Laser drilling has found many applications in precision machining, microelectronics, chip fabrication, tablet drilling, and dentistry. The high aspect ratio of this process and its non-contact nature allowed it to compete and become on par with traditional machining processes such as mechanical drilling or electrochemical machining (EDM). But what is laser drilling? How different is it from conventional machining techniques? And what are some of its most prominent applications? In the rest of this article, you will find answers to these questions.
What is laser drilling?
It is a noncontact machining technique of creating a single hole or an array of holes on the surface of a material by removing some of that material. This is performed by using a single pulse or multiple pulses of short or ultrashort powerful laser beams guided by a beam focusing system. It can also be performed using a continuous-wave laser, but compared to pulsed lasers, continuous wave lasers have higher risks of thermally damaging the material.
In laser drilling, the size of the created hole is defined by its depth, and width or diameter. The depth and the width of the generated holes can both reach a few millimeters, but the latter is typically smaller and on the order of tens of microns. In this case, the machining process is called laser micro-drilling. Typically, these holes have diameters ranging between 5 µm and 1500 µm, but recent reports show that laser drilling can generate holes as small as 1 µm in diameter.
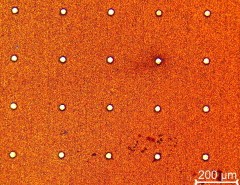
Optical Microscope Image of an Array of Holes Drilled by a CO2 Laser. Courtesy of ScienceDirect.
In addition to the different sizes, the drilled cavities also come in different geometries: microvias, simple holes, and channels. Such drilling techniques have unique applications as we see below.
How does laser drilling work?
Also referred to as laser ablation, laser drilling employs a laser beam to rapidly increase the temperature of the material or substrate to the melting or evaporation temperatures. The material can be removed by melt expulsion also known as melt ejection or vaporization. Vaporization creates very well-defined and clean holes with minimal damage to the surrounding material, but it requires more energy than the melt expulsion mechanism.
Typically, the energy needed to remove material through vaporization is 4 times larger than that needed to melt the same volume. Since this process depends on the workpiece material, higher energy levels are sometimes required. And while material removal via melt expulsion is more energy efficient, it generally generates irregular and asymmetric holes.
The removal process depends on the material, the laser, and the laser parameters used. Thanks to the controllable laser beam size, the heating can be confined to the area irradiated without affecting the surrounding areas.
Advantages
This machining process can be performed on any class of materials. It can be used on high-strength materials such as super-alloys and brittle materials such as ceramics which are difficult to machine using conventional drilling processes. It is important to note that the choice of laser used depends on the material.
As previously mentioned, laser drilling is a non-contact process that does not require tooling. Unlike mechanical drilling, parts of laser ablation systems do not wear or break over time hence the durability and cost-effectiveness of this machining process.
In addition, the drilling of shallow angle holes is crucial for the aerospace industry, where it has always been challenging to perform mechanical drilling. Shallow angle holes require secondary processes and additional tooling. These challenges are completely eliminated using laser drilling. By simply rotating the laser beam, the needed angle is achieved, and angles as small as 10 degrees from the surface can be realized.
Furthermore, high aspect ratios with depth-to-diameter greater than 10:1 can be achieved using laser drilling. High aspect ratio holes are especially crucial to the aerospace industry. The same results cannot be reached using conventional machining methods as they tend to heat up or break due to an increase in pressure.
Applications of Laser Drilling
Many industries rely on laser drilling for large-scale production, and below we list some of the most prominent ones:
1. Aerospace Industry
Laser drilling is particularly vital for the aerospace and automotive industries as they require shallow-angle drilling. Perhaps one of the most important applications of this process in the aerospace industry is the drilling of holes in turbine engine components such as blades, combustors, and nozzle guides to improve their cooling capacity.
2. Oil and Gas industry
Drilling is also essential for the research and development of oil and gas fields. However, rock drilling is costly, and costs have the potential to increase with increasing difficulties. These problems can be avoided using laser drilling. In addition to the properties listed in previous sections, laser systems used for drilling are light compared to conventional systems. They also offer higher processing rates as it is easier to penetrate the rock using lasers.
