Handheld Laser Welders are extremely adaptable machines used to conjoin pieces of metal. In this blog post, we will discuss the technology, purpose, and benefits of these advanced machines.
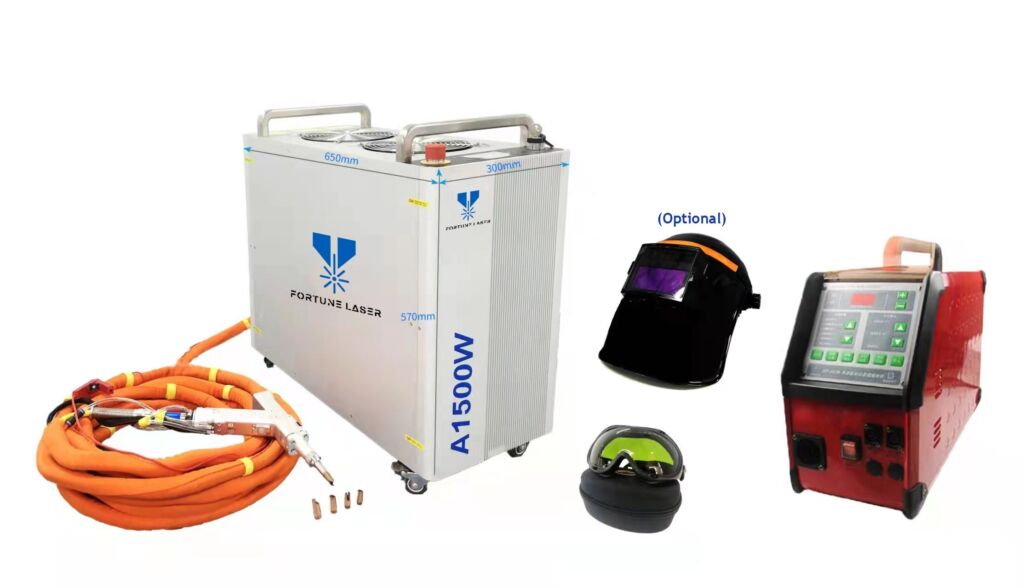
A typical handheld laser welding machine. Image courtesy of Fortune Laser
Laser Welding is a progressive technique utilized to weld metals or thermoplastic materials using a laser beam. The laser beam serves as a concentrated heat source, allowing for extreme precision and quick execution rates. The laser source creates a stronger seam at an extremely high speed, making the machines convenient for mechanical industries requiring higher precision in the production process.
Handheld Laser Welding Machines optimize mobility during this process and provide further flexibility for the user. Although human usage typically results in less precision, the accuracy of the welding process in these machines outweighs any drawbacks resulting in high-quality welds. These machines are exceptionally user-friendly, oftentimes constructed as an all-in-one machine much like the one shown above.
Handheld Laser Welders
The technology of Handheld Laser Machines is similar to that of automated ones, with a few user-friendly aspects added for increased flexibility and mobility. The main difference lies in how the laser power is transmitted to a handheld device for human operation. Despite the difference, they maintain standard laser welder characteristics of creating strong, precise joints on a variety of compatible materials.
Key System Features of a Handheld Laser Welder
In the handheld laser system, the features are generally organized as shown in the photo below. The laser engine is placed in a different unit, while the resulting radiation is channeled to a handheld welding gun through an optical fiber. This welding gun is typically equipped with focus-finding capabilities, allowing for swift positioning of the apparatus in the desired weld area.
During the welding process, the laser heats/melts the surrounding materials and subsequently fuses them together during the cooling process.
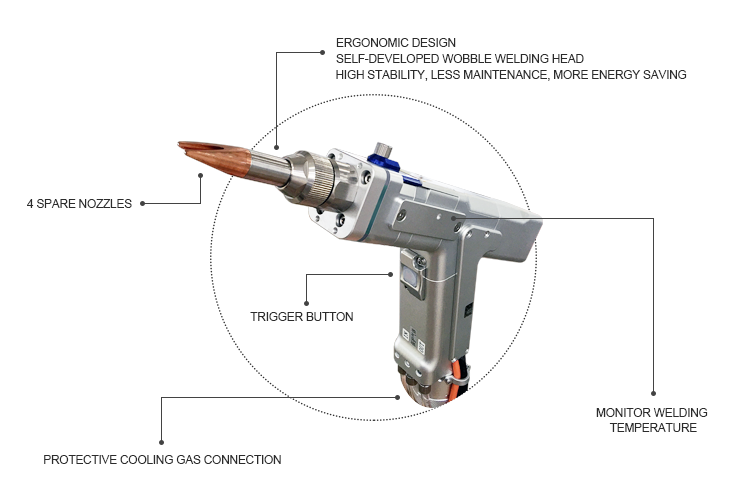
Handheld Laser Welding Gun: Diagram of the key components shows the output port nozzle, trigger button and the outlet for connecting a special cooling gas stream to help cool down the welded pieces.
