Material surfaces are not as smooth as they seem. They have microscopic irregularities that can only be seen when magnified. These irregularities are called microstructures. When properly engineered, these microstructures can have unexpected effects on the physical properties of the surfaces of materials. For instance, one can create an extremely hydrophobic surface by making a regular pattern on the surface of a polymer. This can be done using different techniques, such as hot embossing, electrochemical machining, or laser texturing. Recently, laser texturing has gained popularity due to its precision and ease of use. In this article, we will introduce laser microstructuring techniques, focusing on their applications to polymer surfaces.
1. Why are Polymers Good Candidates for Laser Microstructuring?
Polymers are macromolecular chains made from smaller repeating structures, called monomers. There are both natural polymers, like rubber and cellulose, as well as synthetic polymers. Both types have many uses, including in biomedicine, engineering, and product development. Within optics, polymers are used to create lenses, films, filters, gratings, and more. Creating these optical elements out of polymers instead of traditional materials, like glass, reduces labor and cost to create them while increasing the production speed and quality.
The most common types of polymers used are acrylic, polycarbonate, and polystyrene. The desire for miniaturization within technology development, makes polymers an increasingly appealing material to work with as it is relatively inexpensive and easy to use. Further, by altering the topography of the polymer surface, through the use of laser texturing, you can alter the properties of the material.
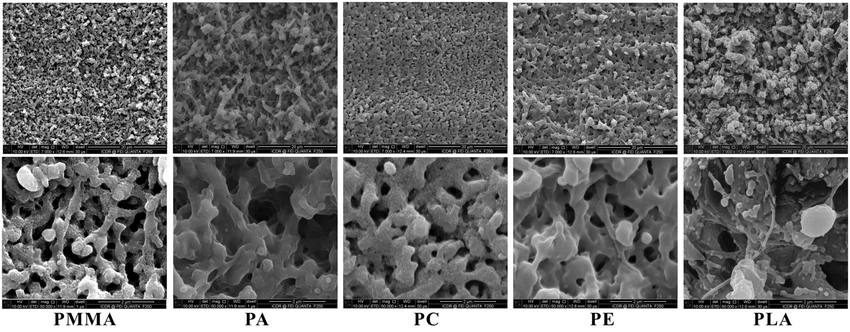
Magnified images of different polymer surfaces after exposure to a femtosecond laser pulse. Courtesy of Advanced Material Interface
2. How does Laser Microstructuring Work?
Like laser marking there are two main techniques for creating microstructures on a surface: removing excess material from the surface and adding new material to the surface. Both have found many useful applications within technology, biomedicine and other areas. Most of these techniques use the energy of a focused laser to melt the polymer before manipulating it into the desired pattern. In the following three sections we will look into three different techniques for laser microstructuring:
2.1. Laser Ablation
Laser ablation is a well established technique that selectively removes material from a surface. When applied in a control fashion it can be used for laser microstructuring. The laser micromachining set up in this case will need to attain sufficiently high power output, very short pulse durations or a combination of both to deliver significant peak powers. Such lasers interact with polymers by ablation, or removal of material by vaporization and melt expulsion. This means the laser beam needs to have high enough peak power per pulse to induce a phase transition. The first instance of laser ablation used with polymers was reported by Cozzen and Fox in 1977, where they used a 10.6 μm pulsed CO2 laser.
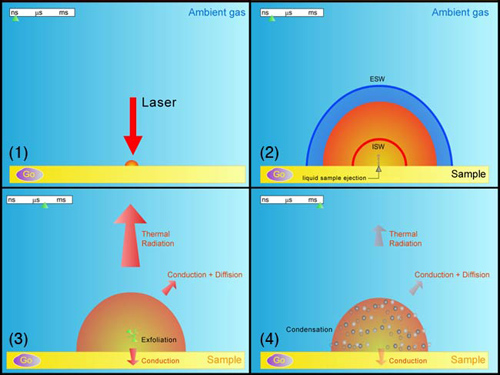
An illustration of the laser ablation process. Courtesy of Applied Spectra, Inc.
