Introduction
Using the technique of keyhole laser welding, we can use very high beam intensities to process the material (please see this reference for the details of keyhole laser welding technique). Due to the substrate’s quick melting and evaporation during laser keyhole welding, the interaction between the keyhole and laser beam is quite unstable. The welding process is greatly impacted by fluctuations in the laser beam absorptance caused by unsteady keyhole motions. In the context of laser welding, it is important to anticipate the shape of the keyhole and the laser absorptance inside the keyhole. In this article, we discuss a novel real-time full-penetration laser keyhole welding monitoring system introduced by the researchers in the department of mechanical engineering at Ulsan National Institute of Science and Technology.
In order to assess the cavity development and its suppression in pulsed and continuous-wave laser welding, some researchers use high-speed optical and X-ray transmission technologies to study the keyhole and plume dynamics in real time. The researchers observe the dynamics of the keyhole and laser-induced plasma in the molten pool, where the keyhole fluctuated and the laser-induced plasma is periodically created. Additionally, the welding procedure includes measurements of the creation of porosity.
In order to enable the direct and clear observation of the longitudinal keyhole wall via high-speed imaging and to clarify the mechanisms underlying the formation of spatter during high-power fiber laser welding, other researchers propose a modified sandwich sample made of stainless steel and GG17 glass. To evaluate the bulge and constriction/protrusion on the rear keyhole walls and to study the spatter discharged due to the tiny keyhole entrance, the side keyhole walls and liquid movements are clearly and directly observed.
The dynamic coupling between the keyhole and molten pool in full-penetration laser keyhole welding is simulated using a 3-D model and the ray-tracing technique, and the upper and lower surfaces of the molten pool are observed using two synchronized high-speed charge-coupled device cameras to confirm the simulation results.
The results of the simulation, which take into account multiple reflections, can be validated by the simultaneous inspection of the upper and lower surfaces, and the researchers realized that the laser beam passed through the keyhole without coming into touch with the specimens.
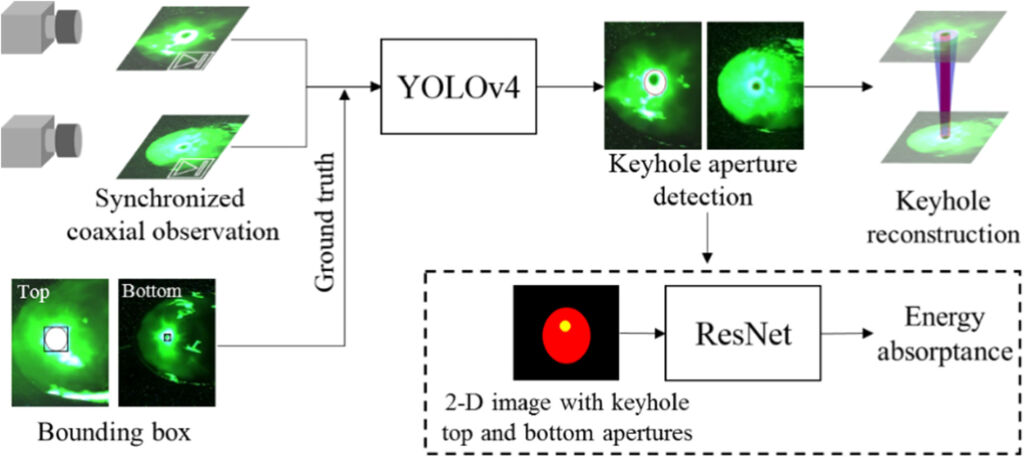
Figure 1: Outline of the proposed deep learning real-time monitoring system for laser keyhole welding; Image courtesy of Elsevier
Motivation
To examine the top and bottom surfaces during full-penetration laser keyhole welding, the researchers employ a high-speed coaxial technique. And then the researchers rebuild the time-averaged keyhole and run a statistical analysis on it.
For determining the laser-beam absorptance, the researchers can also run electrodynamic simulations taking into account the various reflections inside the keyhole. They need to accurately measure the keyhole apertures using the coaxial observation technique. The welding procedure is examined using the reconstructed keyhole forms and energy absorptance calculations.
To improve the weld quality in real time while laser welding with an external magnetic field, they can also develop weld seam monitoring by extracting the features of the keyhole and melt pool through grayscale processing and median filtering, which are conventional image processing techniques.
