Beam profiling systems are an essential technology to ensure the quality and uniformity of lasers. Beam profilers measure the optical spatial intensity of an input laser beam, providing information about the uniformity of the beam over time as well as over different regions of the beam. Lasers are used everywhere – transmitting signals, spectroscopy, manufacturing, and numerous other domains – so it is imperative that the applied laser beam is properly calibrated in its beam properties and consistency to a high degree of precision.
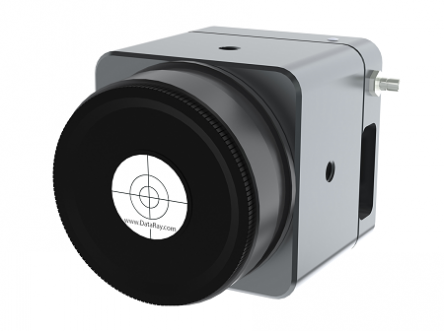
TaperCamD-LCM CMOS Based Beam Profiler by DataRay.
The important qualities of a laser beam that can be derived from the intensity reading of a beam profiler include the beam radius, profile (chart of beam intensity at any point along its path), wander (the degree to which the beam shifts over time), divergence angle (angle by which the beam spreads over its distance), width at beam waist, waist location, astigmatism, and beam quality (given by the parameter M^2, the product of the divergence angle and waist radius). However, the vast number of laser applications lends itself to a commensurately diverse number of different laser beams, meaning no single beam profiler is adequate for every job.
What are the different types of beam profiling systems?
There are two main types of laser beam profiling systems available on the market – camera-based profilers and knife-edge or scanning-slit beam profilers. Camera-based beam profilers involve directly shining the laser on a CCD or CMOS sensor to directly measure the intensity of the laser beam profile down to a specific pixel-based resolution. Camera-based laser profilers are the most commonly used systems on the market today. Knife-edge profilers utilize a rotating blade or “knife” to allow portions of the laser signal to be analyzed by a power meter, after which software is able to reconstruct the full beam profile. The advantage of knife-edge beam profilers is their typically excellent diffraction-controlled lower resolution limits, which are generally on the order of microns (compared to the tens of microns seen in camera-based beam profilers). However, knife-edge beam profilers are only suitable for continuous laser sources, and not pulsed lasers.
For camera-based beam profiling systems, it is usually necessary to attenuate the beam being measured dependent on the sensitivity of the beam profiling system in use by using ND filters. This is not generally necessary for knife-edge beam profiling systems due to the small cross-sectional area of the beam that is analyzed at any given time. One disadvantage of knife-edge beam profiling systems is that they generally only measure the beam on a few axes of the beam, which does not provide information about the beam perpendicular to its direction of travel on the edge.
CCD or CMOS camera-based systems?
In choosing a camera-based beam profiling system, you also need to take into account the imaging system – CCD or CMOS? A CCD, or charge-coupled device, image sensor utilizes a matrix of photosensitive cells that shuffle photoelectrons from each cell to a single readout amplifier, which allows each cell to devote all of its utility to converting a light signal to an electronic signal. It also tends to reduce noise in the outputted digital signal, but requires more time for readout.
CMOS, or complementary metal-oxide-semiconductor, image sensor systems, on the other hand, consist of amplifier readouts for each photosensitive cell which convert the analog light input to an electronic voltage. While such a setup can increase complexity, CMOS image sensors are often seen as beneficial due to their higher transmission bandwidth and tend to have lower costs due to the lack of an external electronic structure to shuffle and interpret signals present in CCD systems.
These days, most beam profilers utilize a CMOS image sensor due to their lower cost and ease of manufacture. As mentioned, CMOS systems tend to have a higher bandwidth, allowing for faster image processing and typically lower power consumption. Additionally, CCD systems are prone to oversaturating the signal in a cell, “spilling” its extra signal into neighboring cells and producing a bloom effect into the digital signal. While this is typically mitigated in CMOS imagers due to the parallelism of analog/digital conversion, it can be more difficult to correct when it does happen due to the abundance of active electronics on board that all need to be put into a low-voltage state for noise correction. However, as CMOS technology develops and noise-correction techniques continue to improve, we can expect CMOS-based image sensors to continue to dominate the market.
Choosing a beam profiling system for your application
Different beam profiles for various applications. Courtesy of UCSD
Beam profiling systems are exceedingly important for a number of diverse applications. Whether you are profiling a beam for fiber optics, manufacturing, or medical instruments, knowledge of the uniformity and stability of a beam can make or break laser-based instrumentation. For example, lack of knowledge of the mode pattern of a laser in manufacturing can result in non-uniform cuts or introducing unwanted defects into the material being manufactured.
The first factor that must be taken into consideration is the size and shape of the laser beam you are using. Prior knowledge of laser beam size is essential, especially for focused beam spots on the order of microns. At such low dimensions, camera-based beam profiling systems become infeasible, as camera-based systems generally have an overall sensitive area on the order of millimeters. This can be overcome with the use of beam expanders or large area sensors. On the other hand, if your beam is too large for the sensor area, a beam expander in reverse can be used.
The shape of the laser beam will also influence the techniques used for beam profiling. Typically, a gaussian-profile beam is used for applications where it is desirable to concentrate a laser beam on a single point. Another beam profile that might be desired is a flat-top profile for uniform distribution over an area (used in Photorefractive Keratectomy) or an elliptical beam profile for laser manufacturing purposes. The differences in power densities dependent on beam shape necessitate different levels of beam attenuation if using a camera-based beam profiling system.
For more information on beam profiling systems, check out our previous article on beam profiling systems and FindLight’s array of beam profilers.