3. Microelectronics
Another industry that depends on laser drilling is the microchip fabrication industry. In this industry, there are increasing efforts to improve the performance of microelectronics and reduce their size. This requires an increase in the density of interconnecting and interfacing through high-resolution microvias. The drilling of dielectric layers in microchips is commonly achieved by means of photolithography.
However, this etching process is restricted to a class of material known as photo-imageable organics. This challenge is overcome by using laser micromachining processes which have the capacity of drilling polymers and insulating films while maintaining a high resolution. Laser processing is also involved in different stages of microelectronic fabrication including surface cleaning and treatment. This makes those machines a rather versatile tool for such applications.
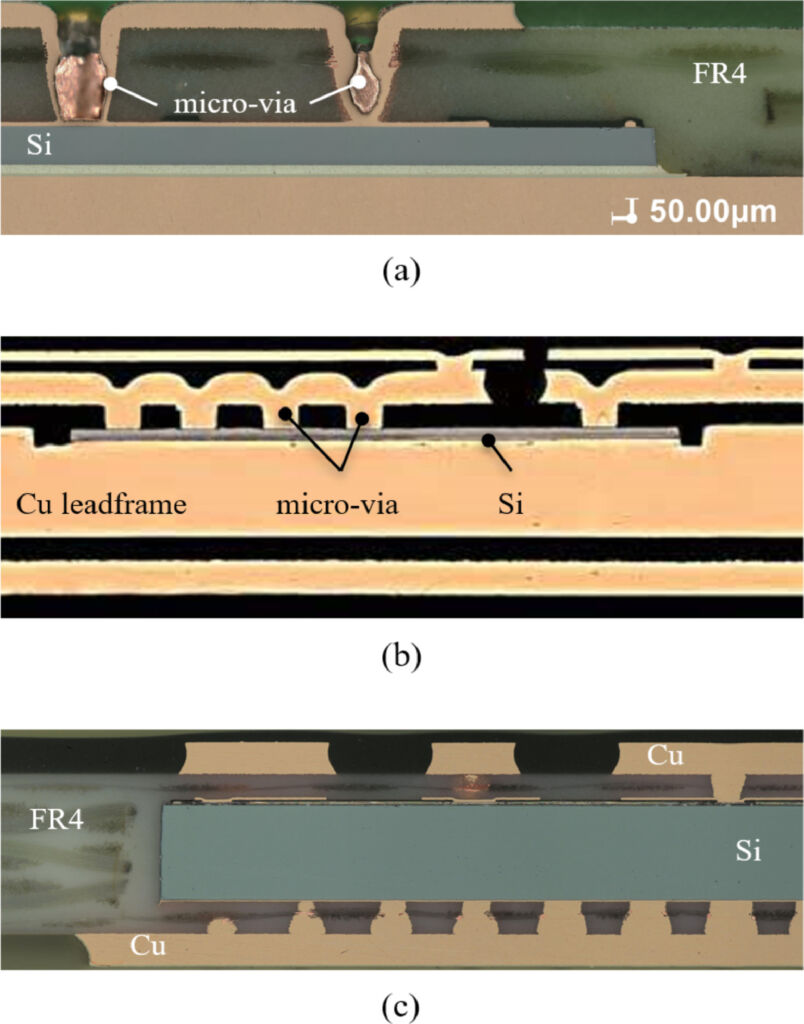
Cross section of a PCB (Printed Circuit Board) showing different microvia drilling. Courtesy of ScienceDirect.
4. Pharmacy
Today, lasers are used in many fields of medicine, but they are notably popular in the pharmaceutical industry where laser drilling systems are used to drill up to 140,000 tablets per hour. While it seems trivial, this process is of immense importance as it prevents counterfeiting.
Conclusion
Laser drilling remains an active area of research that is continuously expanding to new industries and applications. Recent reviews are calling for further investigation of the thermal effects of laser drilling. Means of controlling the thermal damage, especially on the nanoscale, has become a center of active research in recent years.