Introduction
Goniometer stages, as shown in the example below, are precision instruments that play a pivotal role in the realm of optics. Their primary function is to measure angles or rotate an object around a fixed point, either in the horizontal or vertical plane, thereby facilitating precise angular positioning and alignment.
These specialized devices empower researchers and scientists to manipulate and measure angular positions with extraordinary precision. Consequently, they are indispensable tools in an array of optical applications, including but not limited to crystallography, spectroscopy, and material characterization.

An example of High Precision Manual Goniometer Stage, as seen on FindLight.
At their core, goniometer stages provide controlled rotational or tilting motions around one or more axes. They furnish a stable platform for positioning and aligning optical components with unparalleled accuracy and repeatability. This level of precision is vital for executing intricate experiments, calibrating instruments, or analyzing materials with complex crystal structures.
The value of these devices stems from their ability to introduce an unprecedented level of precision to angular measurement and manipulation. They facilitate control over the orientation of light beams, enable accurate angle measurements, and ensure the acquisition of reliable data. Consequently, goniometer stages contribute significantly to advancements in optics and a wide array of scientific investigations.
With their extraordinary precision measurement capabilities, goniometer stages can achieve sub-microradian or even sub-nano radian angular resolutions. This degree of accuracy enables researchers to conduct intricate experiments, corroborate theoretical predictions, and perform sensitive measurements in a myriad of scientific and industrial environments.
In this comprehensive guide, we delve into the principles of operation, design considerations, applications, calibration methods, and technological advancements of goniometer stages. By shedding light on the intricacies of these precision instruments, we aim to provide readers with a thorough understanding of their critical role in optics and precision measurement.
Principles and Operation
Goniometer stages fundamentally consist of precision stages, which furnish a stable and adjustable platform for angular motion. Outfitted with superior-quality bearings or linear guides, these stages facilitate rotational or tilting motions around one or more axes. This permits precise control over the angular position of any attached optical components or samples.
These devices meld precision stages, motion control mechanisms, and angular measurement techniques to accomplish precise angular positioning and alignment. Offering a stable platform for angular motion, the stages enable meticulous control over the position of optical components or samples. Motion control mechanisms, encompassing both manual adjustments and motorized actuators, facilitate the desired angular movements.
To attain precise angular measurements, techniques involving encoders or autocollimators are typically preferred. Encoders, which are electromechanical devices, convert angular positions into analog or digital output signals. They encode position information on a disc or strip, thus enabling accurate measurement of angular displacement or rotation. Autocollimators, on the other hand, leverage optical principles to measure minor angular deviations by analyzing the angle of the reflected beam from a mirror affixed to the goniometer stage.
Goniometer stages are often equipped with specialized features to enhance their functionality. Locking mechanisms ensure the stage remains in the desired position, while fine adjustment knobs permit precise alignment. Additionally, tilt correction mechanisms are used to compensate for angular errors, ensuring the accuracy of positioning. Certain stages may also offer vacuum compatibility or employ specialized materials to minimize the effects of thermal expansion.
Design and Construction
Goniometer stages are precision instruments built for stability, accuracy, and versatility. High-quality materials such as aluminum, stainless steel, or advanced composites are used to minimize vibrations and enhance measurement precision.
Mechanical configurations depend on application requirements. Single-axis stages allow rotation around a fixed point, while multi-axis stages control multiple axes simultaneously. These configurations include rotation stages, tilt stages, and goniometer cradles.
Design considerations focus on load capacity, backlash compensation, thermal stability, and precision motion control. Load capacity refers to the maximum weight the stage can handle, and backlash compensation mechanisms reduce play in mechanical components for precise positioning. Thermal stability is maintained through temperature compensation features or materials with low thermal expansion coefficients.
Precision motion control mechanisms like micrometer heads or motorized actuators enable fine adjustments and accurate positioning. Manual mechanisms offer fine control, while motorized actuators provide automated motion for better repeatability and integration with computerized systems.
Goniometer stages may also include features like locking mechanisms, index marks, or integrated sensors for real-time position feedback. These stages are designed to balance stability, precision, and versatility, making them ideal for various optical applications.
Types of Goniometer Stages
Goniometer stages come in various types, each designed to cater to specific angular manipulation and measurement requirements. These stages can be categorized into single-axis stages, multi-axis stages, rotation stages, tilt stages, and specialized goniometer stages for specific applications, a few of which are pictured below.
Single-axis stages allow rotational movement around a single axis, providing precise control over one angular degree of freedom. They are commonly used for basic angular adjustments and alignments in optical setups.
