Flaw detection and rapid fatigue fracture
Additive manufacturing (AM) techniques have gained popularity in a number of high-value industries due to their capacity to produce small batches of geometrically complicated components in an economically viable manner. The ability of laser-based powder bed fusion (L-PBF) processes to produce optimized components from engineering grade materials, such as a number of aluminum, steel, and titanium, has attracted particular interest in the power, medical, aerospace, and defense industries. However, flaw detection in this process is yet a challenge in the industry. In this article, we discuss the importance of flaw detection in L-PBF, what the challenges are in this area, and finally how we can use machine learning techniques such as convolutional neural networks to detect them.
In an area that matches a two-dimensional (2D) slice of the component’s three-dimensional (3D) shape, a laser moves over the build plate, melting the powder. After the layer is finished, the build platform is lowered, a fresh coating of powder is applied, and the subsequent layer is fused to the layers that came before. Up until the component is finished, this process is repeated.
Despite the geometric freedoms made possible by the technology, poor build quality that results in inconsistency in both static and dynamic mechanical properties has prevented broad implementation of L-PBF. A major obstacle to qualifying and expanding the use of the technique is scatter in fatigue characteristics, which has prevented the use of AM components in important applications.
Inconsistencies in the material, such as gas porosity, keyhole pores, and lack of fusion, have been frequently blamed for this scatter. Lack-of-fusion pores, like the one shown in Figure 1, are typically assumed to be small (50 m or less) and rather spherical, in contrast to gas and keyhole pores.
The existence of spatter particles interacting with the incident laser beam has been linked to the production of lack-of-fusion faults that have been found in coupons made using optimum processing parameters. These faults are substantial stress concentrators appropriate for rapid fatigue fracture formation because of their increased size and irregularity.
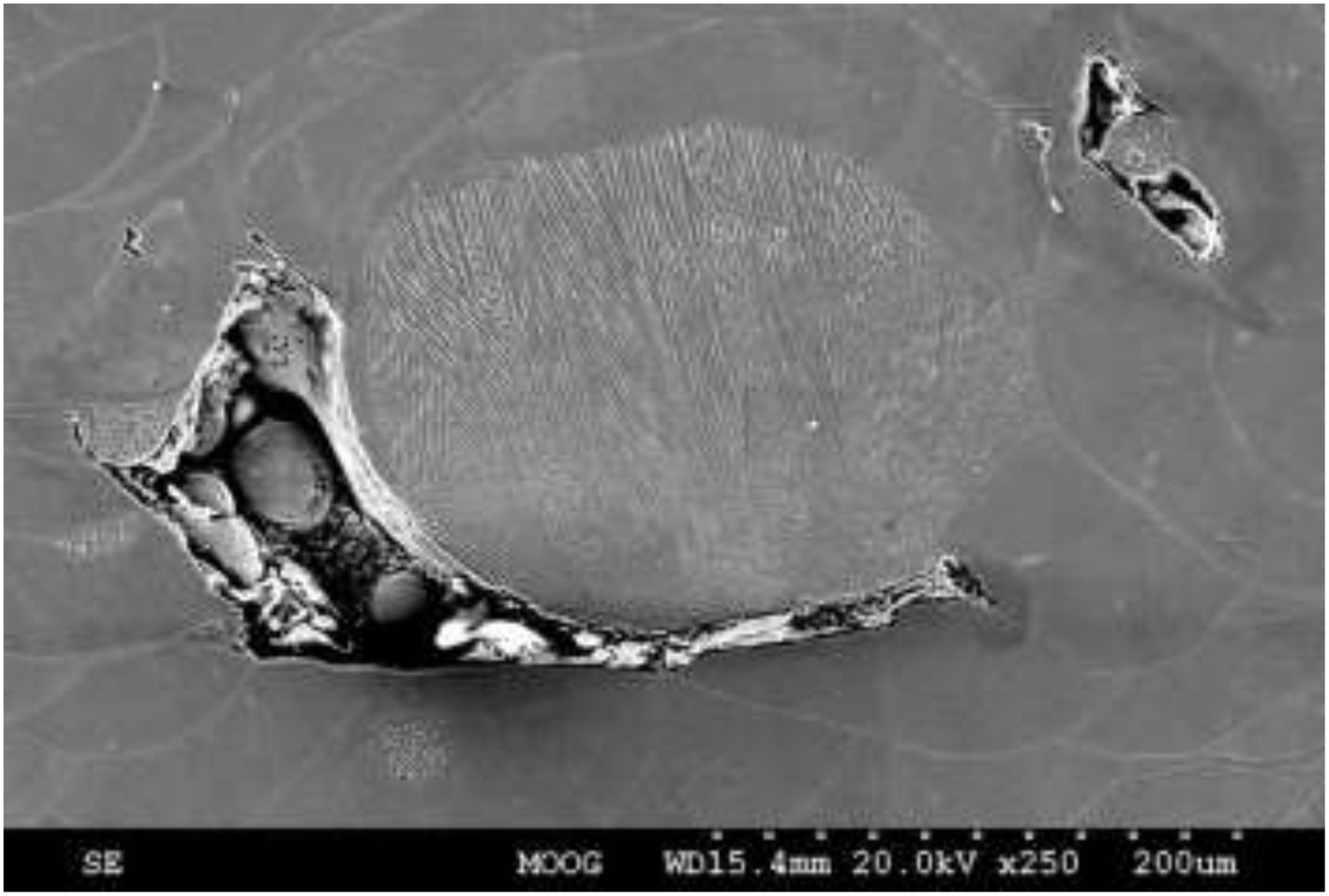
Figure 1: Example of a lack-of-fusion flaw in a L-PBF build; Image courtesy of Elsevier
X-ray computed tomography and additive manufacturing
The complex geometries and rough surfaces of as-built L-PBF components present challenges for conventional nondestructive inspection (NDI) methods for flaw detection, such as dye penetrant and ultrasonic inspection. As a result, X-ray computed tomography (XCT) has taken over as the industry standard for flaw identification in AM.
The application of XCT technology to large components made of high-density alloys for flaw detection can be constrained by considerable attenuation of the X-rays, which is unfortunate because XCT scans can quickly become cost-prohibitive in