In this blog post we will provide a brief introductory guide to laser welding. If you ever wondered what welding is, how lasers fuse materials, what industries use laser welding and more, this introductory guide can be a handy resource. In this article we will cover the following topics and you can click on the links below to navigate to the appropriate section quickly:
- What is Welding
- Industries that Use Laser Welding
- Types of Laser Welding: Direct and Transmission Welding
- Types of Laser Beams
- Industrial Applications
What is Welding
Welding is a process that fuses two materials together by heat and/or pressure. Metals and plastics are the most common materials that lend themselves to welding applications. Surprisingly wood can be welded too although the actual mechanism of bonding wood is less understood. The ancient Egyptians employed the heating process to bond copper. This was perhaps the first version of welding known to mankind. In more modern history, traditional welding first occurred in 1881, when Auguste de Méritens used electric arc heat to weld lead plates together. This led to rapid use of this application in the manufacturing of storage for batteries. Laser welding, a relatively newer invention, utilizes a laser as the heat source to weld materials together.
The laser heats the two areas of the pieces, and fusing them together in the cooling process. Lasers are particularly advantageous to use due to the highly concentrated heat source and ability to control the beam size. This leads to smooth and strong joints, suitable for various applications.
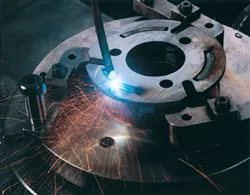
A laser welding of a piece of metal. Photo courtesy of The Fabricator.
Industries that Use Laser Welding
Many industries require laser welding for quality and efficiency. This includes automation, biomedical device industry, food packaging and even medicine. Laser welding especially caters to industrial automation due to its speed and productivity. An alternative to laser welding is arc welding, which uses an “arc” of electricity as the heat source. Arc welding can reach speeds of up to 80 inches per minute for sheet metal.
On the other hand, laser welding can reach speeds of up to 400 inches per minute for sheet metal and due to the high heat and deep penetration abilities, often only requires one pass through, making it even faster than arc welding. Highly valued in the medical industry, laser welding can also create very neat joints with high tolerances. This is due to the small beam size and the ability to focus tightly on the welded area, without perturbing the material around it.
Types of Laser Welding
As we know, the laser energy can be reflected, transmitted, or absorbed. Direct laser welding occurs when the laser energy is not transmitted through the material. This can be for any reason such as the energy level of the laser beam or absorption properties of the welded materials. For example, if the material has a lower melting point, the laser will melt the outer layer and not penetrate further down to the inner layers. Typically a carbon dioxide (CO2) laser is the suitable choice for direct laser welding. This laser has a wavelength of 10.6 micrometers, making it also useful for cutting thin plastics. The upper layer of the plastic, which is less than half a millimeter thick, absorbs the heat quickly and therefore leads to fast welding. Speeds of up to 1000 meters per minute are easily achievable in direct laser welding using CO2 lasers.
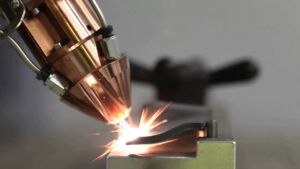
Direct Laser Welding. Courtesy of TRUMPF
Transmission laser welding is more common than direct laser welding and has been around longer. In contrast to direct laser welding, during transmission laser welding, the laser beam penetrates through the upper material heating the inner layers. A typical example of transmission laser welding is bonding two plastic materials: an upper layer that transmits IR (infrared) radiation and a black, carbon layer on the bottom, that absorbs the transmitted laser energy. The laser can then heat the boundary between these materials and weld them. The image below illustrates how this process works. A laser beam is directed to the top layer, and the energy is transmitted through the layer to the bottom layer. The bottom layer absorbs the energy, allowing for localized heating. Both sides are under applied pressure that ensures a tight, uniform weld.
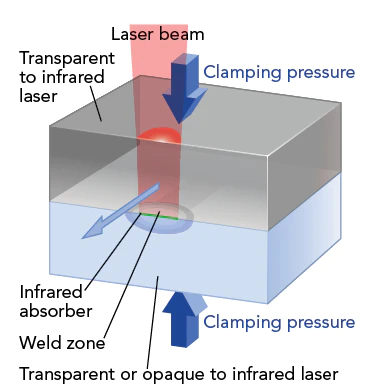
An illustrative representation of the transmission laser welding process.
Types of Laser Beams
While transmission and direct laser welding call for different beam characteristics there is a variety of choices when it comes to the proper source. Each of those choices come with their pros and cons. A fiber laser for instance has a doped fiber in its inner core and offers a compact packaging and reliable performance. With special doping elements such as erbium, ytterbium, or holmium they can operate with lower pump energies and high efficiency while attaining a high output power at relatively low cost. With a decent output beam quality they are an ideal choice for all types of industries, especially medical, automotive, and aerospace.
Nd: YAG Pulsed Lasers are another popular choice for welding applications. Nd: YAG is a crystal and works as the medium for the laser, similar to the fiber medium in a fiber laser. These lasers are unique since they emit discrete pulses of energy, not a continuous stream. These energy bursts can be shaped, allowing for optimized welding operation such as lower collateral heating and material perturbation. Nd: YAG lasers are useful for deep spot and seam welding applications. Spot welds are type of joints that combine two metal pieces together and are commonly used in the automotive industry.
The last of the three popular lasers used for such applications is a continuous wave laser. As the name suggests, continuous wave lasers emit a continuous beam, unlike Pulsed lasers which emit short bursts of lights (pulses). Many gas lasers such as CO2 and Excimer lasers are often used for such material processing purposes. High-speed and deep penetration welding primarily require CW lasers.
Industrial Applications
Welding together different materials is common for industries such as automotive and aviation. However, welding different materials require knowledge of the melting point, strength, and other material properties. Without this knowledge, the weld will not be as strong or heat resistant. Welding together different metals are crucial for the automotive and aviation industry. Creating light-weight accurate joints is the hallmark of modern manufacturing in automotive and aeronautical industries. With ever increasing benchmarks for efficiency and tight regulations this becomes increasingly more important.
Recent innovations both in laser industry and metallurgy offer new avenues for controlling the parameters of the end-product. The wide availability of alloys such as aluminum-zinc and the ability of laser technology to process these materials makes it possible to create stronger and lighter chassis for automotive and air vessels.
This post is sponsored by RPMC Lasers - a trusted provider of laser equipment throughout the Unites States.