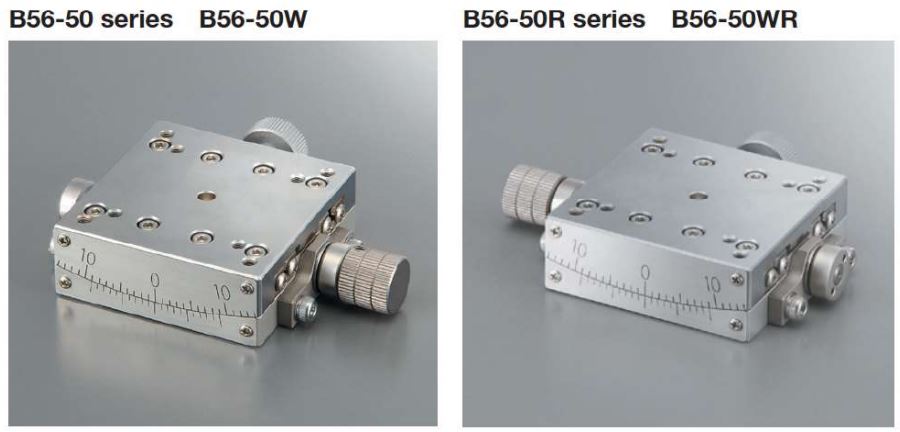
Examples of Goniometer Stages. As seen on FindLight Marketplace.
Multi-axis stages offer simultaneous control over multiple axes, enabling complex angular positioning and alignment. These stages provide enhanced flexibility for intricate optical configurations and advanced experimental setups.
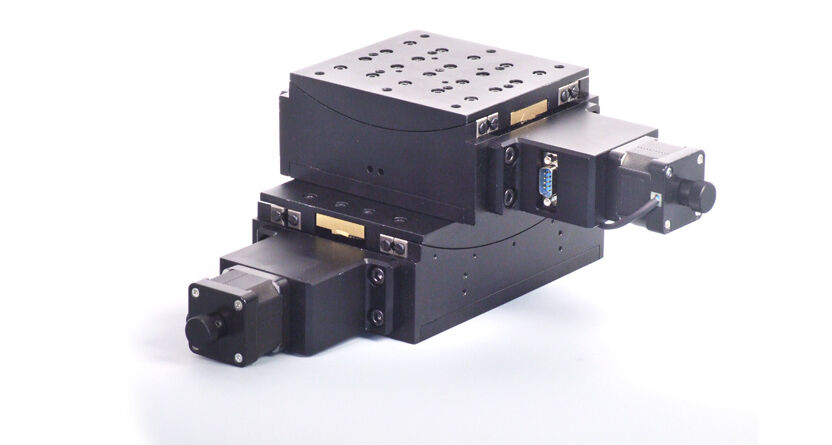
A typical Multi-Axis Goniometer Stage. Courtesy of Zolix Instruments
Tilt stages allow controlled angular tilting in a single plane. They are ideal for applications that require precise inclination adjustments, such as aligning optical elements or compensating for angular deviations.
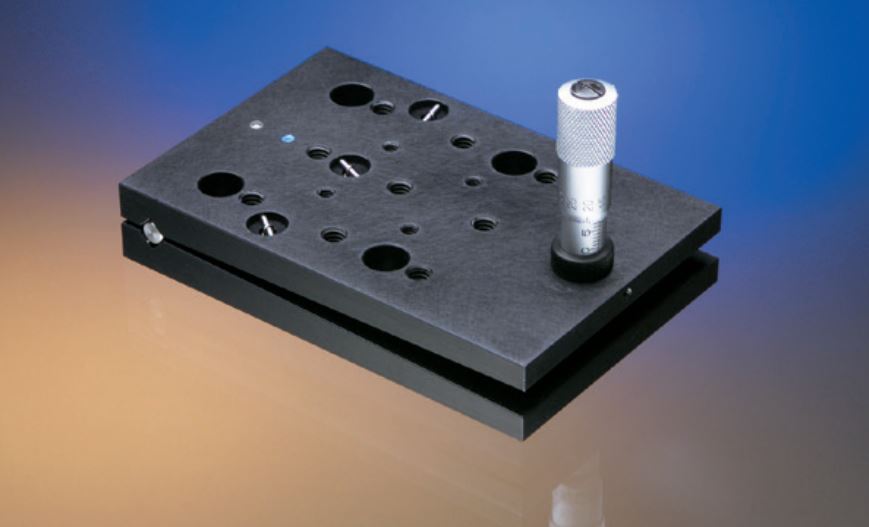
A typical 1-Axis Tilt Stage. As seen on FindLight Marketplace
Specialized goniometer stages are designed for specific applications or measurement requirements. These stages may include specialized features such as high-load capacity, vacuum compatibility, or ultra-high-precision mechanisms tailored to meet specific experimental or industrial needs.
