Developments in combination laser processing techniques have the potential to improve the manufacturing of metal parts. Researchers at the University of Basque Country proposed a combination of Laser Metal Deposition, Laser Beam Machining, and Laser Polishing to manufacture parts of a nickel-chromium superalloy without the use of other manufacturing techniques. By employing methods based on the use of lasers, wasted material is reduced, as are the size of the Heat Affected Zone and any thermally-induced distortions. The overall manufacturing process is cleaner and more environmentally friendly. However, the rate of this combination laser processing technique is slower than that of traditional manufacturing techniques, and is only advantageous with difficult-to-cut materials and with highly detailed parts.
Laser Metal Deposition
To manufacture the alloy product, Laser Metal Deposition, Laser Beam Machining, and Laser Polishing were used, in that order. Laser Metal Deposition (LMD) is a form of additive manufacturing. Additive manufacturing is commonly seen in commercial 3D printers. In the experiment described in the paper, a 1kW continuous wave fiber laser deposits the nickel-chromium test part onto the substrate surface. LMD produces parts that still require further processing to ensure correct dimensions and surface qualities.
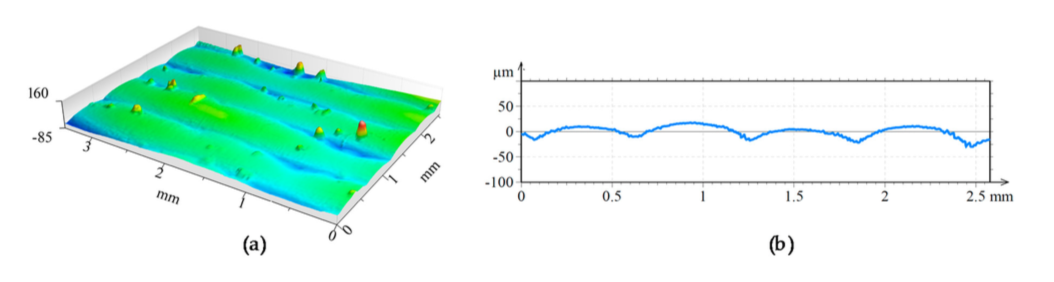
This figure displays (a) the topography and (b) surface profile of the alloy’s surface following LMD. Image Courtesy of MDPI.
Laser Beam Machining
Laser Beam Machining (LBM) works to eliminate more waste material through melting and vaporizing. It is dependent on a pulsed laser, and requires no further tools. The laser is manually focused on a specific area of the part’s surface, and removes the material in this area over a series of repetition. Researchers utilized confocal microscopy to determine optimum parameters for this step, and to quantify progress of the LBM. This step required continuous input and regulations by researchers, to identify upon which area the laser should be focused. The 50W laser was capable of removing the wavy surface and excess material caused by the LMD process. However, it could only remove material located less than 1.6mm away from the focal plane position. Additionally, the removal rate of LMD is 8.3 x 10-3 g/min, which is significantly slower than traditional machining processes used to remove material.
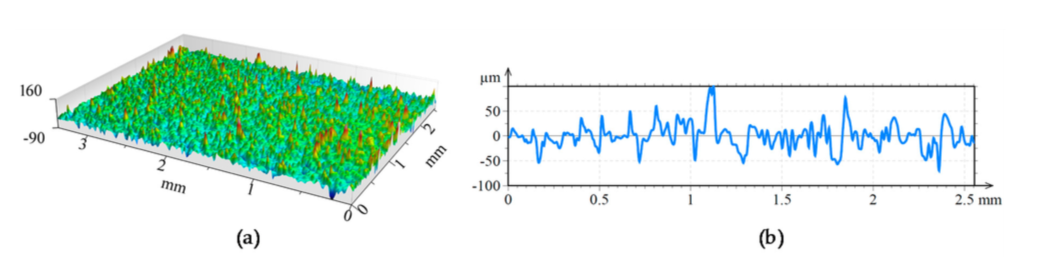
This figure displays (a) the topography and (b) surface profile of the alloy’s surface following LBM. Image courtesy of MDPI.
Laser Polishing
Laser Polishing (LP) is the final laser-based technique used to manufacture the alloy part. Although the LBM process left the part without the non-ideal wavy surface, the surface of the part is still rough. A confocal microscope measures surface roughness, which then determines parameters for the LP process. The LP process utilizes the same laser as from the LBM process. The process removes roughness and produces a polished part, that needs no further machining. However, it leaves a recast layer on the surface of the part. In the experiment, the recast layer measured 22 μm, which was determined to be not significant enough to modify mechanical properties of the part. This recast layer, and its depth, should be considered when analyzing the finalized part.
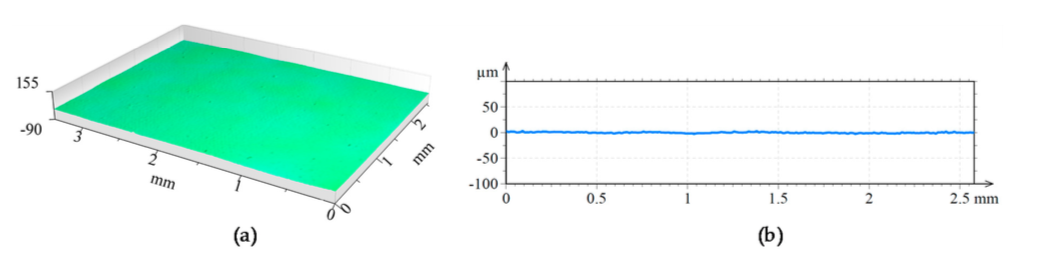
This figure displays (a) the topography and (b) surface profile of the alloy’s surface following LP. Image courtesy of MDPI.
Why use combination laser processing?
The combination of the three individual laser processes succeeded in producing a finished part with desired dimensions and surface roughness. It required no outside machining or tools besides the multiple lasers involved. Combination laser processing is also cleaner and more environmentally friendly than traditional machining and metal processing, and does minimal damage to the metal part being processed. Finally, the use of lasers is very precise. Therefore, using laser processing techniques is most effective at producing parts with high levels of details. The only downsides are that this combination technique, particularly the LBM process, are slow, and that the recast layer produced by the LP process may modify mechanical properties of the part’s surface.
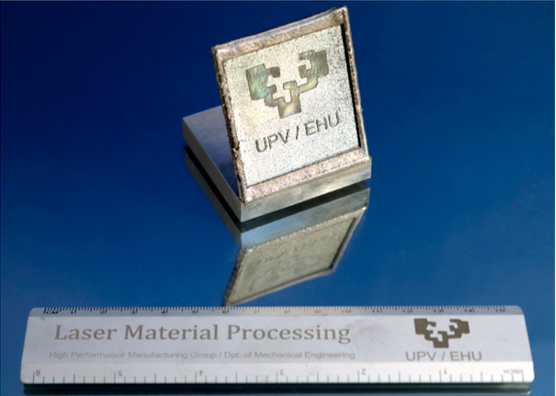
The image displays the finalized manufactured part made using the combination laser processing technique described within the paper. Image courtesy of MDPI.
Conclusion
A full laser-based manufacturing technique made up of multiple individual laser processes is a realistic option for the manufacturing of small, detailed parts. In the experiment found in the paper, the combination laser processing technique was highly successful at creating a Inconel 718 part. The technology still has room for many improvements. LBM is still not commonly used in industrial settings because it is not fully developed. In time, all aspects of this technique will become more effective. However, combination laser processing could replace traditional machining techniques, such as milling, in the near future due to its precision, low environmental footprint, and low quantity of materials wasted.
To read more about the experiment, find the paper here.