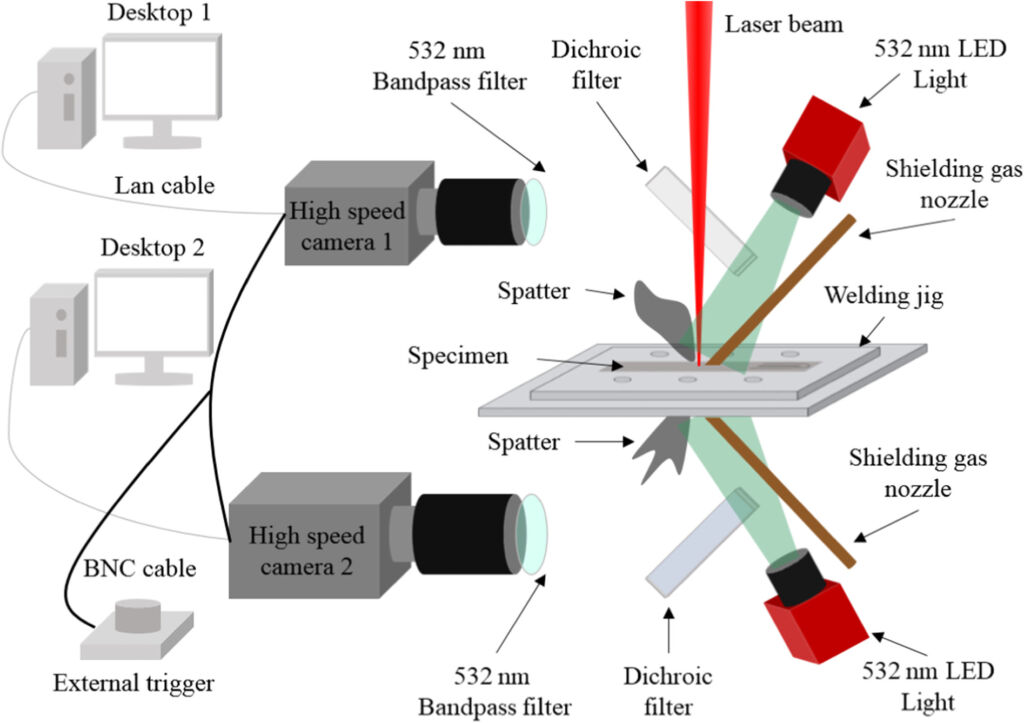
Figure 2: Schematic of synchronized high-speed coaxial observation method; Image courtesy of Elsevier
To recognize the keyhole, weld pool, weld seam, and backdrop, they can create a model based on convolutional neural networks (CNNs). Afterwards, they can couple this model with machine learning techniques to forecast the process parameters and detect errors.
To monitor the fluctuations in keyhole movements and laser absorptance throughout the welding process, the researchers have created a deep-learning-based technique for full-penetration laser keyhole welding. In this technique, the top and bottom welding surfaces are also simultaneously recorded using a synchronized high-speed coaxial observation technique.
They employ a real time object recognition deep learning model to detect the location and size of the keyhole top and bottom apertures by using the images gathered by the suggested high-speed observation method in order to reconstruct the keyhole geometry.
ResNet-34 is a well-known image classification module built on CNN and developed. The researchers use ResNet-34 to predict the laser absorptance from the 2-D image with the keyhole top and bottom apertures in the context of the keyhole structures recreated with a tilted cone. Additionally, they prepare the training data using a ray-tracing technique in their technique. Figure 1 and Figure 2 show the general framework of this novel model.
Data preparation for full-penetration laser keyhole welding
The keyhole aperture measurements collected from the welding process observations are taken into consideration when creating the dataset for the object detection deep-learning model. The measurements of the keyhole aperture have to be distinct because the model training is dependent on the extraction of the features of the keyhole aperture form.
The keyhole top aperture is the bright white area that is emitting powerful heat radiation from the top surface. The keyhole bottom aperture is located at the area of the bottom surface that is black, or anywhere other than the brightest white point.
Figure 3 displays examples of the keyhole top and bottom apertures, denoted by black ellipses. As can be seen in Figure 3, the keyhole top aperture was calculated as an elliptical shape intersecting the bright white portion. Also a blue or green elliptical form contained within a bright white spot and a black spot were noticed in the keyhole bottom aperture.
