This guide is brought to you by DataRay, Inc. — Pioneering the future of laser beam profiling.
Introduction
Laser beam quality is a fundamental parameter that determines the effectiveness and precision of laser systems across various applications, from industrial manufacturing to scientific research. Engineers and scientists rely on high-quality beams to achieve optimal energy delivery, minimal losses, and superior focusability. The parameter M², known as the beam propagation ratio, provides a quantitative measure of how closely a laser beam approaches the theoretical ideal Gaussian beam.
M² directly influences critical properties such as beam divergence, focal spot size, and energy density — factors that are essential for applications demanding high precision and efficiency. For instance, in material processing, an optimal M² ensures tighter focus and cleaner cuts, while in spectroscopy, it enhances measurement accuracy by minimizing beam distortion.
This guide serves as a comprehensive reference for understanding laser beam quality, with a focus on M², its measurement, and its impact on practical applications. By mastering the principles discussed here, you can make informed decisions when designing, optimizing, or deploying laser systems for your specific needs.
1. What is M² and Why Does it Matter?
The beam propagation ratio, denoted as M², is a dimensionless parameter that characterizes the quality of a laser beam by quantifying its deviation from the ideal Gaussian beam profile. In an ideal Gaussian beam, the intensity distribution follows a symmetrical bell-shaped curve, and its propagation exhibits minimal divergence while maintaining a small, well-defined waist. A beam with an M² value of 1 is considered ideal, as it represents a perfectly Gaussian beam. Real-world beams, however, are often affected by optical aberrations, thermal lensing, misalignment, and imperfections in the laser cavity, which degrade the beam quality and increase the M² value.
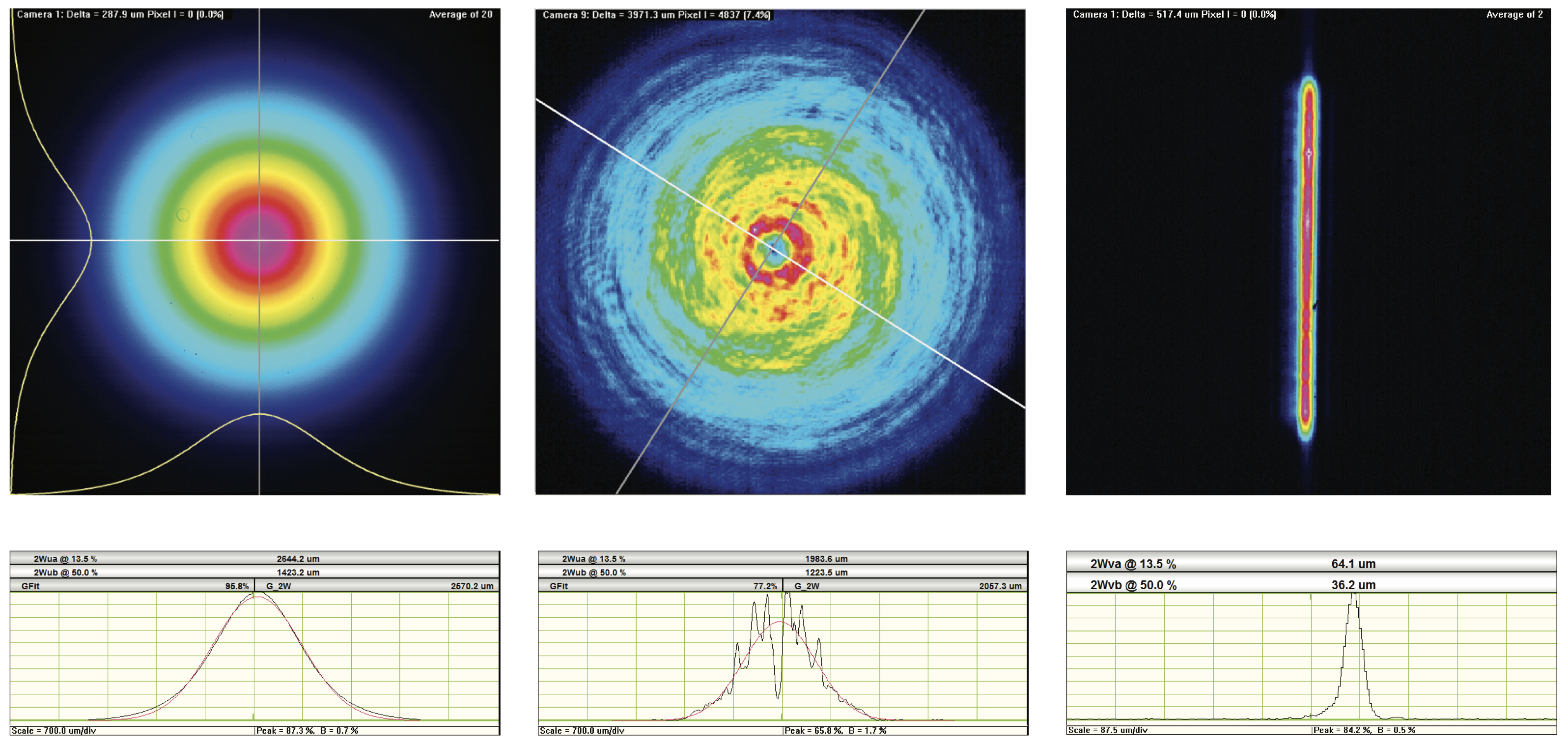
A visual comparison of an ideal Gaussian beam (M² = 1) and a distorted beam (M² > 1) to illustrate the impact of M² on beam quality. Image courtesy of Dataray, Inc.
