquid. Quick and accurate measurements are crucial in analyzing the quality of films, dairy products, and even blood tests. Courtesy of Sciencing.
A research team at Keio University in Japan devised a novel handheld viscosity sensor capable of quick, non-contact in situ measurements. Viscosity is a fundamental property for liquid analysis in a wide variety of applications and fields. Dairy companies, for example, rely on viscosity measurements to determine product quality. These measurements are also prevalent in medicine, as blood viscosity can indicate an assortment of diseases including diabetes and cardiovascular disease. Efficient and accurate viscosity measurements are essential for diagnosis.
A simplified definition of viscosity describes relative resistance of a fluid to deformation due to friction between different molecules. Picture a tube of toothpaste: high viscosity pastes would be difficult to squeeze out while a low viscosity would flow too quickly. We can clearly witness the effects, but measuring viscosity proves to be a little more challenging. Current methods suffer from long sample times and require large volumes of each sample.
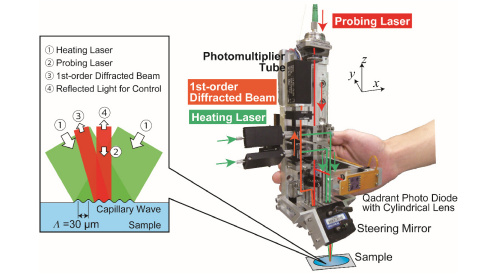
The above figure shows the placement of the different beams in the handheld device. Courtesy of OSA Publishing.
How it Works
The handheld device first generates an interference fringe pattern by heating the sample surface with two pulsed laser beams. Heating at the surface creates a capillary wave which oscillates and decays. This “relaxation process” is dependent on many properties of the sample including density, surface tension, and most importantly, viscosity. Researchers are then able to access numerical viscosity data by analyzing the temporal behavior of the capillary wave. We can directly observe this behavior because the intensity of the first-order diffracted beam generated from the interference fringe is proportional to the square of the capillary wave amplitude. Therefore, we can optically monitor the capillary wave by detecting the first-order diffracted beam.
The Non-Contact Handheld Viscosity Sensor
The heating laser source emits two beams and a probing laser that couple into the handheld device via optical fibers. This single-mode fiber has a large core diameter to allow for high-energy pulse delivery. The optical heating is created with a YAG laser and the probing beam emits from a diode. The first-order beam that describes the behavior of the capillary wave is detected by a photomultiplier tube. A two-axis steering mirror controls the incident angle of the three beams while a focal-point detection system controls irradiation time.
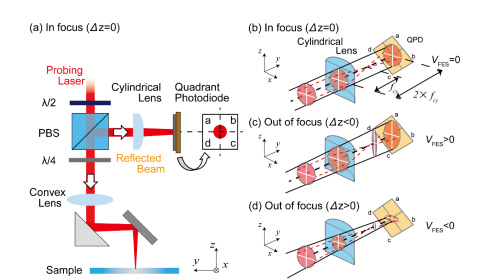
Here we see how the device corrects for hand vibration during operation. Courtesy of OSA Publishing.
The device features an incident angle control system that compensates for hand vibration during operation. When optimized, the probing laser should enter the sample vertically so that the reflected beam from the surface hits the center of a photodiode. The team inserted a quarter-wave plate and polarized beam splitter into the system so that the reflected probing beam changes position on the photodiode as a function of the incident angle. Feedback through the two-axis steering therefore compensates for changes in incident angle by correcting the reflected beam back to the center of the photodiode.
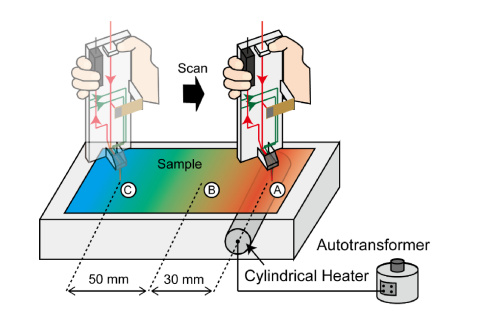
The above figure shows the experimental setup of interest. We see how points A, B, C vary in temperature based on position from the cylindrical heater. Courtesy of OSA Publishing
The Results
The team first tested their angle-stabilizing system by comparing signal dispersion with and without feedback. They confirmed their proposed control system provided high stability.
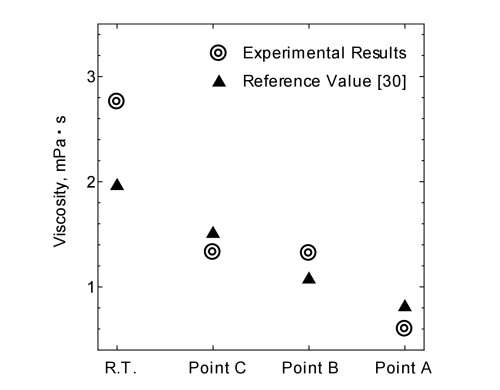
It is important to note there was indeterminable temperature deviation between reference and measured values because the measurement locations are indefinite within the sample. Courtesy of OSA Publishing.
For their main experiment, the team tested viscosity distribution of a sample fluid. The fluid consists of 20% sucrose aqueous solution with amorphous carbon for laser beam absorption. A cylindrical heater placed at one end of the sample created thermal distribution throughout so that the team could test three different positions, each with distinct temperatures and viscosities. The first-order diffracted signal was detected at each point from the low to high temperatures. While the acquired data shows significant deviance (about 30%) between measured and reference values in the high viscous region, we still see the expected viscosity trend with temperature. The team proposes more accurate measurements can be attained by changing the fringe spacing to improve the signal-to-noise ratio. Regardless, the experimental results prove that the handheld non-contact sensor is a valid method of viscosity measurement.
The Keio team has designed a non-contact device capable of rapid viscosity measurements. The handheld viscosity sensor with incident angle could be easily adapted into a long list of industrial and medical uses. The device also requires much smaller sample sizes compared to standard measurement methods, once again lending itself to mass-production applications.
For more on the principles behind their novel sensor, read the Keio team’s paper here.