production settings. However, independent of the alloy composition or component size, it is predicted that the utilization of process monitoring data may enable faults to be automatically discovered as they arise within the components.
Photodiode arrays, acoustic monitors, high-speed video, high-resolution layer-wise imaging, and a variety of melt-pool monitoring setups are examples of process monitoring sensors that can be installed on L-PBF systems. The L-PBF process exhibits a wide range of size scales, a fast melt pool, and rapid solidification rates, which can make it difficult to detect flaws directly from in-situ monitoring data and frequently necessitate the use of multiple sensor modalities to record different physical aspects of the L-PBF process.
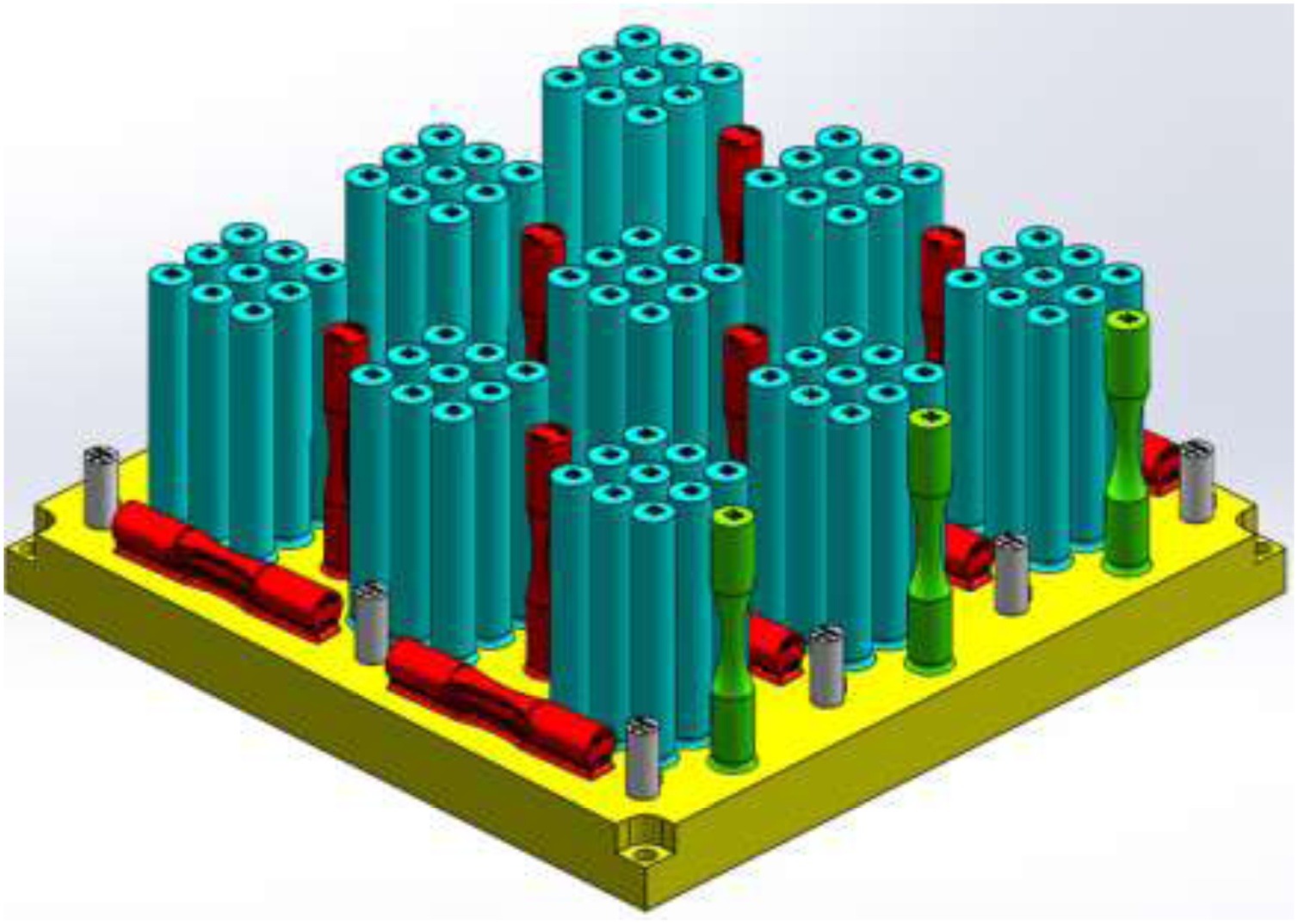
Figure 2: Configuration of the build plate used for machine learning; Image courtesy of Elsevier
The vast volume of data created makes it more difficult to discover flaws in process monitoring data. Terabytes of data can be generated from a single build, depending on the sensor configuration. As a result, machine learning techniques (see Figure 2 and Figure 4) have been used to solve this issue and have already shown to be capable of spotting macroscopic construction problems.
Machine learning applications (see Figure 2) to additive manufacturing (AM) processes have typically identified process anomalies, such as macroscopic build failures, either due to recoating issues, geometric deviations, flaws, etc., by classifying process conditions from sensor data alone or based off post-build inspection techniques, such as XCT.
