Introduction and motivation
The manufacturing sector has paid a lot of attention lately to additive manufacturing (AM). By adding layer after layer of material, AM is one technology that creates three-dimensional objects. AM is a very promising method for creating intricate, expensive components for a variety of markets, including the aerospace and automotive sectors. In this article, we discuss a specific type of AM for the aluminum alloy. Our article is mainly based on the study done by the researchers at Beijing University of Technology in China.
Over the past thirty years, a variety of approaches have been developed in the field of AM. AM can be divided into three categories: arc additive manufacturing, electron beam additive manufacturing, and laser additive manufacturing depending on the energy source used for metal deposition. Arc additive manufacturing equipment has a low cost, but it uses a lot of heat, which causes a lot of residual stress and deformation. High vacuum conditions are necessary for electron beam additive manufacturing, and the equipment is expensive. A quick and adaptable production process called laser additive manufacturing (LAM) is utilized to produce versions with intricate geometrical designs (see Figure 1).
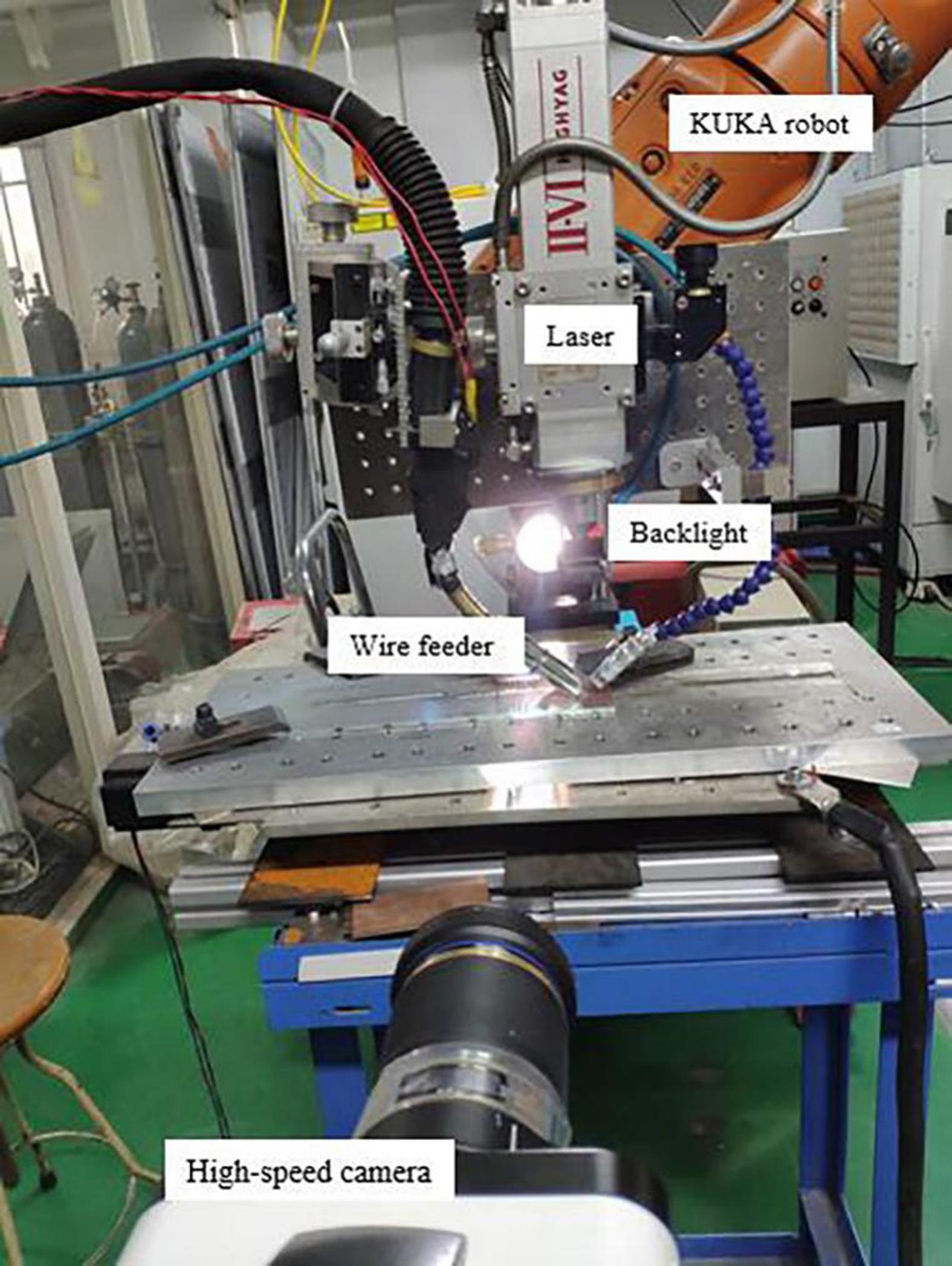
Figure 1: Experimental setup for LWMAM system. Image courtesy of Elsevier
Laser additive manufacturing
The metallic powder or wire is delivered using this technique, which first employs the laser as a heat source to create a small melt pool on the substrate surface or a previously deposited layer (see Figure 1 and Figure 2). The clad solidifies and creates an impenetrable link with the original surface as a result of the relative movement of the substrate and laser.