As shown in the photo, the welding gun is equipped with a spray head, a trigger button, and a temperature monitor. All of these amount to an extremely efficient or ergonomic design resulting in little maintenance and high stability. The meticulous control this device offers over the depth and width of the weld makes it a popular choice for industries requiring precise and smooth execution.
The separate unit of the Handheld Laser Welder is where the radiation and energy are generated. This component contains a user-friendly operation panel for easy use of the machine’s settings. It will typically resemble the machine in the diagram shown below.
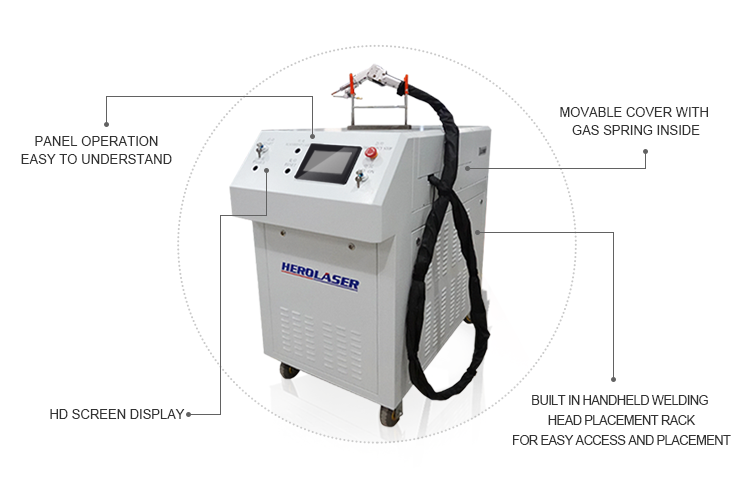
Handheld Laser Welding Unit: The diagram of key components highlights the main operation unit that houses the laser head, and the operation display unit that controls all the key parameters of the laser.
By the way, if your laser welder’s output ever deteriorates, consider investing in a good power detector from our sponsor – Gentec EO. They are a world leading expert in laser beam measurement solutions.
Advantages and Disadvantages of Handheld Laser Welders
The benefits of these machines severely outweigh the disadvantages, but here we will discuss them both in a brief comparison.
Limitations
The main drawback of Handheld Laser Welders is oftentimes acknowledged as the hefty price tag that comes with them. They range from estimated values of $8,000 for handheld types to around $50,000 for automatic machines. For businesses of smaller scales working on more personal projects, these costs may be a bit out of reach. However, the benefits and overall cost efficiency of these machines can often easily balance their price with time.
Benefits
Prior to laser welding machines, Soldering, arc welding and flame welding were the standard methods of choice for welding projects. Soldering is a procedure used to join two or more items using a filler metal. Common filler metals typically include tin, lead, silver, aluminum, nickel, or copper. The filler metal is poured into the desired area of the connecting joint and then melted to create the weld. The photo below compares a standard soldered weld and a laser weld.
