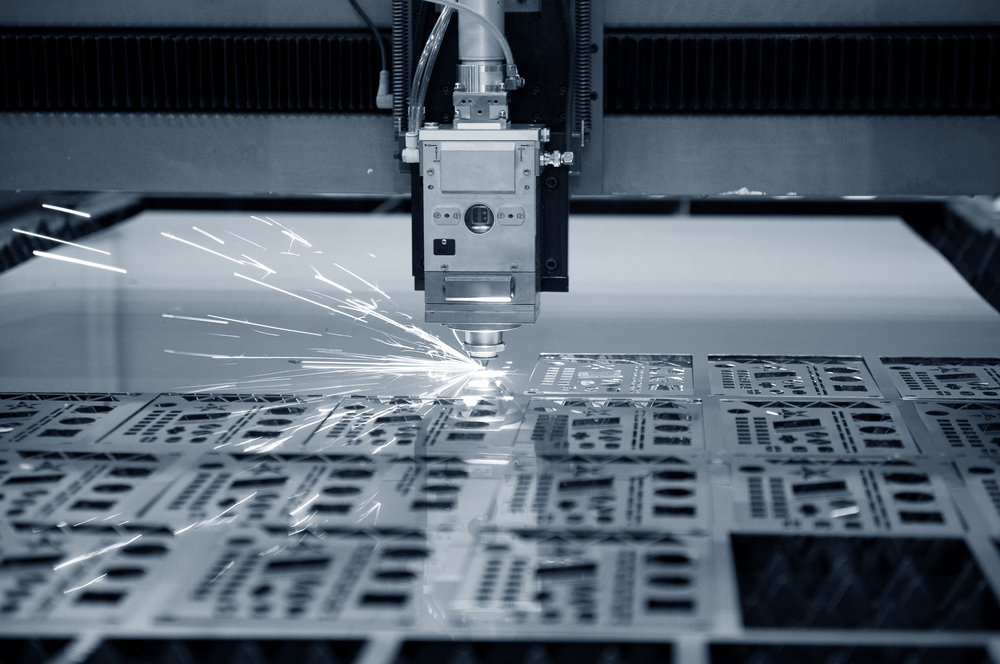
The design of a laser marking system needs to consider various factors. The picture shows a working laser marking head. Courtesy of Machine Service Inc.
In the last article we presented a thorough discussion about the principles of laser marking mechanisms. In this post we will proceed to review the design of different laser marking systems. Compared to the selection of proper light sources, choosing a suitable laser marking system is enormously complicated by many practical factors, such as the materials to be marked, the throughput, the permanence, the flexibility and the tolerance of the substrates. Each must be evaluated on its own merit and the final plan is a reconciliation of all aspects.
What Is A Laser Marking System Made Of?
A laser marking system consists of three major parts: a light source, a controller, and a surface. The laser is like a pencil—the beam emitted from it allows the controller to trace patterns onto the surface. The controller is a computer embedded with automation algorithms to monitor the direction, intensity, speed of movement, and spread of the laser beam aimed at the surface. The surface is picked to match what the laser can act on. If the material is vaporized during marking process, ventilation equipment such as blower or vacuum pump is required to remove the noxious smoke and debris on the surface to guarantee continuous marking. In addition, elaborate cooling systems are used to dissipate heat of the laser and target, and many factories now adopt pulsed lasers to decrease the collateral heating.
Available Types Of Laser Marking Systems In The Market
There are three main types of laser marking systems. The most common one is the X-Y table where the workpiece (surface) stays still and the laser optics moves around in X and Y directions, directing the laser beam to draw vectors. A second type, namely drum marker is for cylindrical workpieces or flat workpieces mounted around a cylinder, where the on/off laser pulsing produces the desired image on a raster basis. In the third method both the laser and workpiece are stationary. A galvo system scans the laser beam over the workpiece surface. Laser marking systems using this technique can work in either raster or vector mode.