As a result, a three-dimensional object is built up gradually. A laser, robot, and deposition feeding system are all parts of the LAM system. After a single layer has been completely deposited, the process is repeated while moving the laser beam and deposition feeding system relative to the layer.
Additive manufacturing (AM) of metal components, using a laser beam as a heat source, has a number of benefits, including high energy density and low heat input, minimal thermal deformation of the workpiece, quick heating and cooling speeds, The small grain size of the formed part, no or minimal requirements for the manufacturing environment, no vacuum atmosphere, no electromagnetic interference, and trajectory walking are additional benefits of the LAM.
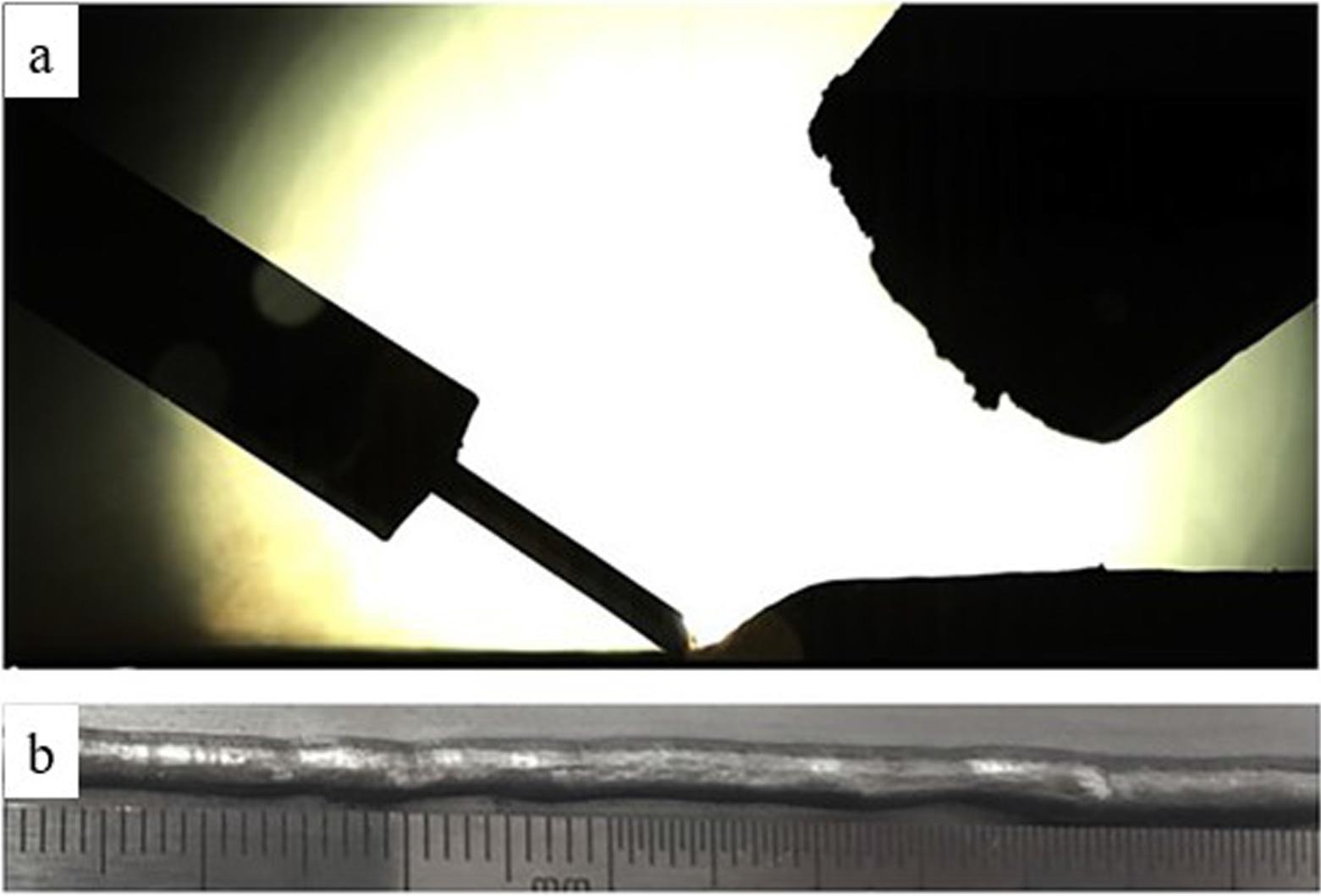
Figure 2: Deposition at the front feeding. Image courtesy of Elsevier
Laser wire-feed metal additive manufacturing
Automation and intelligence are flexible and simple to implement. Regarding the additive material form, laser additive manufacturing (LAM) can be separated into powder-based and wire-based systems. Over the past 20 years, a lot of research has been done on the powder-based laser additive manufacturing technology.
However, the adoption of powder-based LAM technology was severely constrained because of its expensive cost of metallic powder, low material utilization rate (20%-30%), environmental contamination, and threat to the operator’s health.
