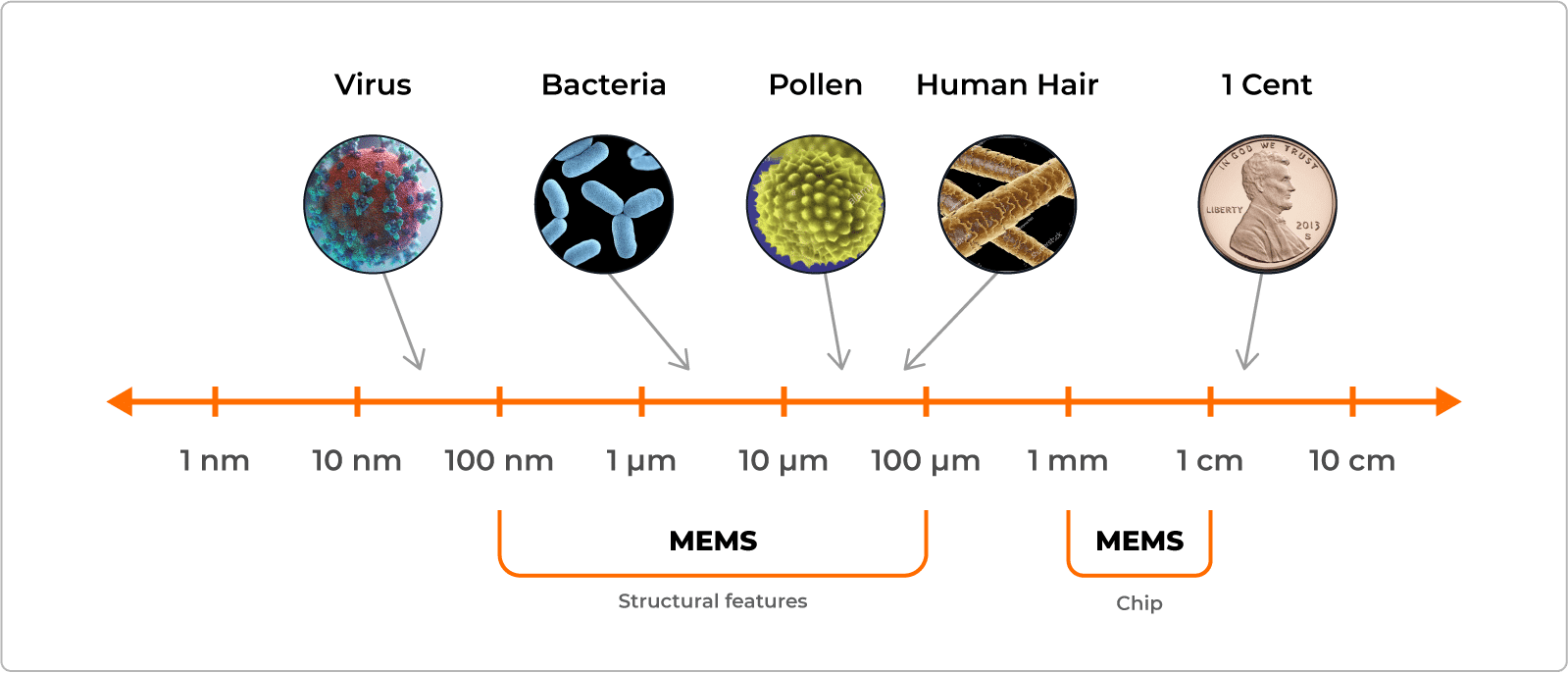
Introduction to MEMS technology which exists at an extremely small scale, with everything being smaller than a single penny. Image courtesy of Atamica.com
Have you ever considered how small something could be? What would limit how small we can make things? How precise exactly is “ultra precision”? Today we will have an introduction into microscopic technology and look at examples of Micro-Electromechanical Systems, MEMS for short.
Perhaps movies and tv shows have brought you to dismiss the prospect of microscopic technology as nothing more than science fiction screen magic. Or perhaps you know that some micro-tech must exist even if it the technology in its infancy, enter MEMS.