X-Y Table
An X-Y table is a sophisticated equipment platform used to guide the laser beam precisely. The laser is usually fixed to the side of the table and emits light towards a pair of movable mirrors so that every point of the table surface can be swept by the laser. At the point of marking, the laser beam is focused through a lens, hence, achieving very precise and intricate patterns on material surfaces. A typical setup of an X-Y table involves the fixed laser emitting light parallel to one axis of the table aimed at a mirror mounted on the end of an adjustable rail. The beam reflects off the mirror angled at 45° so that the laser travels a path exactly along the length of the rail. This beam is then reflected by another mirror mounted to a movable trolley, which directs the beam perpendicular to the original axis. X-Y tables make possible marking in two degrees of freedom (vertical and horizontal).
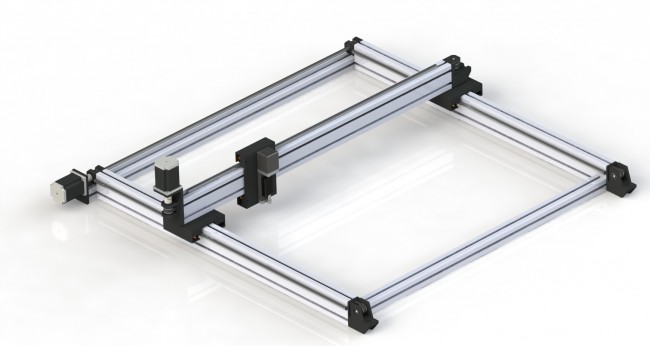
An x-y table with integrated stepper motors. Courtesy of SmartDrive
Drum Marker
In drum marking system, the laser beam is controlled to penetrate fixed depth in the material. In this manner, only a particular depth of material is removed when the marking takes place. A simple machined stick or angle-iron can be used to help technologists adjust the marker to achieve the required focusing. This setup is preferred for surfaces, which do not vary in height appreciably. For surfaces that vary in height, more elaborate focusing mechanisms have been developed. Some are known as dynamic auto focus systems. They adjust the lasing parameters in real time to adapt to the changes to the material as it is being etched. Typically, the height and depth of the surface is monitored with devices tracking changes to infrared or visible light aimed at the marking surface. These devices, known as pilot beams or pilot lasers provide guidance to adjust lens in determining the optimal spot to focus.
Mirror Galvanometer
A mirror galvanometer is an instrument that can manipulate mirror positioning fast and precisely for the deflection of laser beams. In laser marking systems, a galvanometer plays an essential role in the beam scanning part, and allows for pattern marking with high resolution.
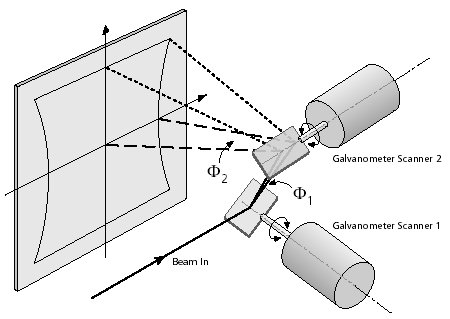
Deflection of a laser beam with two galvanometers. Courtesy of www. zamisel.com
Two Working Modes of A Laser Marking System
Vector Mode
Vector marking follows the line and curve of the pattern to be marked. It works similarly to a pen that draws by constructing line segments from pattern outline. Early laser marking systems working in vector modes exhibited several problems, and a prominent on is the moiré effects. Now with the introduction of the PostScript page-description software (like CorelDRAW or Adobe Illustrator), virtually anything that can be defined in vectors by the software could be laser-marked with high quality.
Raster Mode
Raster laser marking systems scan the surface in a back-and-forth, slowly advancing manner. The pattern is usually optimized by the controller/computer so that areas to either side of the pattern, which aren’t to be marked, are ignored and the trace across the material is thus shortened for better efficiency. The amount of advance of each line is normally less than the actual dot-size of the laser. As is true of all rasterized devices, curves and diagonals can sometimes suffer if the length or position of the raster lines varies in relation to the adjacent raster scan; therefore exact positioning and repeatability are critically important to the design of the system. The advantage of rasterizing is the near effortless “fill” it produces. Most images to be marked are bold letters or have large continuously-marked areas, and photos call also be well-rasterized with dots larger than that of the laser’s spot. More importantly, almost any page-layout software can be used to feed a raster driver for an drum laser marking system. Thus, although many modern shops reserves vector marking to speedily mark outlines, they tend to run their laser marking systems mostly in raster mode.
To learn about laser marking systems and conduct comparative shopping of different systems, visit our page on Laser Marking Machines.