Laser wire-feed metal additive manufacturing (LWMAM) has a number of benefits over powder-based LAM, including a greater material usage rate (almost 100%), higher deposition rate, lower material cost, less pollution, etc.
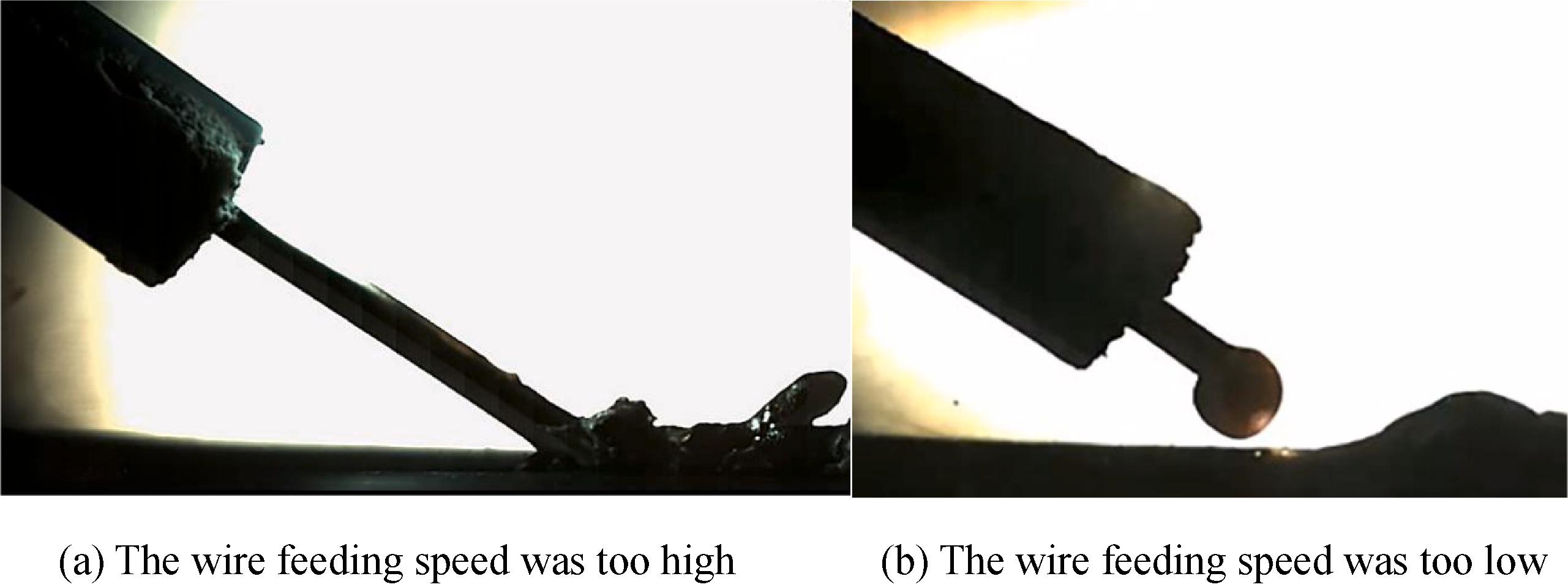
Figure 3: (a) Wire feeding speed was too high (b) Wire feeding speed was too low. Image courtesy of Elsevier
Efficiency of LWMAM
Different industrial areas, such as aerospace, automotive, and quick tooling, have shown interest in these benefits. Currently, the majority of LWMAM research is concentrated on the LWMAM method, such as forming accuracy and forming size.
The process parameters, benefits, and drawbacks of wire- and powder-feed direct laser deposition are contrasted. It was discovered that wire feeding had significantly higher deposition efficiency than powder feeding. It was realized that wire feeding from the front produced clad of higher quality than back feeding, which resulted in serrations.
On the weight and dimensions of the deposited single tracks, other researchers evaluated the effects of the wire feeding direction and angle, as well as the effects of the laser power, traverse speed, and wire feed rate (see Figure 3). The procedure and the geometrical properties of the track were discovered to be strongly influenced by the wire deposition volume per unit length of the track and the energy per unit length of the track.
