The new technology of Jewelry Laser Welding has seemingly revolutionized the jewelry industry. With what appears to be a few simple flashes of light, jewelers are now able to repair countless valuable pieces without the risks of damage during soldering, which could easily destroy precious materials. In this blog post, we will discuss the adoption of these machines, their features/technology, and their advantages as an alternative to traditional methods.
Welding in the Jewelry Industry
Laser Welding has been extremely popular since around the 1970s, yet its applications were typically reserved for the medical and aerospace industries until recently. In the past decade, smaller-scale laser welders have become essential in various types of jewelry repair projects.
The very first laser welders were produced as large stand-alone units, but the advancement of this technology has led to the production of smaller desktop machines. The smaller machines offer the same advantages as their larger counterparts, still providing extreme precision and speed.
Jewelry Laser Welders were seemingly adopted into the jeweling industry by the year 2007 when the MJSA trade group (Manufacturing Jewelers and Suppliers of America) recognized talent in a new design category. The new category included a distinct classification for laser repair and production, introducing the technology as an option for various jeweling projects.
How do Jewelry Laser Welders Work
The central technology of Jewelry Laser Welders is the same as any other standard laser welder. The machine uses an amplified laser beam to create a concentrated heat source. This welding method often uses close to an infrared wavelength, and you can easily change both the resolution and speed that the laser operates at. The heat source is then directed toward the desired joint area, and the surrounding material is rapidly melted and cooled to form a clean weld.
Inner workings of a Jewelry Laser Welding Machine
Jewelry Laser Welders often look much like the one pictured below. They contain extremely advanced spot welding technology, executing precise repair on a variety of materials.

A typical Jewelry Laser Welding Machine. Note the hand ports for easy access to the workpiece. Almost always, they are also equipped with a binocular viewing port for easy positioning of jewelry articles.
This machine, as you can see from the smaller design, is constructed as a tabletop unit for jewelry welding use. Its laser output power can range between 100 and 150 Watts, and it operates in a pulsed welding mode with a wavelength of 1064 nm. Other notable features of this machine – and many other standard jewelry laser welders – are as follows:
- Ceramic condenser chamber that is resistant to corrosion and dangerously high temperatures. This ensures long chamber life despite the exerted heat during the welding process.
- Air and water-to-water cooling to stabilize temperatures during welding. This ensures stable laser operation with a constant output that ensures consistent results after each weld.
- Microscope and CCD double observation system that helps accurately position the jewelry articles to be welded.
- Control panel where frequency and other important parameters can be finely tuned in accordance with the project to achieve desired results.
These are some of the more important and typical features of jewelry laser welding machines. Different systems come with unique advantages that can be beneficial to specific jewelry applications.
How to use a Jewelry Laser Welding Machine?
To achieve a clean and precise weld, the operator must be somewhat experienced in managing the machine. The operator must control the beam generated from the machine, placing it in the designated area that needs to be welded for repairs or redesign. The machine is operated under a magnifier for prime visibility of the jewelry piece. As shown in the photo above, the operator will look through the mounted binocular viewing port. Most machines, if not all, contain an advanced automatic shading system to eliminate irritation to the eyes and protect users during operation. Apart from the precision required for placement, the machine is rather easy to use.
The machine is extremely user-friendly and the remainder of the process is essentially automatic. On many machines, the diameter of the laser can range between two-tenths of a millimeter up to two millimeters depending on the requirements of the project. So the user will simply change the parameters on the control panel. This laser beam control is one of the main advantages of laser welders compared with other soldering techniques. It offers the utmost precision and minimal post-weld processing.
Projects and Capabilities
Jewelry Laser Welders can be utilized for many diverse projects, whether that be for repair or production purposes. They can be used to fill voids, re-enforce bezel settings, correct manufacturing defects, resize rings and bracelets, and much more. All while bypassing the need to remove stones. The following short list describes a few of these applications more in-depth:
- Resizing: rings can be resized to a smaller or larger size. Once a ring is cut and the material is removed, the welding machine can conjoin the material back to its original closed shape. Alternatively, the laser can heat desired material in order to stretch the ring to the desired size.
- Repairing Bezel Settings: the prongs of a ring– which hold diamonds or other gemstones in place– can oftentimes become loose and threaten the safety of the gem. If not tended to, the gemstone can fall out of its setting. A jeweler can identify these faulty areas and use a jewelry laser welder to repair/strengthen broken prongs.