If a high powered laser is not an option, some people choose to use a lower power laser and rely on the thermal properties of polymers. In this case, the area near the laser beam is simply melted away. This will also happen if the energy output of the laser is less that the ionization potential of the chosen polymer valence electrons. However, this method is less precise as the melting process invariably impacts the surrounding area.
Power is not the only parameter that can be altered to manipulate the ablation of a material. For example, a lot of research today investigates how tailored temporal profiles of a femtosecond laser pulse reacts with polymer surfaces. One group uses a Yb-doped fiber-amplified femtosecond laser system to fabricate microstructures on reinforced polymer substrate.
2.2. Direct Laser Writing
Much like laser texturing, direct laser writing (DLW) is a laser microstructuring technique that employs a focused laser to fabricate 3D structures. This is done through a process call multiphoton polymerization. When, the laser irradiates an area, multiple photons are absorbed by the atoms, an idea first proposed by Maria Göppert-Mayer in 1931. This requires high intensity lasers and when applied to the surface of a polymer, allows for microscopic structures to be created.
Further, since the material is not being removed, but rather, more material is being added to the polymer surface, an additional material is required. Typically, a photosensitive emulsion, also called a photoresist, is layered on the surface before being irradiated by the laser. Once the laser beam is applied, the photoresist reacts to the laser beam through multiphoton absorption polymerization. Afterwards, the excess photoresist is washed off with a chemical bath. However, this means that the irradiated emulsion needs to anchor onto the surface or it will be washed away.
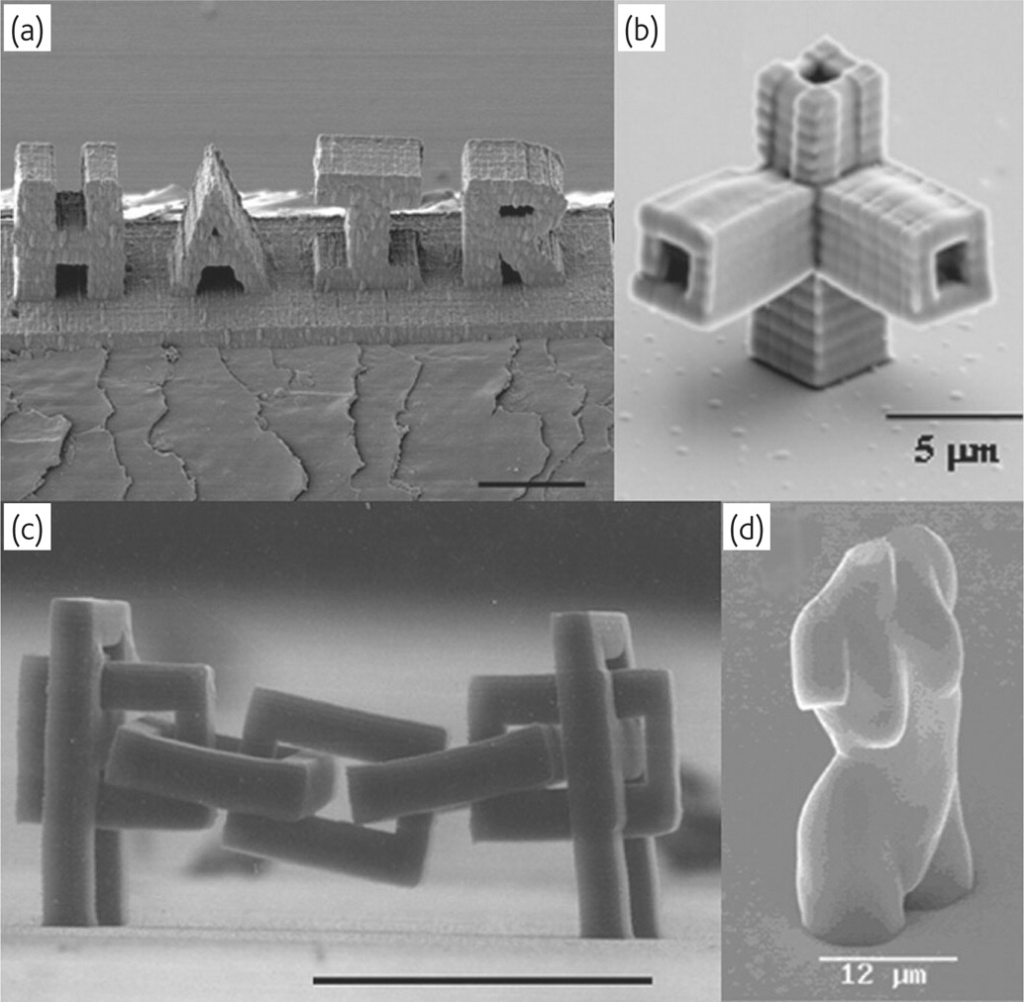
Micro and Nanostructures created on different surfaces using multiphoton absorption polymerization, a key element of DLW. Courtesy of Materials Today
2.3. Optical Lithography