1.1. Explicit Definition and Calculation of M²
Mathematically, M² is defined by comparing the divergence and waist properties of a real beam to those of an ideal Gaussian beam. It is calculated as:
M² = (θreal · w0) / (θGaussian · w0)
Where:
- θreal: The divergence angle of the real beam.
- θGaussian: The divergence angle of an ideal Gaussian beam.
- w0: The beam waist radius (the point of minimum beam diameter).
Alternatively, M² can also be expressed in terms of the beam parameter product (BPP), a product of the beam’s waist radius and divergence:
M² = BPPreal / BPPGaussian
1.2. Why it Matters to Have a Good M² Value
The impact of M² extends to fundamental beam properties such as focusing ability, energy density, and spot size:
- Focusing Ability: A lower M² enables a smaller diffraction-limited focal spot, enhancing precision in material processing or medical applications.
- Energy Density: Beams with low M² concentrate energy more effectively, making them ideal for applications that require intense localized energy.
- Spot Size: A beam with higher M² produces a larger focal spot, reducing its effectiveness in tasks requiring fine resolution.
Understanding and optimizing M² allows engineers and scientists to select the right laser for their application, ensuring performance is aligned with operational requirements. Whether in industrial, medical, or research settings, controlling M² is key to leveraging the full potential of laser technology.
2. How is M² Measured?
To determine the beam propagation ratio (M²), the following detailed steps are typically followed:
- Measure the Beam Profile Across the Propagation Path: The intensity distribution of the beam is captured using a beam profiler, such as a CCD camera or scanning slit profiler. Measurements are taken at multiple points along the beam’s propagation axis to map how the beam’s diameter changes with distance. This step ensures a comprehensive understanding of the beam’s behavior across the propagation path.
- Determine the Beam Waist Size (w₀): The beam waist, denoted as , is the location where the beam diameter reaches its minimum value. This point is critical because it represents the focal point of the beam. The waist size is typically measured with high precision using a profiler, ensuring accuracy for further calculations.
- Calculate the Divergence Angle: The beam’s divergence is determined by measuring its diameter at several distances from the waist. The divergence angle, , is calculated by fitting these measurements to a linear model in the far-field region (beyond the Rayleigh range). Divergence quantifies how rapidly the beam expands as it propagates.
- Fit the Measurements to a Propagation Model: A propagation model, such as the ABCD matrix or Gaussian beam propagation equation, is applied to the measured data. This model is used to derive the M² value by comparing the actual beam propagation characteristics to those of an ideal Gaussian beam. The fit provides a quantitative assessment of the beam’s deviation from the ideal profile.
3. Tools Used for Measuring M²
Accurately determining M² requires specialized tools designed to measure and analyze the properties of laser beams. These tools enable precise characterization of the beam’s profile, waist, divergence, and propagation. Below are the primary tools used for M² measurement:
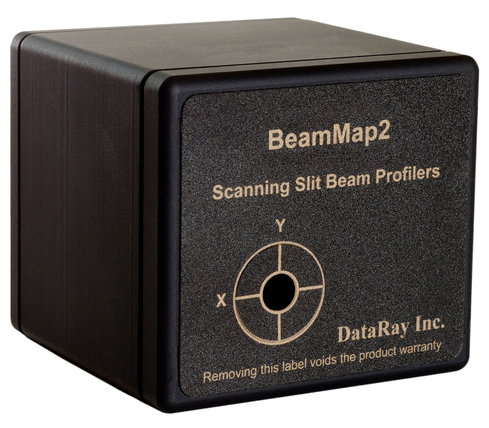
The BeamMap2 system is a multi-plane beam profiling with real-time M², divergence, pointing stability, and focal measurement capabilities. Image courtesy of DataRay – a leading supplier of beam profiling systems.