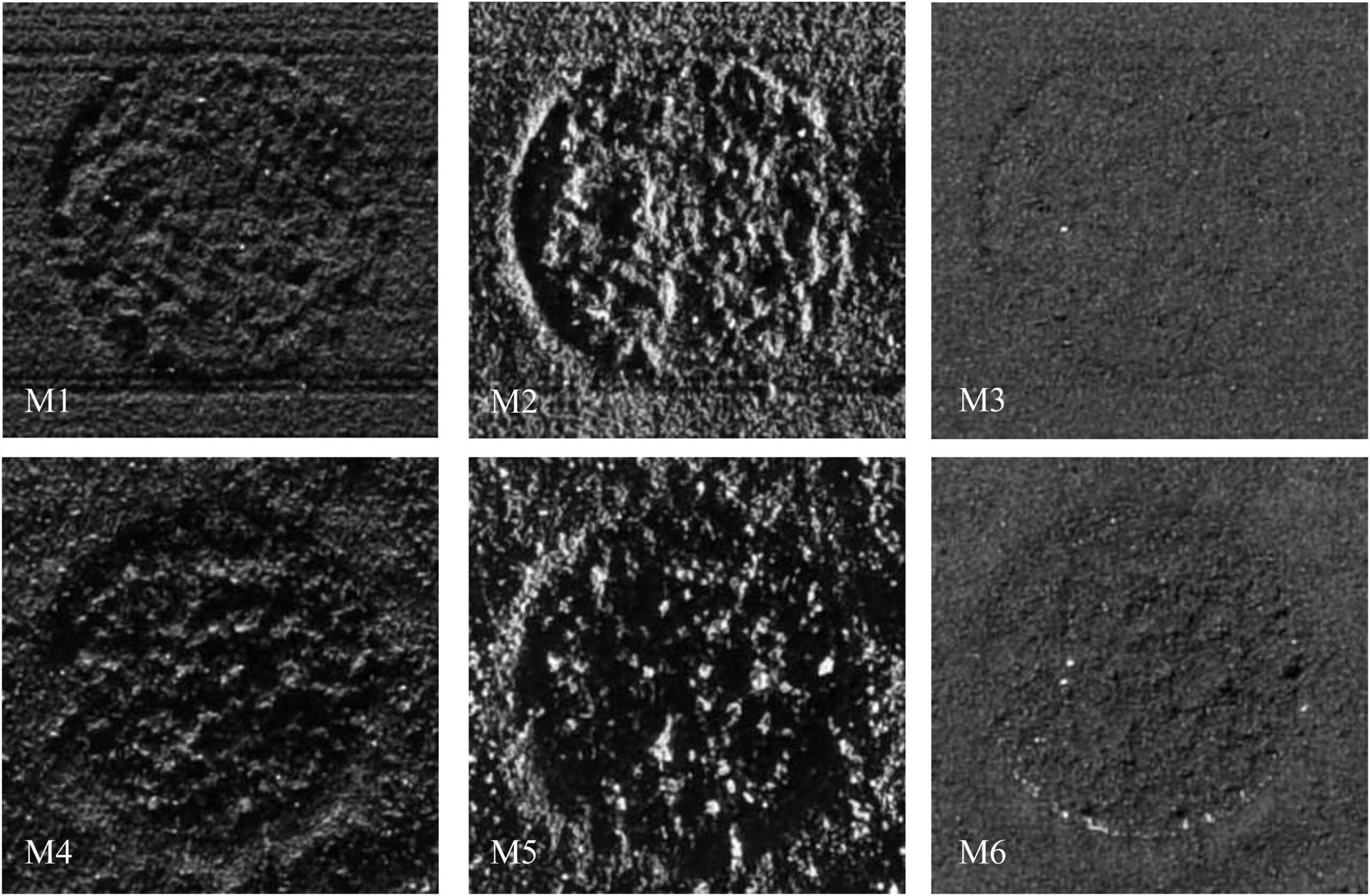
Figure 3: Representative layer-wise images taken from a sample; Image courtesy of Elsevier
Flaw detection using machine learning
While the use of post-build XCT scans offers an objective way to generate training labels that are known to correspond to faults, it is still advantageous to be able to distinguish between nominal and off-nominal processing situations from simply sensor data. High-resolution layer-wise pictures of L-PBF components created with optimum processing parameters might be used to immediately detect faults found using XCT. The layer-wise imagery (see Figure 3 and Figure 5) acquired from a single component was converted into 3D picture tiles representing nominal and anomalous voxels (see Figure 4) using registered XCT and layer-wise imagery.
Prior investigations into L-PBF process monitoring data using machine learning techniques have either been limited to a single component or to components made from only a single build. The trained classifiers (as a machine learning component) would learn sensor signals indicative of flaws intrinsic to the L-PBF process itself. This would show that the trained classifiers are not over-fitting to data collected from a single build or component. With varied degrees of success, many ML approaches may also generalize to data gathered from independent builds.
