What exactly is Laser Depaneling? In today’s blog post we’ll discuss just about all you need to know about Laser Depaneling.
A Basic Intro to Laser Depaneling Lingo
Before we get into the standard technology of Laser Depaneling, let’s discuss a few of the basic terms.
- PCB (Printed Circuit Board): a baseboard which is used in electronics manufacturing to assemble and connect various electronic components.
- Depaneling: a process commonly used in high-volume electronics assembly production to separate individual PCBs from their overall panel.
- Laser Depaneling Machine: a device used for the separation of PCBs using a CO2 or UV laser.
- Depaneling Router: machine used to mill the material of the PCB using a router bit.
- HAZ (Heat Affected Zone): area of a material being laser cut that is impacted by the local heat of the laser.
These are some notable terms that may be valuable to reference as you read further.
Laser Depaneling Technology
Laser Depaneling has become one of the most favorable methods for cutting and separating printed circuit boards to be removed from their original panel. It’s an extremely flexible and precise method, offering a new innovative approach to a once tedious process.
The technicality of the process is not overly intricate, so it proves rather user-friendly and easy to execute. During the depaneling process, PCBs are cut from their original panel using a suitable processing tool. In the case of laser depaneling, this processing tool is generally a CO2 or UV laser. Determining the correct laser for the project is one of the most important aspects of this process. So choosing the right laser should be a top priority.
The deciding factor for laser selection typically has to do with what takes priority in the project: overall cycle time or the cleanliness of the cut edge. To gain a better understanding of when to use each laser, let’s discuss their pros and cons.
CO2 Lasers
CO2 lasers are more frequently used for projects desiring perforated cuts, although they can be used for full cuts as well. Executing perforated cuts reduces the amount of char commonly found with full cuts. It also simplifies the loading and unloading of panels from the cutting machine, as the panel is still removed in one piece. Because the cuts are perforated, cut PCBs can be fully removed from the panel at a later time. Finally, as panels increase in thickness so does the elapse in production time, so CO2 is the preferred laser for thicker materials.
In summary:
- Pros: faster cutting speeds, an option of perforated or full cut, lower costs per watt during production time, can process aluminum panels.
- Cons: more charring on the cut edges (less pristine appearance), larger HAZ.
UV Lasers
UV lasers use cold-cutting technology, so there is less probability of charring on the edges of the panel. So if minimizing char assumes more prominence than a shorter production time, UV lasers are the best choice. This is important for achieving cuts of medical or engineering industry quality. UV cuts will completely isolate the PCBs, so cleanup can prove more tedious in comparison to when perforated cuts are used
Summary
- Pros: exceptionally clean cuts, narrower laser diameter (higher precision), smaller HAZ, can process copper.
- Cons: longer cut/production times, more expensive.
To gain a better visual understanding of how this process works, check out the video below.
Laser Depaneling Machines
Most Laser Depaneling machines look much like the one pictured below. This machine offers accuracy of 2 nanometers, and a laser output power of 20W. The standard work area for a depaneling machine offers at least 1,225 sq. cm in space (350 mm x 350 mm). This machine includes precise thermal control, a marble tabletop for better stability, and extremely high UPH rates (units per hour).
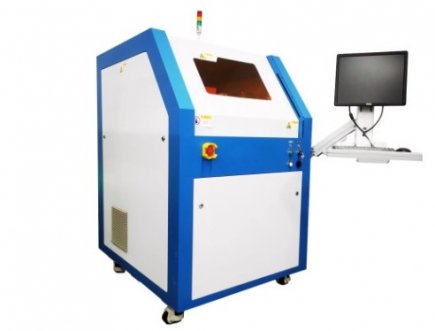
ZMLS1000 Genitec PCBA-FPC Laser Depaneling Machine (as seen on FindLight)
Benefits and Limitations of Laser Depaneling Machines
Laser depaneling is a no-contact method, so there are less limitations when it comes to execution. The laser can cut in any pattern including intricate shapes and turns. This leaves fewer restrictions to straight lines, which is commonly seen with other manual methods. When using a standard depaneling router, there is extensive maintenance concerning the sharpening or replacement of bits/blades. Lasers bypass these requirements, making these machines easier to finance. In regard to operation, the advanced software controls allow for swift change between numerous different cut patterns. Cuts can be scheduled using pre-programmed cut patterns, further bypassing the need to set up the machine each time a new panel is loaded. When different panels are loaded into the machine, there is also no need to realign bits/blades or switch mechanical parts.
For some, the only downside to laser depaneling is the larger price tag in comparison to different methods for PCB depaneling. This leads to the conclusion that these are truly remarkable machines for mass production.
Conclusion
Circuit boards or panels typically contain very delicate materials, making laser depaneling a perfect choice for components that can be damaged easily. In recent decades manufacturers have adopted Laser Cutting and Laser Routing as their primary depaneling methods, essentially due to the advantages described above. With their unbeatable precision and speed, they will continue to further the production of electrical components in a variety of industries.
Interested in purchasing a Laser Depaneling machine? Start your comparison shopping here at the FindLight website and browse among our suppliers to determine which machine meets your personal needs! Also check out our Technical Guide to Laser Scan Heads.
If you have any additional insight on the topic, feel free to leave your thoughts in the comments. If you enjoyed this article on Laser Depaneling, please subscribe and share.