- Reassembly: broken necklaces and bracelet chains can be easily fixed using jewelry laser welders. When chain links are broken after wear and tear, the broken sides can be efficiently joined in a strong, precise weld.
Because the laser is so precise in its positioning and the process is exceedingly quick, no heat is transferred to surrounding metals or gems. The exact and careful nature of these machines makes them perfect for projects involving the most delicate of gemstones such as opals, emeralds, or pearls. This saves immense time and prevents the need to remove stones from their established settings.
To see these machines at work on delicate jewelry pieces, you can watch the videos linked below.
Are Jewelry Laser Welders Better than Traditional Methods?
Jewelry Laser Welders offer more advantages in comparison to traditional soldering methods than you may realize. To start, soldering is an extremely tedious and frequently messy process. The aftermath can result in discolored and dirty welds if executed incorrectly, so there is little room for error. Welding machines will provide clear and precise results every time, always giving jewelry pieces a polished finish.
Soldering materials can also change color with time. So, pieces repaired using soldering methods can easily show wear and tear like the ring shown below. This requires an extended polishing process to restore the original shine of the article.
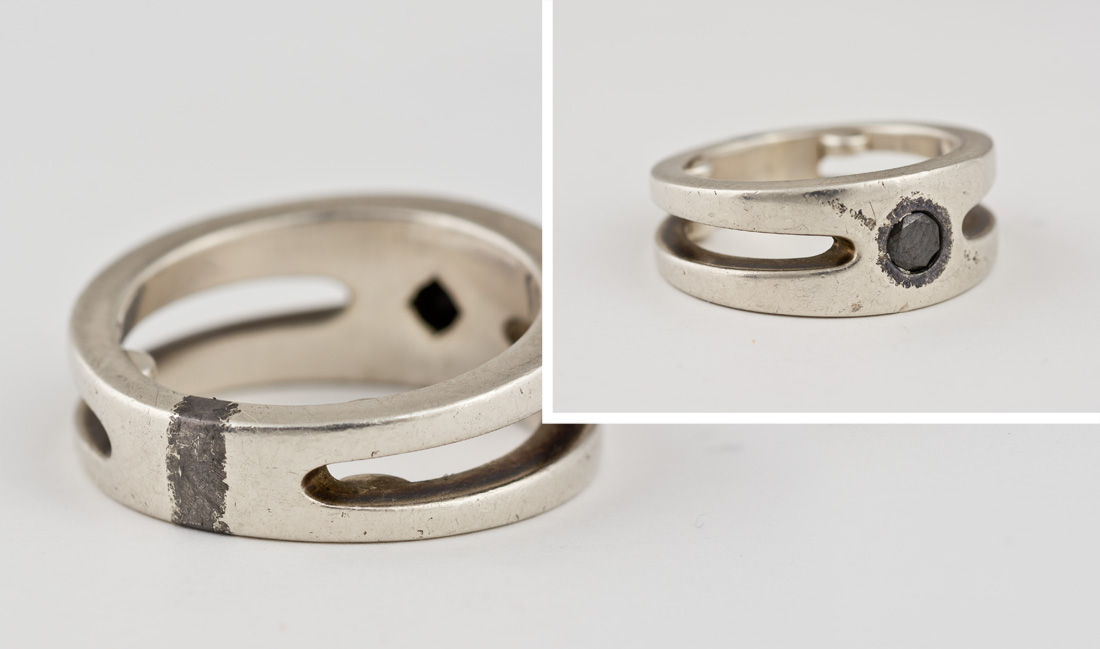
A ring repaired using soldering methods has severely tarnished over time.
Another noteworthy advantage of this process is the total time saved and ultimate efficiency. With these machines, repairs that once required multiple steps – disassembly, unsetting stones, completing the repair, and finally re-setting stones – can be completed in a single step. By bypassing these now unnecessary preemptive steps, repair jobs that once required hours of work can be completed within a mere five minutes.
One of the only disadvantages acknowledged for these machines is oftentimes their larger price tag. However, their price turns to profit rather quickly. Significant time savings leads to higher productivity, and ultimately a much more profitable business. Jewelry Laser Welders have revolutionized the jewelry industry, and they will continue to do so as their availability expands.
Did you know, at FindLight we have a dedicated category for Jewelry Laser Welding Machines, directly sold by leading suppliers worldwide. If you are considering buying one of those machines you can start your comparison shopping at that link above.
Did you like this article? If you did, please subscribe and share. If you have additional insight into jewelry laser welding, please comment below.