1. Beam Profilers: Beam profilers are essential instruments for capturing and analyzing the spatial intensity distribution of a laser beam. There are several types of beam profilers, each suited to different applications:
- CCD Cameras: Widely used for visualizing and measuring beam profiles, CCD cameras provide high-resolution intensity maps of the beam’s cross-section. They are ideal for continuous wave (CW) and low-power lasers.
- CMOS Cameras: Similar to CCD cameras but typically faster, CMOS cameras are suitable for applications requiring real-time measurements of high-speed beam dynamics.
- Scanning Slit Profilers: These devices use a slit that scans across the beam, measuring intensity at different points to construct the profile. They are especially effective for measuring high-power lasers.
2. Wavefront Sensors: Wavefront sensors, such as Shack-Hartmann sensors, measure the phase distortion of a laser beam. While not directly used for M² calculation, they complement beam profilers by identifying aberrations that can affect M².
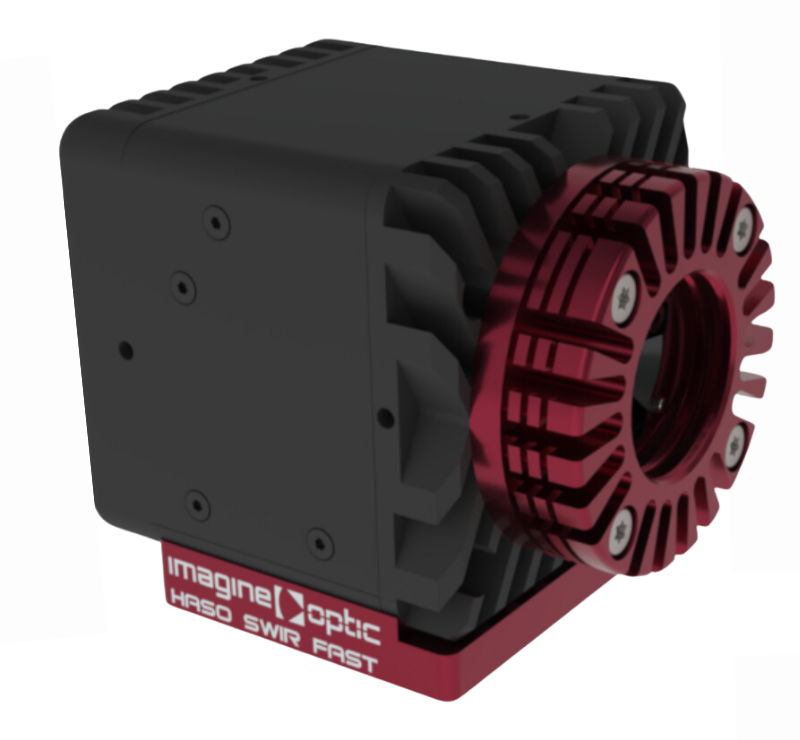
The HASO SWIR FAST Wavefront sensor delivers high temporal resolution and accuracy in SWIR bandwidth, ideal for adaptive optics and atmospheric turbulence characterization. As seen on FindLight.
3. Knife-Edge Scanners: Knife-edge scanners measure beam diameter by moving a sharp edge across the beam and recording the power loss. They are a simple and effective method for determining the beam’s waist and divergence.
4. Power Meters: Power meters are often used alongside beam profilers to measure the total energy or power output of the laser. This helps correlate intensity distribution with overall beam quality.
5. Beam Expanders and Reducers: Beam expanders or reducers are auxiliary tools used to adjust the beam size for measurement purposes. They help ensure the beam is appropriately scaled for the profiler or other instruments.
6. Software for Data Analysis: Modern M² measurement relies heavily on software to process the captured data. Many beam profiling systems come with dedicated software capable of fitting the measured beam propagation to a Gaussian model, calculating divergence, waist size, and ultimately the M² value.
Choosing the appropriate tools depends on the laser type, power level, and application requirements. For example, high-power lasers may require robust scanning slit profilers with damage-resistant optics, while low-power lasers might be better suited to high-resolution CCD cameras.
4. Impact of M² on Laser Applications
The M² parameter is critical for determining the suitability of laser beams across diverse applications, where precision, focusability, and energy efficiency are essential.
In industrial applications such as cutting, engraving, and welding, a low M² value ensures tightly focused beams with smaller spot sizes and higher energy densities. This leads to cleaner cuts, reduced kerf widths, and improved processing efficiency. Low M² lasers are particularly advantageous in micromachining and semiconductor manufacturing, where precision and minimal heat-affected zones are critical.