By offering a range of types, goniometer stages accommodate diverse angular manipulation and measurement tasks in the field of optics. Researchers and engineers can choose the appropriate type based on the specific requirements of their experiments or applications, ensuring optimal performance and accurate angular control.
Applications
Goniometer stages find widespread applications in various fields and industries where precise angular manipulation and measurement are critical. Their versatility and accuracy make them indispensable tools in disciplines such as crystallography, spectroscopy, material science, and more.
In Crystallography, goniometer stages play a pivotal role in determining the structure of crystalline materials. By accurately measuring the angles between crystal faces, they enable researchers to analyze crystal structures, understand molecular arrangements, and investigate properties like lattice constants and interatomic distances. These stages are vital in X-ray crystallography experiments, where precise angular control is essential for obtaining high-resolution diffraction patterns like the one below.
In Spectroscopy, they are utilized for aligning and positioning optical components within spectrometers. They enable researchers to achieve precise angular adjustments for optimizing light paths, coupling efficiency, and minimizing stray light. Goniometer stages are particularly valuable in applications such as Raman spectroscopy, fluorescence spectroscopy, and Fourier-transform infrared spectroscopy, where accurate measurement of light intensity, wavelength, and polarization is crucial.
Material science and characterization heavily rely on goniometer stages for studying the properties of materials with complex crystal structures. They frequently aid in investigating phenomena like birefringence, optical anisotropy, and polarization effects. Furthermore, they enable researchers to precisely control the orientation of materials under investigation and study their response to different angles of incidence or polarization states of light.
Additional Fields
Furthermore, goniometer stages find applications in fields such as microscopy, metrology, optics research, and the semiconductor industry. In microscopy, the devices allow for precise sample positioning and imaging from different angles, facilitating three-dimensional reconstructions and detailed analysis. These stages are also used in metrology for calibration and alignment of precision instruments, ensuring accurate measurements. In the semiconductor industry, goniometer stages are utilized for wafer inspection, alignment of optical components, and testing the performance of semiconductor devices.
The versatility and precision measurement capabilities of goniometer stages make them indispensable in a wide range of scientific and industrial applications. Their contribution to fields such as crystallography, spectroscopy, material science, microscopy, and the semiconductor industry has revolutionized research and enabled advancements in various technological domains.
Calibration and Accuracy
The accuracy of goniometer stages hinges on careful calibration, typically involving precision reference standards such as angle interferometers or laser autocollimators to confirm stage performance.
Measurement accuracy is influenced by factors like resolution, repeatability, error sources, and environmental conditions. Higher resolution enables more delicate control and repeatability guarantees consistent positioning. However, mechanical flaws, backlash, non-linearity, and thermal effects can introduce errors impacting accuracy.
Environmental factors, such as temperature fluctuations and vibrations, can also interfere with measurements. To mitigate these effects, goniometer stages often feature temperature compensation and operate in controlled environments.
Routine calibration and verification are key to maintaining accuracy. The frequency of these checks varies based on the application and the stability of the stage.
Through rigorous calibration processes, consideration of error sources, and careful environmental management, goniometer stages deliver highly accurate and dependable angular measurements in both scientific and industrial contexts.
Integration/Automation
Goniometer stages are seamlessly integrated into control systems, software interfaces, and computer-aided measurement setups, enhancing automation and providing precise control of angular positioning.
Compatibility with control systems is a key aspect of integrating goniometer stages into larger experimental setups. These stages are oftentimes interfaced with various control mechanisms, such as manual control units, motorized controllers, or programmable logic controllers (PLCs). Motorized goniometer stages often feature standard communication protocols, such as RS-232 or USB, enabling easy integration with external control systems.
Software interfaces play a vital role in automating the operation of goniometer stages. They provide intuitive graphical user interfaces (GUIs) or application programming interfaces (APIs) that allow users to control the stage, set specific angular positions, and automate complex motion sequences. These software interfaces may also enable data logging, real-time feedback, and synchronization with other instruments or data acquisition systems.
Goniometer stages are often compatible with computer-aided measurement setups, where they are incorporated into automated measurement routines. These setups utilize software tools for experiment control, data acquisition, and analysis. They can be programmed to perform precise angular movements as part of larger measurement sequences, enabling efficient and accurate data collection.
The integration and automation of goniometer stages provide numerous benefits, including improved repeatability, reduced human error, and increased experimental efficiency. Researchers can achieve complex motion sequences, perform synchronized measurements, and automate data acquisition and analysis, streamlining the experimental workflow and enhancing overall productivity.