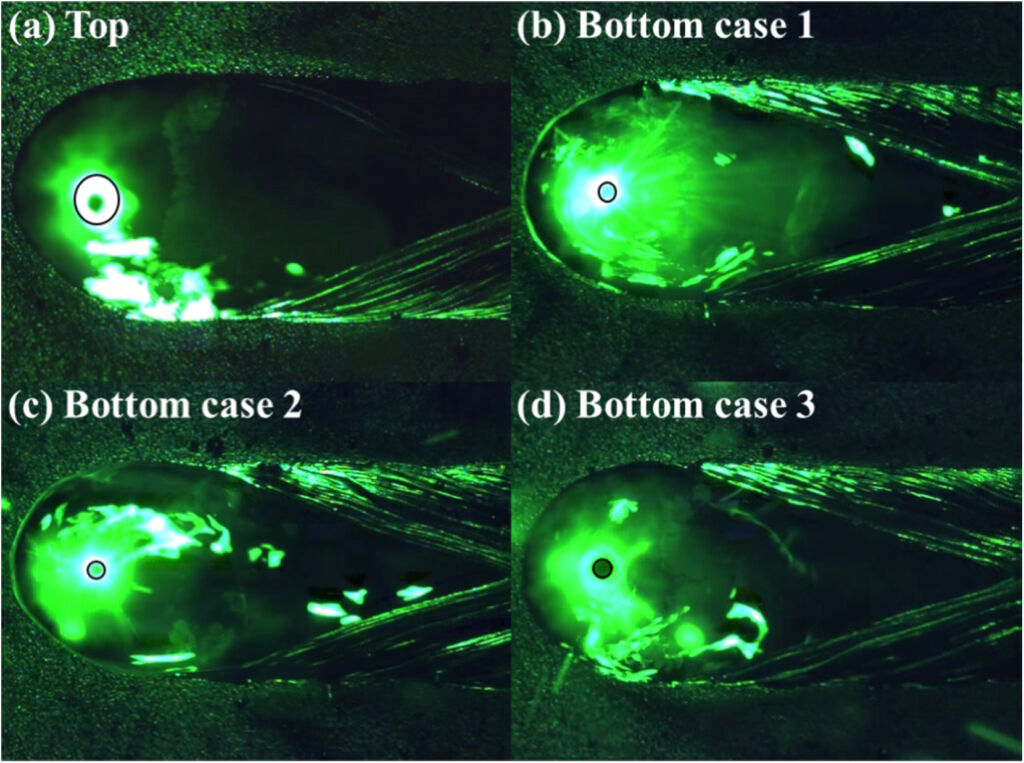
Figure 3: Measurements for the keyhole aperture (black ellipse shape) in laser welding process. (a) Top keyhole aperture, and (b–d) three cases of bottom keyhole aperture; Image courtesy of Elsevier
Results for full-penetration laser keyhole welding
A few examples of the outputs of this case study are shown in Figure 4 and Figure 5. We can summarize the main results and observations of this test case as follows:
- During full-penetration laser keyhole welding, the keyhole’s behavior and laser absorptance vary significantly. The area of the bottom aperture, the number of opened keyhole bottom apertures, and the keyhole’s tilting angle all have an impact on the laser absorptance variation tendency.
- Regions where the laser absorptance significantly decreased could be used to pinpoint the flaws in the laser welding process.
- The pressure inside the keyhole increase as a result of the narrower melt pool when the faults are formed, which typically results in the bottom aperture opening.
- By taking into account the laser absorptance in accordance with the keyhole behavior, the created model may be utilized to analyze full-penetration laser keyhole welding and identify faults.
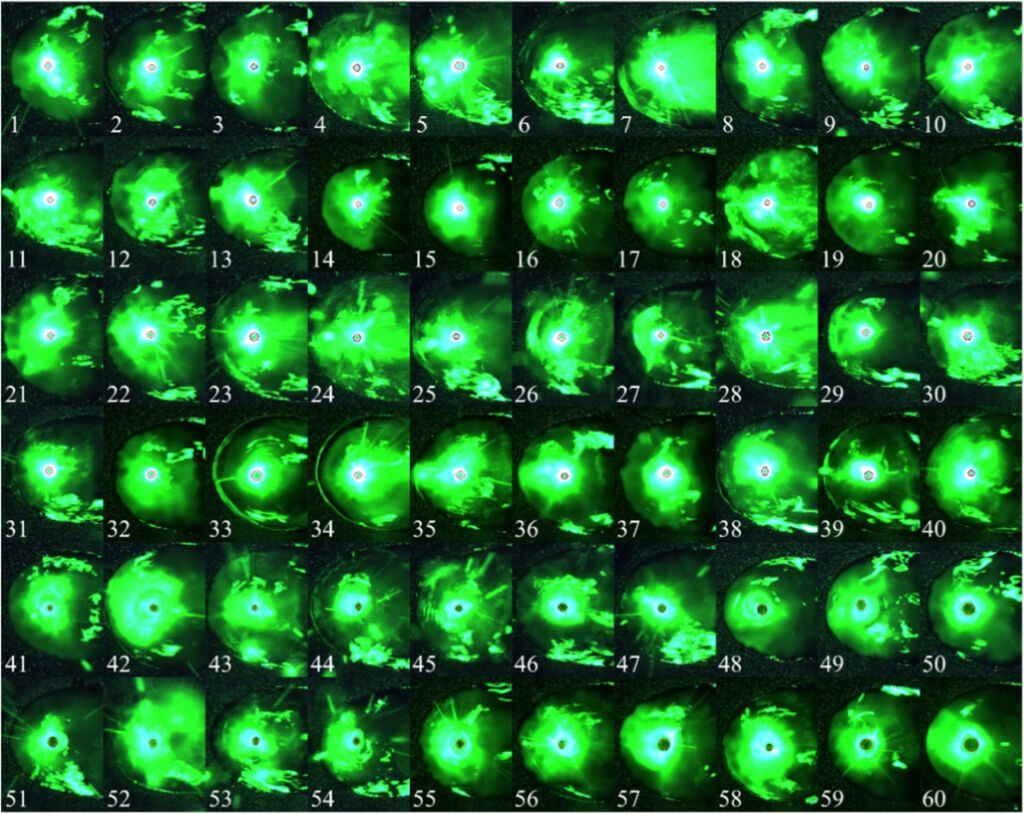
Figure 4: Test results of the model for the keyhole top apertures. Ground truth is shown by black ellipse and prediction by red ellipse; Image courtesy of Elsevier
Summary
In this article, we discussed a method to implement real-time monitoring of full-penetration laser keyhole welding. The main application of this method is to examine the dynamics of the keyhole and changes in the laser absorptance inside the keyhole.