In medical applications, low M² lasers are indispensable for procedures like LASIK surgery, tattoo removal, and skin resurfacing. Their tightly focused beams allow precise targeting of tissues while minimizing collateral damage, ensuring faster recovery times and better patient outcomes. For instance, excimer lasers with low M² are essential for reshaping the cornea with high accuracy in ophthalmology.
In scientific research, lasers with low M² are crucial for high-resolution spectroscopy, metrology, and atomic physics experiments. These applications demand high spatial coherence, enhanced focusability, and consistent beam quality to ensure reliable and reproducible results. Low M² lasers enable precise cooling and trapping of atoms, a critical process in advanced research.
Across these fields, understanding and optimizing M² enhances laser performance by delivering energy with minimal distortion and maximum precision. This makes low M² lasers a cornerstone of innovation in industries ranging from manufacturing to healthcare and fundamental research.
5. Factors Influencing M²
The M² parameter is influenced by several factors that affect a laser beam’s ability to maintain its ideal Gaussian profile. Understanding these factors is essential for optimizing beam quality and ensuring reliable performance across applications. Below are the most common contributors:
1. Optical Alignment and Lens Quality: Poor optical alignment and subpar lens quality are significant contributors to increased M² values. Misaligned optics cause beam distortion, introducing aberrations that disrupt the Gaussian profile. Additionally, lenses with surface defects, coatings inconsistencies, or improper curvature can scatter or distort the beam, further degrading its quality. Ensuring precise alignment and using high-quality optical components are critical for maintaining a low M² value.
2. Thermal Effects Within the Laser Cavity: Thermal effects, such as heat-induced lensing and deformation of laser cavity components, can significantly impact M². As the laser operates, heat generated within the cavity alters the refractive index of the gain medium and optical elements, causing unwanted changes in beam propagation. These effects lead to beam distortion, increased divergence, and a rise in the M² value. Active cooling systems and thermal management techniques can mitigate these effects, preserving beam quality.
3. Power Scaling and Its Impact on Beam Quality: Scaling up the power output of a laser often leads to compromises in beam quality. High power levels intensify thermal effects and exacerbate non-linear optical phenomena within the laser medium, both of which contribute to higher M² values. Power scaling must be carefully managed by optimizing the laser design and materials to balance output power and beam quality effectively.
By addressing these factors — optical alignment, thermal management, and power scaling — you can minimize M², ensuring the laser performs at its optimal potential for precision and efficiency.
6. How to Optimize Beam Quality
Optimizing beam quality is essential for ensuring a laser system performs at its peak potential. One of the most effective strategies is to use high-quality optics designed for the laser’s wavelength and power. Poor-quality lenses or mirrors can introduce aberrations, scatter, and energy loss, all of which increase the M² value. Additionally, ensuring precise optical alignment is critical. Misaligned components distort the beam path, degrading focusability and increasing divergence. Regularly checking and fine-tuning alignment can significantly improve beam quality.
Routine maintenance of the laser system is another vital step. Dust, debris, or contamination on optical surfaces can scatter light and reduce beam quality. Moreover, thermal effects within the laser cavity, such as heat-induced lensing or component deformation, can negatively impact the beam’s Gaussian profile. Implementing proper cooling systems and cleaning protocols helps maintain system stability and reduces these effects over time.
Finally, it’s crucial to match the laser’s M² to the specific application’s requirements. For instance, industrial cutting or welding processes benefit from low M² values for tighter focus and higher energy density. On the other hand, applications like illumination may tolerate higher M² beams. Selecting a laser with the appropriate beam quality for the task ensures both efficiency and performance.
By investing in high-grade components, adhering to regular maintenance schedules, and aligning the laser’s beam quality to its application, you can achieve optimal results. These steps not only improve precision and reliability but also extend the lifespan of the laser system, maximizing its value across a range of applications.
7. Conclusion
Understanding and optimizing M², the beam propagation ratio, is fundamental for achieving precision, efficiency, and reliability in laser applications. Whether in industrial manufacturing, medical procedures, or scientific research, beam quality directly impacts a laser’s performance and suitability for specific tasks. A low M² value ensures tighter focus, higher energy density, and minimal beam distortion, enabling superior outcomes in processes ranging from material cutting to atomic physics experiments.
By assessing M² and other beam quality metrics, you can make informed decisions when selecting lasers for their projects. Choosing the right laser and maintaining optimal beam quality ensures not only enhanced performance but also long-term system reliability. Emphasizing beam quality in the selection process is essential for maximizing the potential of laser systems across diverse and demanding applications.