1. An introduction to MEMS Technology?
A Micro-Electromechanical System is as the name suggests: a process technology which is used to create microscopic integrated devices or systems that can combine mechanical or electrical components at a micrometer scale. Many techniques used to create integrated circuits have been retooled to create these devices.
These devices are on the order of micrometers for structures and can result in chips at the size of a few millimeters. As a result of their size they can only truly be seen in detail under the lens of powerful microscopes. This technology is the kind that fits on the tip of your finger while maintaining a sophisticated set of operations it can perform from drilling and pumping to measuring data and returning information.
2. Why do we integrate MEMS technology?
The nature of the microscopic technology is one of precision and minimal space/material usage. Modern smartphones require so many ICs and sensors from cameras to accelerometers which are all expected to fit in the palm of one’s hand. Human technology has been trending to be more compact and smaller to create more convenient devices.
A fine example of MEMS usage would be the use of ultra precise MEMS accelerometers in automotive vehicles. These devices are used to detect extreme changes in acceleration in order to immediately deploy airbags in the event of an impact. As the diagram shows below, a crash sensor is used to trigger the airbags in the event of a collision. The bag then inflates almost instantaneously once triggered.
An extremely responsive sensor would be needed to trigger the airbags within milliseconds of an impact. Objects with larger mass have more inertia and as a result require more force/time to be set in motion. Inertial influence is normally negligible, but this is not the case in the context of crash safety. A heavy accelerometer means that the response time could be slower. Using a MEMS accelerometer results in a split second difference that could deploy airbags sooner and save lives.
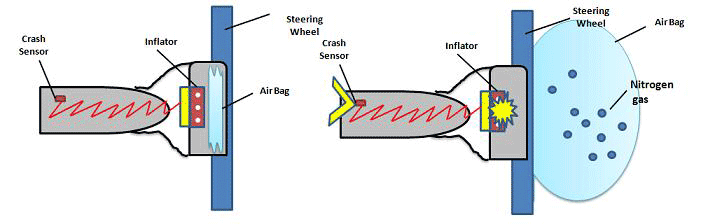
Air bags work via a sensor used to trigger deployment of bag. Image courtesy of Clemson.edu
To maximize safety, the crash sensor must be able to detect a collision incredibly precisely which is best done with a MEMS accelerometer. MEMS technology takes up very little space. A correctly selected accelerometer can be rated for up to 200+ g of force. Due to the small inertial influence in MEMS their responsiveness is very good. For these reasons it becomes apparent why MEMS accelerometers are a good choice for vehicle safety.
The mechanism used for MEMS accelerometers is normally a capacitive mechanism (as seen below) in nature. We use capacitive mechanisms because electric forces dominate the micro world more than magnetic forces. The reason for this is simply because as items scale down the strength of generated magnetic fields diminishes while the relative strength of electric fields increases.

MEMS accelerometers utilize a capacitive differential mechanism. Image courtesy of ResearchGate.com
3. Technologies developed through MEMS
To continue this introduction to MEMS technology we will look at various technologies developed through MEMS which include but are not limited to:
- MEMS switch matrices: One impressive piece of technology using MEMS is this switch matrix containing 192 ports with the ability to dynamically switch connections from one port to another in such a way that any of the inputs can connect to any of the outputs in a completely non-interrupting cross connecting dynamic configurations.

An impressive use of MEMS technology using tilted mirrors to connect inputs and outputs. Image courtesy of FindLight.net
- MEMS pumps: Another realm of MEMS technological development is the industry of pumps wherein extremely precise pumps can have applications in medical procedures where microflow is required to have extreme precision.
