Whether you are new to laser marking or have already had significant experience in laser marking technologies, it’s a quest for continuous improvement of the quality and contrasts of laser marks. Laser marking metals is especially important as metals are ubiquitous in pretty much everything we touch in daily lives, from electronic gadgets to sophisticated medical equipment.
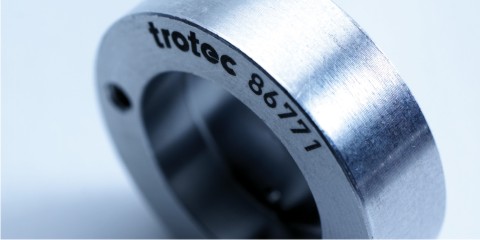
Part with a laser-marked serial number. Courtesy of How To Laser
Laser marking is a non-contact method of permanently marking metals, where depth of the cut can be controlled and even automated. Laser marking is convenient in that it is compatible with almost any vector software, like CAD or Illustrator, for the marking patterns. As with all machining techniques, there are some important factors to be considered when laser marking metals and that’s exactly what we will discuss in this blog post. Without further ado, here are 5 things to consider when laser marking metals.
1. Material Properties
With all laser marking applications, it is important to consider what material is being marked. Materials have different absorption spectra meaning they react differently to different wavelengths. This must be kept in mind when deciding what material to use with what laser source. The melting point and the material’s response to heat must also be considered. The hardness of the material should also be taken into consideration. For instance, laser marking aluminum will take less time than laser marking steel since it is a much softer metal with lower melting temperature.
2. Type of the Laser
Both CW lasers and pulsed lasers can be used when laser marking metals. However, pulsed fiber lasers are used more frequently since they can deliver a higher intensity beam without overheating the sample. Common types of lasers used for laser marking include “carbon dioxide, ytterbium-doped fiber, UV, and green and neodymium vanadate lasers” (from How to Laser).
CO2 lasers are less used for metal and more for woods, glasses, and plastics. Green lasers, again, are less used for metals and more so for plastics and glasses. Fiber lasers are typically used for marking metals, and are suitable for a wide variety of them, ranging from steel to copper. Lasers of >50W power are generally recommended for marking metals. Fiber lasers can be designed to have higher beam quality than lasers of similar average output power. This beam quality controls the beam’s spot size, and thus the width or the finesse of the laser marking.
3. The Choice of Laser Marking Method
There are multiple methods for laser marking metals that produce different kind of marks. The durability and time consideration for each method are just some of what needs to be weighed when deciding which method is most desirable for a specific application. Some of these methods are explored below:
Laser Engraving
This method sublimes the metal. The heat from the laser vaporizes the metal, causing it to go directly from its solid state to gas. Laser engraving creates very resistant markings, as they create a very deep marking in the context of laser marking methods. For laser engraving, the depth of the cut tends to range from 0.0001” to 0.005”. The permanent marks of laser engraving are very desirable in applications where part traceability is concerned.
Laser Etching
Laser etching is a very quick process that melts the metal almost instantaneously. It creates high contrast marks. Laser etching is less permanent than laser engraving, and although they are similar, etching is typically a shallower mark—less than 0.0001”—than that for engraving. Since the marks created with etching are shallower, they are also suitable for thinner sheets of metal that require less permanency of the marks.
Laser Annealing
This process makes it possible to create colored markings for specific metals, namely steel, titanium, and stainless steel. This method does not actually remove material—rather, it creates a chemical change under the material’s surface making it ideal for surfaces that cannot withstand any damage. With annealing, the metal is slowly heated by the laser beam changing the lattice structure of the metal. The metal oxidizes and once cooled, changes color. For annealed metals, when incident light hits the metal’s surface, some of the light is reflected off the oxide layer and some is absorbed. The absorbed light then is either absorbed or reflected off the oxide layer. The thicker the oxide layer, the darker the color the metal appears.
Laser Ablation
Laser ablation is a way to selectively remove material from a solid surface in a controlled fashion. This method can be used for paint removal or thin film removal, which is a much quicker and more environmentally-friendly process than that typically used for thin film removal, however it can also be used to deposit films to a surface, not just remove them.
You might also like our Technical Guide on Laser Scan Heads - an essential component in many laser marking systems.
4. Work Environment
As with any machining operation, it is vital to ensure proper airflow and ventilation/filtration systems are being used. Lasers obviously generate heat, and laser marking metals can produce vapors and particles. This makes having a safe work environment of utmost importance.
5. Cost
One of the decisions to be made is determining if it makes sense to purchase a laser marking setup or to just have the services performed by another party, and if one is a better investment than the other. This could be dependent upon the number of products that require marking and the frequency of the use of the laser marking setup. The material cost and time to complete each laser marking should also be considered.
Conclusion
These are just some of the considerations to keep in mind when laser marking metals. There are multiple articles on this blog for further perusal of the laser marking process, some of which are tagged below. At FindLight Marketplace we also have a large selection of Laser Engraving Machines and Laser Marking Machines from many different suppliers around the world. If you are looking to purchase such a system you might want to start your comparative shopping in those categories.
This Blog post was sponsored by RPMC Lasers, Inc - a leading supplier of pulsed and CW lasers, laser diodes and amplifiers.
The cost tip is really useful. Laser engraving machine gives it an advantage over other traditional techniques involving the usage of inks or tool bits.