The distance between the wire feeding system and the substrate and the ratio of the laser beam to wire width were two processing parameters. It is discovered that the former influences the wire tip’s pressure on the molten pool and the molten metal transfer mode, whilst the laser beam to wire width ratio influences the process effectiveness (see Figure 4).
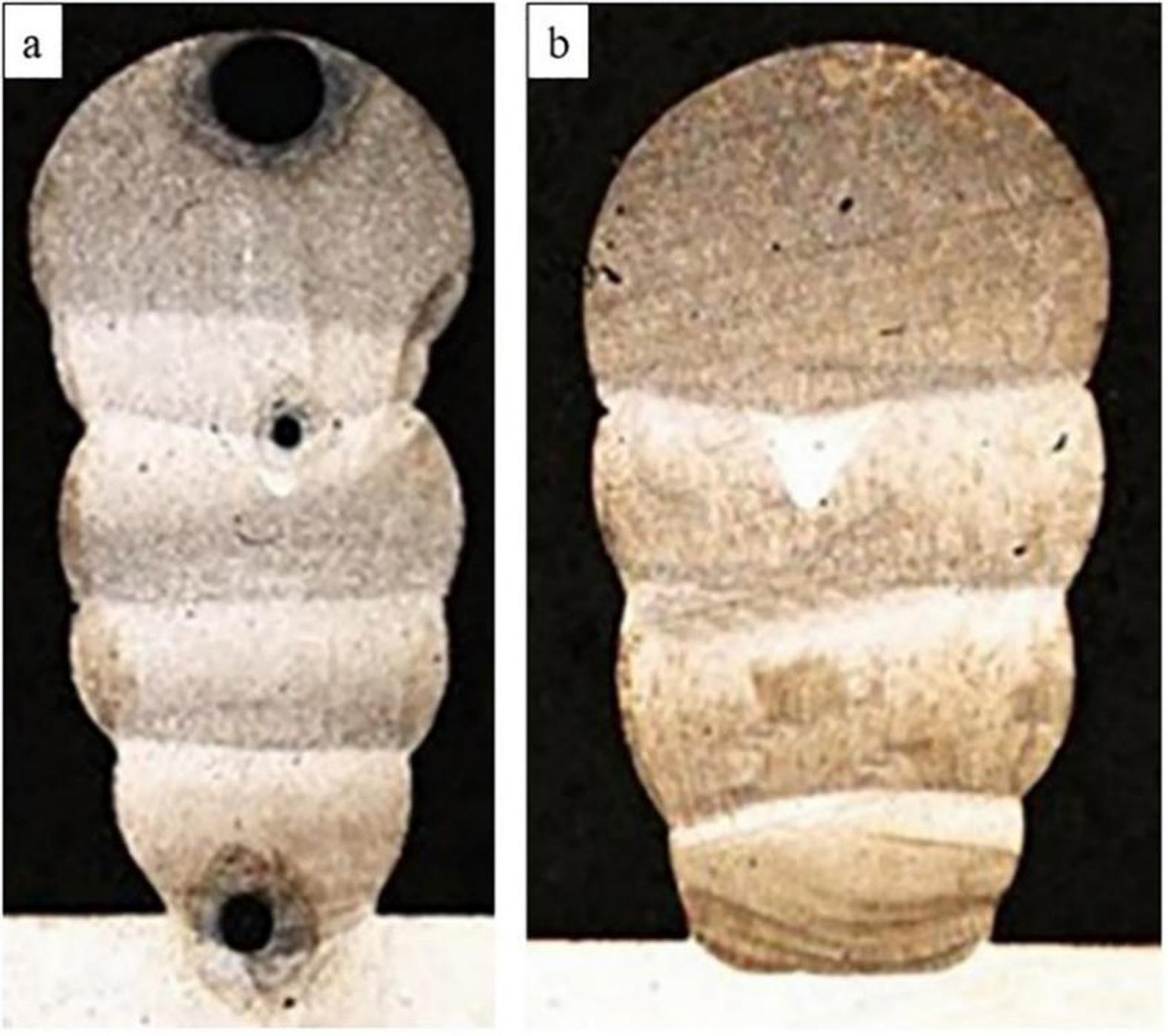
Figure 4: Cross-section images of the multi-layered depositions (a) with non-optimized process parameters (b) with optimized process parameters. Image courtesy of Elsevier
Key results and take-home massages
Although it is now possible to create structures using LWMAM that are free of different materials like iron and titanium alloys, there is still a dearth of information about LWMAM of aluminum and its alloys.
The following are the key causes: First, low density and poor fluidity are traits of aluminum alloys. Second, the process is challenging to manage and has high requirements for wire feeding stability. Last but not least, the wire surface has a high laser reflection rate. Due to these factors, the process is highly challenging to manage. LWMAM process windows must therefore be properly set up in order to obtain high efficiency. The use of a laser beam to deposit Al alloy 5A06 wire was studied in this study by creating single- and multi-layered tracks.
Prior to examining the effects of the primary process variables, such as laser power, traverse speed, and wire feed rate on the geometry properties of the deposit, the effect of the wire feeding direction and angle was initially examined. The experimental specimens were prepared for optical microscopy observation by being cut, ground, and polished. The measured data was then compared to the projected values predicted by the mathematical models.
Images of the weld pool and droplet transfer, which demonstrated the stability of the welding process, were taken using a high-speed camera system. Finally, utilizing the adjusted process settings, a thin-wall part was created without any discernible pores, cavities, or flaws.
Summary
In this article, the use of a laser beam to deposit Al alloy 5087 wire was discussed by creating single- and multilayered tracks as well as the processing conditions necessary for a stable deposition.
Following is a summary of the main findings of this study:
- Traverse speed was a major factor in determining the deposition height, but laser power has a bigger impact on the deposition width.
- The relationship between the LWMAM process parameters and the width and height of the track layer geometry was determined using a second-order polynomial equation. By knowing one of these, the models may solve either the process parameters or the geometrical characteristics.
- The overlap ratio and the increment of height are the two key factors that determine the process stability in multi-layered deposits. The multi-layered deposits exhibit trace porosity at an overlap ratio of 33.33% (the height increase is roughly 66.67% of the single-layer height).
This article was brought to you by DataRay, a leading developer and manufacturer of laser beam measurement solutions.