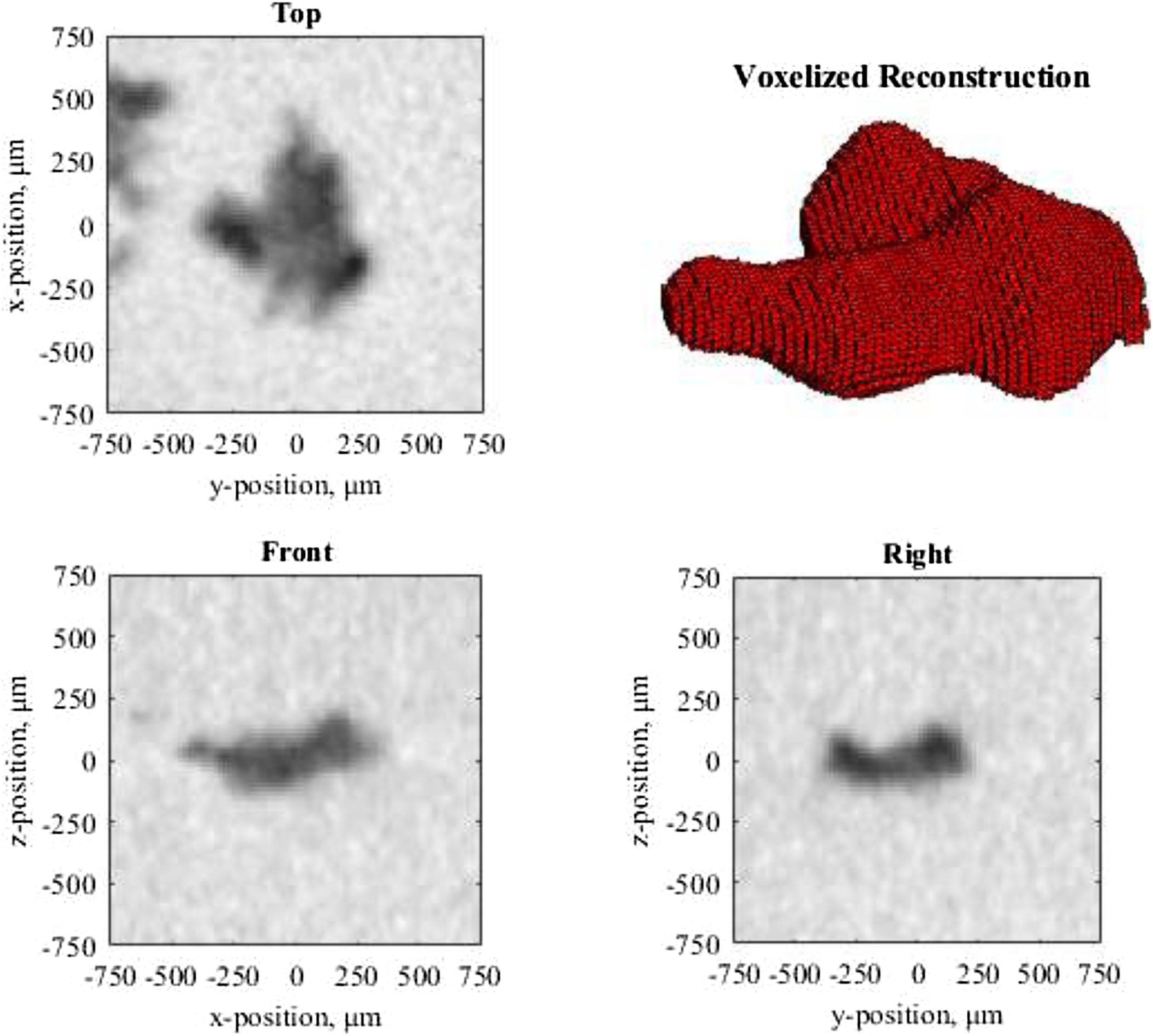
Figure 4: A lack-of-fusion flaw detected in the data used for machine learning algorithm; Image courtesy of Elsevier
Using convolutional neural networks to overcome the challenges
In the rest of this article, we discuss some novel works by the researchers at the Penn State University to resolve the challenges we listed in the previous sections. They demonstrated that L-PBF flaws can be directly detected by applying machine learning techniques to process monitoring data in the form of high-resolution layer-wise images. They explored the variables influencing the generalizability of neural networks (NNs) and convolutional neural networks (CNNs) trained on data from one L-PBF component and tested on data collected from an independent component, and provided phenomenological explanations of the classifiability of their results. They trained both neural networks and convolutional neural networks using layer-wise images labeled from XCT data, and they assessed the generalizability of both network architectures.
The final CNN classifier had a testing accuracy of 92.2% when trained and tested on data from a single component, however it was unable to classify defects from components on a similar but independent component built on the same L-PBF platform.
However, using data from 20 parts for training and testing the classifier enhanced its generalizability, which shows the capacity to apply to many components made on different builds, with no loss of accuracy.