The following are the main points of this article:
- In order to simultaneously examine the top and bottom surfaces of the welding process, the researchers at Ulsan National Institute of Science and Technology use synchronized high-speed coaxial observation.
- Using photos of the welding process, they introduce a deep learning object detection model to autonomously measure the location and size of the keyhole openings.
- From the input keyhole aperture image, they use a ResNet-34 image classification model to forecast the laser absorptance.
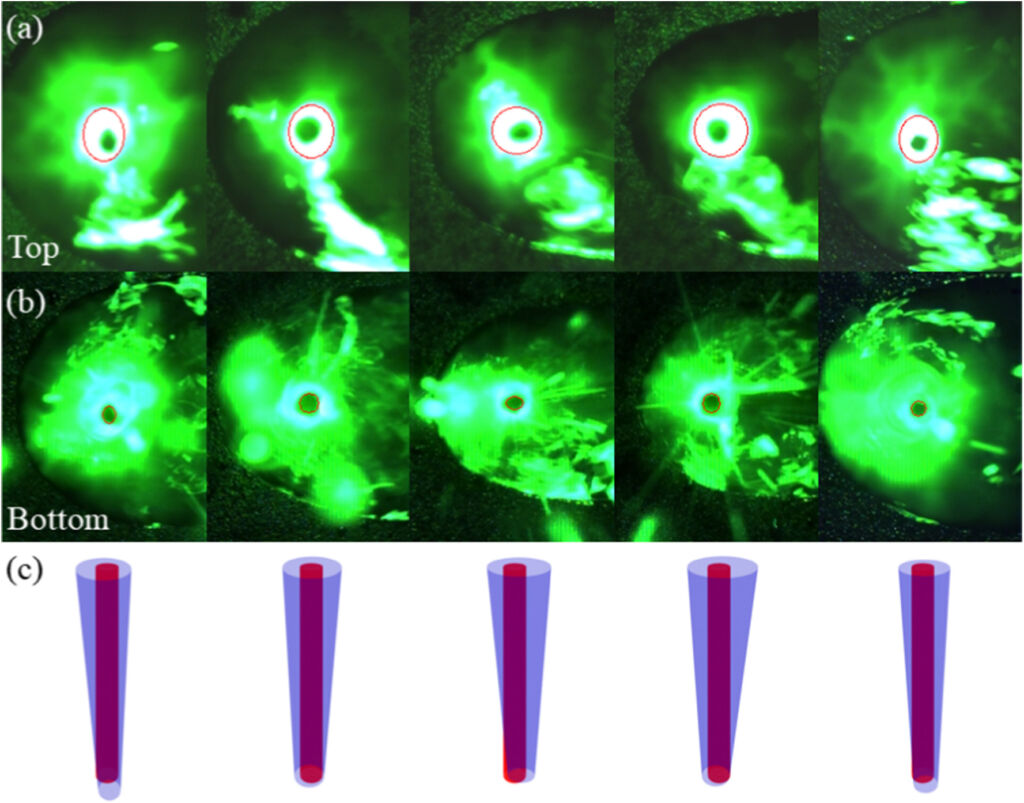
Figure 5: Examples of (c) reconstructed keyhole geometry (blue tilted conical shape) and laser beam (red cylinder shape) based on the keyhole (a) top and (b) bottom apertures detected using the model (red ellipse); Image courtesy of Elsevier
This article is brought to you by World Star Tech, a provider of laser solutions for material processing applications