Optical lithography is another laser microstructuring technique that has found a widespread applications in semiconductor industry. Like DLW, optical lithography, or photolithography applies a laser to the surface of a material that has been coated in a layer of photoresist. However, a mask is inserted in the laser beam before it is focused to the target area. This alters the intensity of the laser beam according to the pattern on the chosen mask. This means that a macroscopic mask can be created and illuminated, creating a pattern in the laser intensity profile. Lithography has been an essential advancement that has led the frontier of miniaturization of electronic circuits.
3. Laser Microstructuring on Polymers to Create Hydrophobic Surfaces
Now that we’ve discussed some methods for laser microstructuring or surface texturing, we will look at some applications. One example was mentioned above, creating hydrophobic surfaces. In general, the roughness and regularity of the material surface directly relates to the wettability of the material. Whether a surface is hydrophobic or hydrophilic is dependent on the contact angle a drop of water makes with the the surface it rests on. This is demonstrated in the image below, where θ is the contact angle.
The degree by which a surface is hydrophobic is related to the surface tension, interfacial tension, and surface free energy through Young’s Equation. More acute angles indicate that a surface is hydrophilic, and obtuse angles occur on hydrophobic surfaces. Introducing grooves to the surface through laser texturing ensures that liquid will always have a contact angle greater than 90° with the surface. Different groove patterns, both regular and irregular, produce different wettability properties.
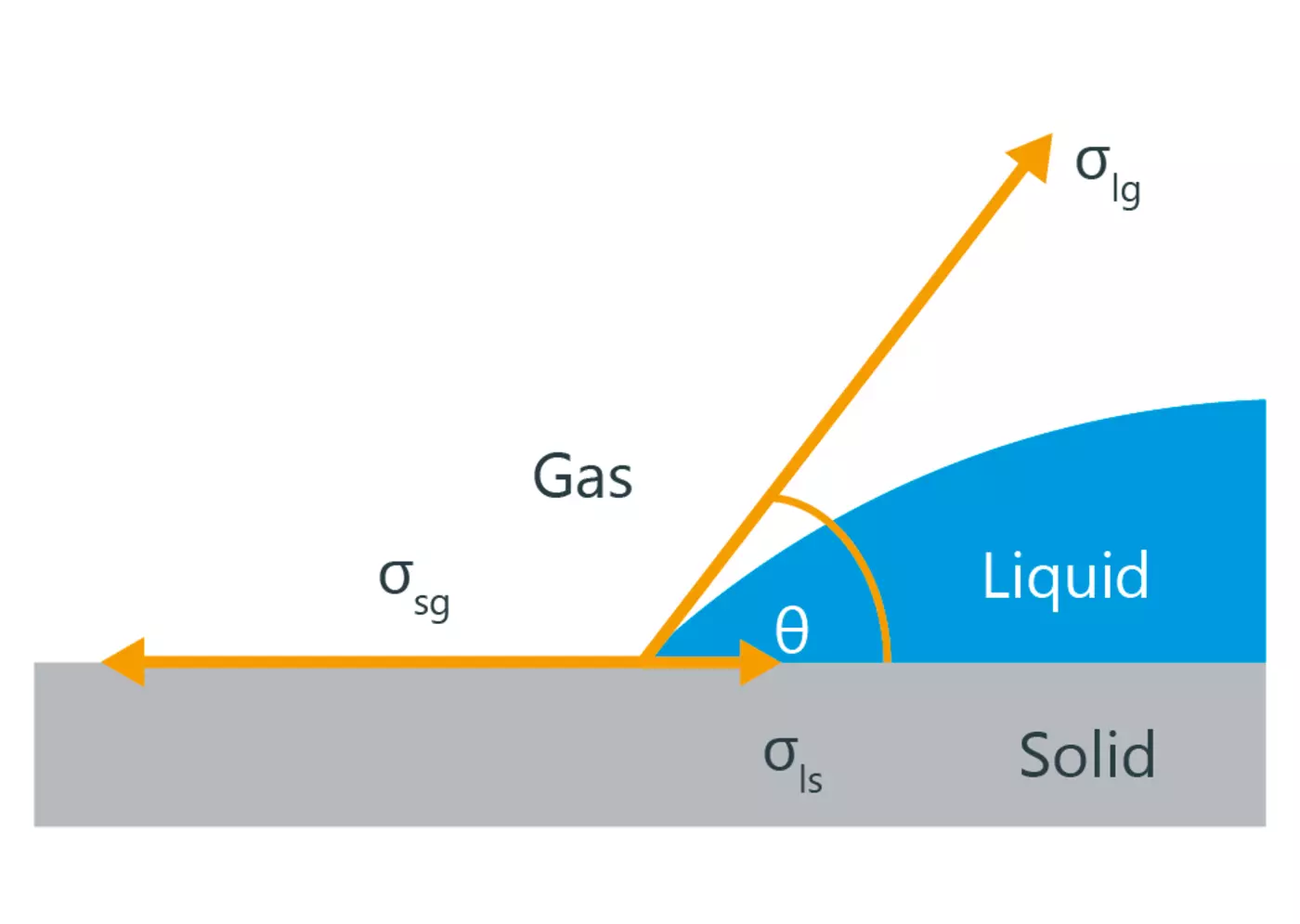
An illustration of the contact angle between a liquid and a solid. Courtesy of Krüss Scientific
On the other hand, hydrophilic surfaces can also be created by engraving patterns into the surface of a polymer. One group attempted to create a paper like surface on a polymer by creating a porous structure. They wanted to imitate the water absorption properties of paper, which absorbs and transfers liquids through capillary action. This is a phenomenon where water moves through porous material by adhesion, cohesion, and surface tension.