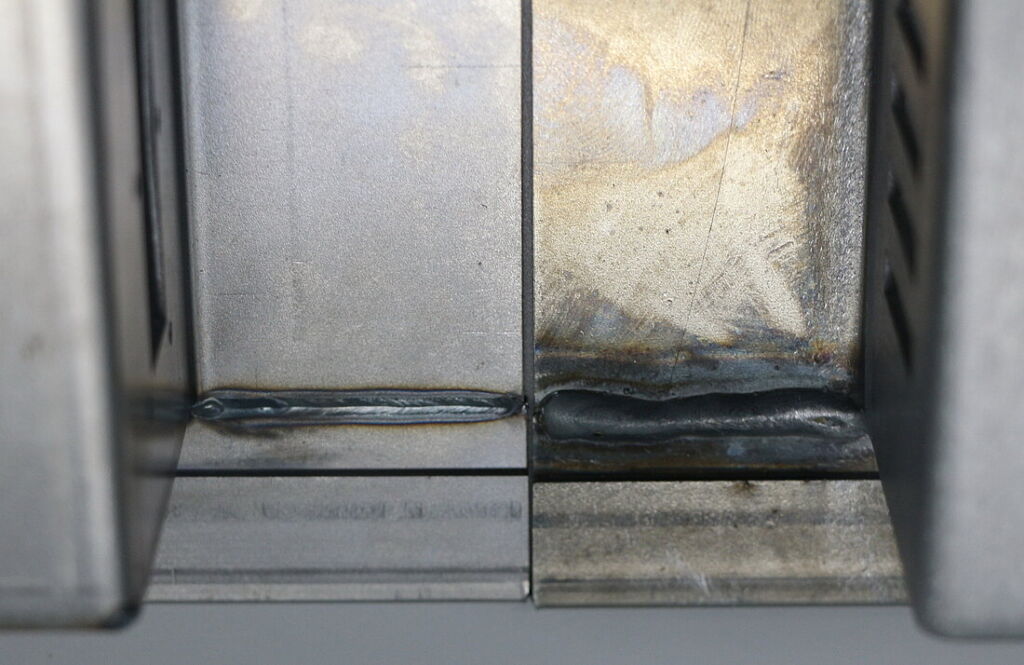
A side-by-side comparison of a soldered weld joint (right), and a handheld laser welded joint (left).
As you can see from the photo above, it is quite clear that handheld laser welders offer further precision and cleaner execution in comparison to soldering methods. The weld itself is much smaller in surface area and there is less residue surrounding the joint. This ultimately provides a more polished appearance for welded pieces.
Not only are Handheld Laser Welders more accurate, but they are also much faster. Depending on the type of laser and the amount of power used, the machines can weld materials at high speeds of numerous meters per minute. This makes laser welding machines extremely suitable for high-productivity environments.
Another notable benefit is their wide range of material compatibility, as discussed earlier. When it comes to different types of steel, the machines are capable of welding different thicknesses of the material. An alternate thickness was once tricky to account for using soldering methods, so this has saved a good deal of time for manufacturing industries.
Overall, handheld systems offer flexibility not seen in other machines, which provides mobility to execute unique welds of various sizes and thicknesses.
Summary
When analyzing the technology and benefits of Laser Welding as a whole, it is evident to the average person that the machines are cleaner and offer further precision. But as we have more attentively discussed above, the advantages offer much more than that. When diving into industry-specific projects we can see how laser welding serves as a versatile tool across a number of vastly different fields. From the small ring on your finger to the car you drive every day, Handheld Laser Welders have played a critical role in endless unexpected projects all around you.
———————————————————-
Did you know?
Laser welding technology is a well researched area by now, documented on many sites and publications. For starters you might be interested in our brief guide to laser welding. As a bonus to this article let’s rehash the two main processes of laser welding. Laser welding is possible in two separate modes: conduction-limited welding and keyhole welding. Both are utilized in different scenarios, but the overall application is extremely similar.
Conduction-limited welding is only used when the laser’s power density is less than 0.5 Mega-watts per centimeter squared, as noted by data collected from Amada Weld Tech. Power density is considered the amount of power per unit of volume, or the ratio of available power and volume. A higher power density is not associated with better performance, different values are simply used for different methods. Conduction limited with a lower power density is typically for projects that do not require penetration of the material. In this method, the laser beam only impacts the absorption of the surface of the material, rather than creating depth.
The keyhole welding method is used with higher power densities, where the focused laser beam actually perforates the material. The created cavity is called a “keyhole.” Since the power density is around 1.5 Mega-watts per centimeter-squared in this method, the laser will not only melt the material but will also vaporize it. As the heat source progresses, the keyhole is filled by this molten metal and metal vapor. Once the material cools completely, the cavity is transformed into a solid weld.
To see this machine in action, and to gain a better visual understanding, watch the video below:
Laser Welding can be performed on a variety of commonly materials. Some of these include die steel, carbon steel, stainless steel, copper, plastic, and numerous other metal alloys. The preferred type of laser is a CO2 laser, typically fiber or pulsed.