Advancements and Innovation
Goniometer stages have undergone significant advancements in recent years, introducing new technologies, materials, and design approaches to improve their performance and accuracy. High-resolution encoders and advanced feedback systems have enhanced measurement accuracy, providing finer angular resolutions. Stiff materials, including carbon fiber composites and high-grade alloys, have increased rigidity and stability during angular manipulation. Innovative mechanical designs and motion control mechanisms minimize hysteresis and backlash, reducing mechanical errors.
Intelligent control systems and software algorithms enable real-time error compensation and automatic calibration, further enhancing measurement accuracy and stability. The trend towards miniaturization has resulted in compact goniometer stages. These smaller devices allow for efficient use of laboratory space and integration into space-constrained setups. These advancements and innovations continually push the boundaries of precision angular manipulation and measurement, providing researchers in various scientific fields with increasingly accurate and reliable tools for their experiments and applications.
Limitations and Challenges
While goniometer stages offer precise angular manipulation and measurement capabilities, they are not without limitations and challenges. Several factors can impact their performance and usage, including mechanical stability, thermal effects, measurement uncertainties, and practical constraints.
One significant limitation is mechanical stability. Goniometer stages may be subject to mechanical vibrations or drift over time, which can introduce errors in angular positioning. Ensuring adequate mechanical stability through robust design, high-quality components, and proper installation is crucial to mitigate these effects.
Thermal effects also pose a challenge. Temperature variations can cause expansion or contraction of materials, leading to changes in stage dimensions and introducing angular errors. Thermal management strategies, such as temperature stabilization or compensation techniques, help minimize these effects and maintain measurement accuracy.
Measurement uncertainties are inherent in any measurement system, including goniometer stages. Factors like resolution limits, repeatability variations, and calibration uncertainties contribute to measurement errors. Regular calibration, error compensation algorithms, and proper consideration of measurement uncertainties can help improve the overall accuracy of goniometer stages.
Practical constraints can also impact the usage of goniometer stages. Size limitations may restrict the range of motion or limit the integration possibilities in certain experimental setups. Compatibility with control systems, software interfaces, or measurement instruments can also pose challenges, requiring careful consideration and compatibility testing.
Combating the Limitations
Despite these challenges, goniometer stages offer notable advantages that combat these limitations. Their precision positioning and measurement capabilities make them invaluable tools in various fields.
Moreover, the compatibility of goniometer stages with control systems and software interfaces allows for automation, precise motion sequencing, and integration into larger experimental setups. Additionally, regular calibration and error compensation techniques can mitigate the limitations associated with mechanical stability and measurement uncertainties.
Despite the limitations and challenges, goniometer stages remain indispensable tools in scientific research, providing precise angular manipulation and measurement capabilities that drive advancements in various disciplines. Continuous improvements in design, materials, and calibration techniques further enhance their performance and expand their applications in diverse fields.
Related Instruments and Techniques
Several instruments share similar functionalities with goniometer stages or are often used in conjunction with them:
- Angle Interferometers: These devices are typically used to measure small angular displacements with high precision. They often serve as a calibration reference for goniometer stages.
- Laser Autocollimators: These instruments measure angular deviations by analyzing the angle of a reflected laser beam. Like angle interferometers, they are also commonly used to calibrate goniometer stages.
- Rotary Tables: Rotary tables provide rotation around a single axis, similar to a single-axis goniometer stage. However, they are typically larger and used for heavier loads.
- Polarimeters: While not providing rotation, polarimeters are optical instruments often used in conjunction with goniometer stages in polarization studies.
- Optical Mounts: These devices hold optical components in place and often have adjustable angles. While not as precise as goniometer stages, they provide a more straightforward and cost-effective solution for simpler applications.
Each of these instruments has its own strengths and is suited to particular applications. However, for applications requiring high precision angular positioning and manipulation, goniometer stages remain the tool of choice due to their versatility, precision, and ability to integrate with automated systems.
Conclusion
In conclusion, goniometer stages are indispensable tools in the field of angular positioning and measurement. They provide researchers with the ability to precisely manipulate and measure angles, facilitating the study of crystallography, material characterization, optical alignment, and various other applications. Goniometer stages offer a versatile and adjustable platform for achieving complex angular positions with high accuracy. Their compatibility with automation and integration into larger experimental setups enables seamless control and data acquisition.
Compared to alternative instruments and techniques, goniometer stages provide direct, hands-on control over angular positioning, making them superior tools for achieving precise and customizable angular measurements and manipulations. With continuous advancements in design, materials, and calibration techniques, goniometer stages continue to push the boundaries of precision angular manipulation, contributing to advancements in scientific research and various industries.
Interested in purchasing a Goniometer Stage? You can start your comparison shopping here at FindLight.