Furthermore, they provided evidence that the production of lack-of-fusion faults in L-PBF components, which have been recognized by the final classifier, is related to the big spatter particles expelled from the melt pool (see Figure 5).
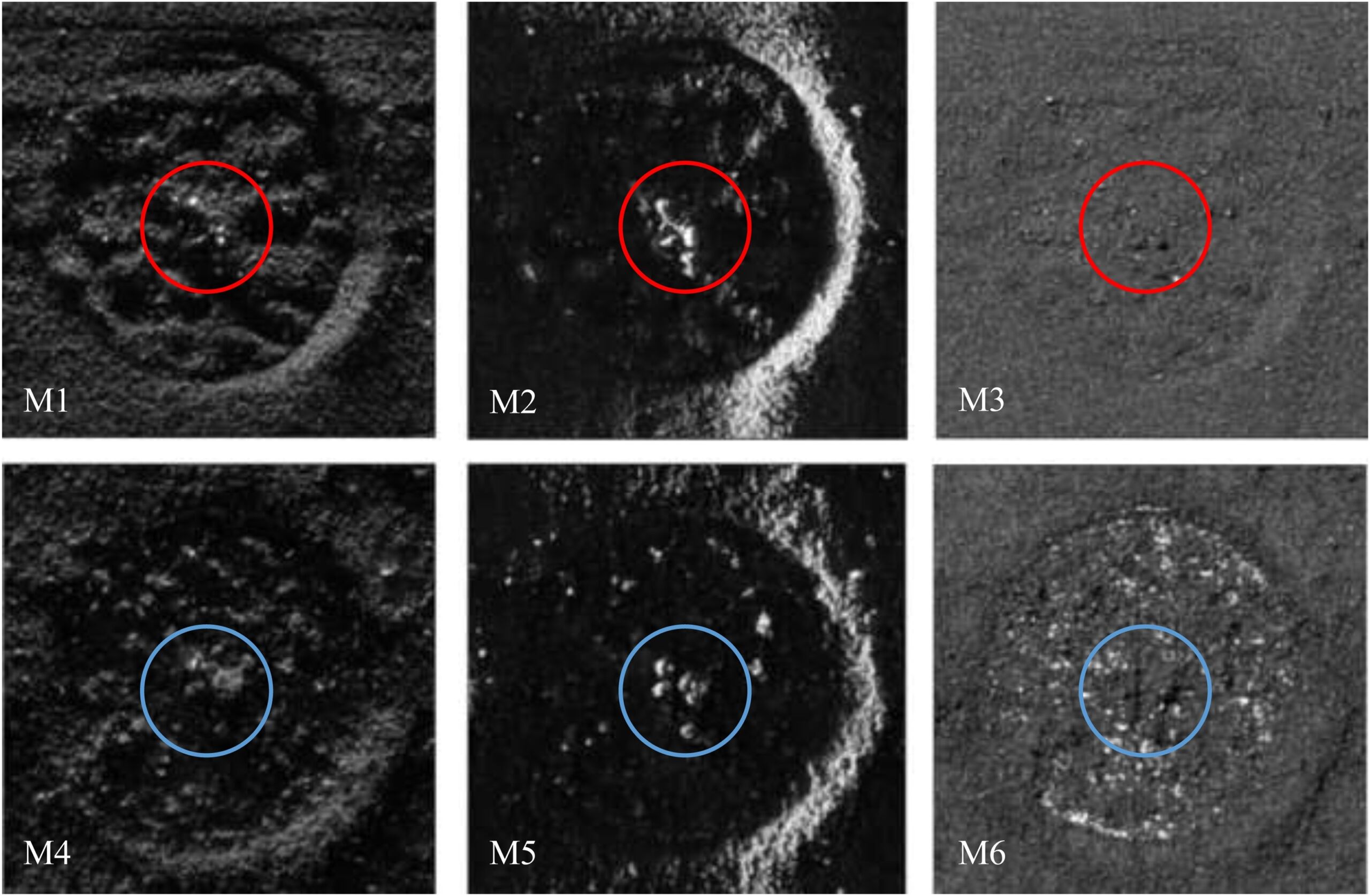
Figure 5: Comparison of all image modalities for different layers; Image courtesy of Elsevier
This article is brought to you by Connet Laser Technology, a leading manufacturer of fiber lasers and amplifiers.