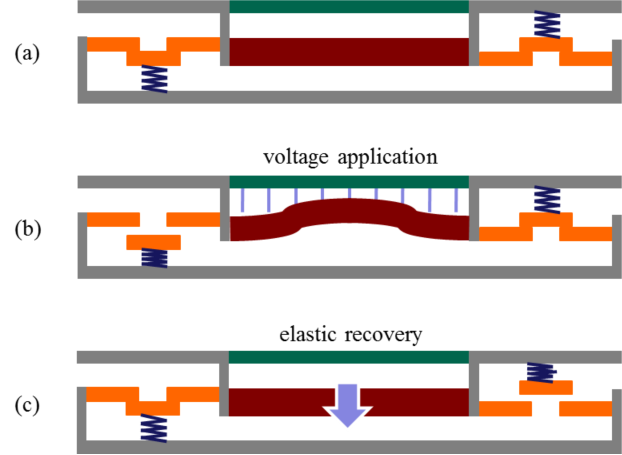
MEMS pumps utilize elastic recovery as a mechanism to pump fluids in this example. Image courtesy of MEMS.polimi.it
- MEMS gears: On a more raw mechanical side, we have managed to create miniature gear trains which boast the main benefit of having near negligible inertia due to each gear having such little mass. The implications of having next to no inertial forces impeding the gear trains means almost instantaneous start ups and very quick stop times where larger gears would need significantly more time to start/stop.

MEMS gears which have very little inertia. Image courtesy of Concordia.ca
- MEMS accelerometers: Using differential capacitor mechanisms like seen below, constructions of arrays of these structures can result in much more accuracy for little increase in volume given that these structures are on the order of a couple microns in thickness and width.
This is an example of multiple capacitive accelerometers placed side by side in an array. Image courtesy of Digikey.com
4. The unexpected side of MEMS and “tiny things”
Due to the scale of the technology, MEMS devices need to consider forces that we would normally consider negligible. Such are the static electricity, friction, low terminal velocities, all forces that are impacted by the ratio between mass and surface area.
Prime examples of this are how surface based forces (i.e., electrical force or adhesion) become the dominating forces over mass based forces (such as magnetism and momentum). This leads to normally more negligible things, such as terminal velocity or capillary action, which become something that needs to be considered for such small devices.
A real-life example would be in how dust particles can seemingly float on the air. Dust’s terminal velocity is virtually zero because relative to its surface area there is very little mass for gravity to pull the dust to the ground. This kind of behavior is not intuitive to us since we experience the universe at a much larger size. However, when the governing equations are assessed the behavior begins to make sense despite being impossible at our normal human sized scale.
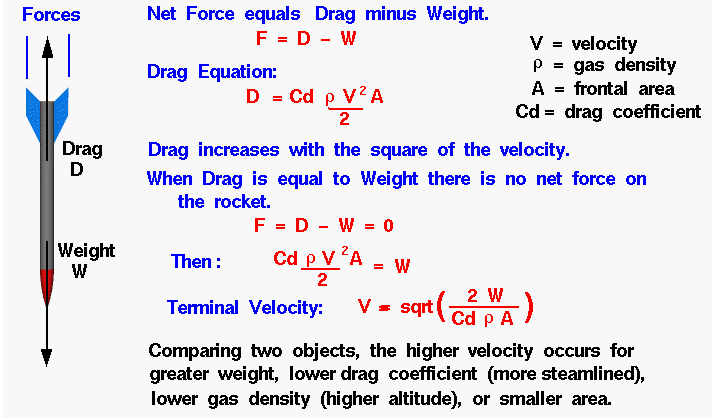
The governing equations regarding drag and terminal velocities. Image courtesy of NASA
As seen in the terminal velocity definition, higher velocities will occur when there is more weight and smaller area. The squared cube rule helps us understand that reducing size impacts mass/volume more intensely than it impacts area. So under the terminal velocity equation we can consider the limits, as W (weight) goes to zero exponentially and A (area) goes to zero linearly.
The resulting observation is that when scaling down, terminal velocity will reduce significantly.
5. Conclusion
To conclude our introduction to MEMS technology, it can simply be stated that Micro-Electromechanical Systems are impressive feats of human technology developing in various industries around the world. The technology has many benefits such as using less material and taking up less space while also being so small that forces that are negligible at our normal human scale suddenly become the dominating force in the “micro-world”. MEMS technology is most certainly worth keeping an eye on as it develops.
This article is brought to you by RPMC Lasers Inc., a leading manufacturer and distributor of laser technologies in North America.