One research group used a 158 fs laser with a center wavelength of 780 nm to engrave grooves a few micrometers in diameter into the surface of a PMMA substrate. Water introduced to the grooved surface filled the grooves and had a contact angle less than half a degree. The microgrooves also demonstrate a filtering capability using artificial blood. They report that the filter worked best for a smaller microgroove width (9.1 μm compared to 20.1 μm) and will require optimization for whichever samples it is used with.
4. Laser Microstructuring in Biomedicine
Since polymers are widely used in biomedicine, its useful to be able to control how hydrophobic or hydrophilic a material surface is. This is especially important when working with polymer implants, as the surface topography can impact how well the body responds to an artificial implant. Using an implant with more surface roughness both on a macro- and microscale can help keep the implant fixed in place. For instance, bone implants with microstructured surfaces have a better chance of being integrated with the bone.
Polymers are also used in biomedical research. For example, they are used to determine the forces stem cells exert on their environment. Using DLW to create 3D structures above the material surface, one group created a spider web structure to detect the force exerted by cells. This structure consists of several pillars connected by threads and arranged in a spider web pattern. When stems cells are added to the surface, they exert forces while accessing their surroundings. In this way, the stem cells are trying to figure out where they are in the body in order to determine which cell type to become.
Laser microstructuring is an important manufacturing technique that is finding an increasingly axial role in engineering of new metamaterials that pave the way in many areas of electronics, bio-medicine, optical cloaking and more.
Today's blog post was sponsored by art photonics - a leader in the development and production of specialty fiber products