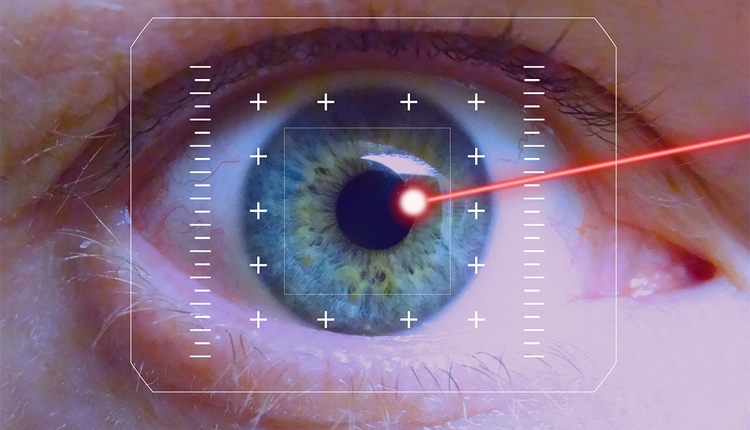
The broader future we envision for lasers, the higher standards imposed on laser reliability. Courtesy of startlr.com
What is Laser Reliability?
Ever since its creation, laser, the “sacred lightsaber”, has become a secret weapon to unravel the cutting-edge problems in numerous scientific and engineering fields. The burgeoning novel applications also lead to a wide spectrum of lasers with difference specifications. However, from a 5$ laser pointer to a weapon-level chemical oxygen iodine laser, one key concern is shared permanently among all the manufacturers —laser reliability, which tells about the probability that a laser device can perform the intended functions during a characteristic time period under specified conditions.
Consequences When Your Laser is not Reliable..
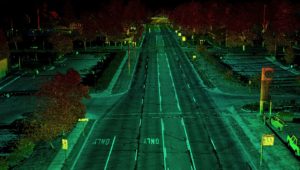
Light Detection and Ranging (LiDAR) Techniques will be the “eyes” of self-driving cars. But will you let go the steer when the “eyes” are not reliable?
Reliability is a pivotal concept for laser manufacturing, and poor laser reliability is more than a headache of receiving incessant quality complaint at customer service. This is because lasers usually undertake high-precision detection and measurement tasks, and one minor error can irreversibly sabotage all previous efforts. A daunting example is that in semiconductor industry, a lithography light source (usually an ultraviolet laser) shutting down could cause a loss of more than $10 per second (or over 1 million Dollars per day) for chip makers, and to fix the laser can possibly take more than 24 hours. Similar issues in other fields are beyond imagination: What if the fine-tuned, well-calculated laser used in the retina surgery suddenly goes to greater intensity? What if the laser in a mobile LiDAR system stops generating light beams for path detection? Thus, laser reliability determines whether the power of laser is effectively harnessed for right purposes.
Weak Links You Should Know About Your Lasers
Needless to say, laser reliability is an integral standard that covers the condition of every part of a laser device: The pumping source which is either electrical or optical, the gain medium ranging from gas, liquid to solid, and the optical feedbacks which are two mirrors with different reflectivity. Generally, component degradation and inherent design deficiencies are the two major type of factors that shrink the laser device lifetime, and real situations are sophisticated by the multiple available choices of materials and device structures.
For example, excimer laser used to suffer from issues with its plasma discharge tube, in which a gas mixture of a rare gas (krypton, xenon) and a halogen gas (fluorine, chlorine) serves as the gain medium. The corrosive gas and the high-voltage discharge would gradually erode the metal electrodes, creating dust, and therefore lowering the laser output. Another problem is the variation of pulse-to-pulse energy output resulting from the changes in the tubes. Consequently, the necessitated frequent cavity cleaning and gas refilling largely limited the lifetime of an excimer laser.
In a semiconductor diode laser, the Achilles’ heel hurts in a different way. A diode laser has a layer of intrinsic semiconductor material as the gain medium, and this layer is extremely susceptible to defects, either introduced by the impurities, or aggravated by current-induced thermal gradients. The dissipated heat can activate the growth of defect clusters and dislocation networks, which give rise to a higher threshold voltage and a reduced laser output. In addition, other factors like oxidation and meltdown of the mirror facets also contribute to a shortened lifetime and poor laser reliability.
As for the importance of pump source selection, a perfect example is the evolution of optically-pumped solid-state lasers. Previously, flash lamps were often used as pumping sources. However, a prominent problem was that flash lamps had very short life time, only around 500 hours for cw (continuous wave) operations and 108x shots for pulse modes. Remarkable improvements of the system reliability happened after replacing flash lamps with laser diodes, namely the DPSS lasers (diode-pumped solid state lasers). In addition to extended life times (104 hours for cw modes and 109 for pulse modes), laser diode pumping sources also exhibit new advantages, for instance, the high temperature stability in diode pumped fiber laser, and more system design freedom that allow higher efficiency and better beam qualities.
Facts About Laser Reliability in the Industry
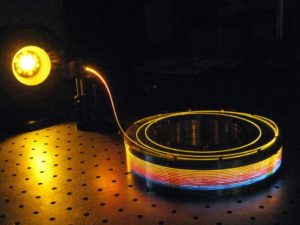
A typical fiber laser worths over 10 thousand dollars. Hence, doing thorough reliability tests are unrealistic
Because of the intricacy of reaching robustness consistency in products, reliability control measures have penetrated into every phase of product cycle, from proposal, design, fabrication, to customer use. Only then can a laser device be assured of qualification as a marketable product. Also, manufacturers have established a set of test programs, so called reliability engineering programs (REPs) and corresponding criteria to quantify the durability and the resilience responding to variables like temperature, mechanical stress etc. However, one point to keep in mind is that REPs serve for one ultimate goal: to enhance the financial strength of the corporation. Hence, a balance between REPs and other business aspects like budget and time etc has to be achieved. As a consequence, manufacturers have built statistics from the comprehensive reliability tests on the inexpensive semiconductor diode lasers, whereas the information for other devices, like fiber lasers and DPSS lasers, are more from field data due to their high prices.
What to Ask the Providers Before Buying Their Lasers?
Searching for lasers only with desired specifications might be a quick way, but it definitely cannot free you from latent problems. One thing to do before signing contracts is to know what customer groups the laser manufacturers aim for and how they expect their products to be used, because different users have different requirements on laser robustness. For a laser believed durable for welding and marking, its frequency to repair can be a nightmare for a semiconductor chip maker. Thus, before placing orders, it is necessary to survey what customers are typically on the laser providers’ radars.
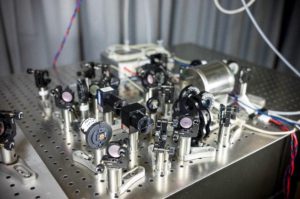
A diode laser is under reliability tests
Further questions that the buyers can ask are the reliability tests that the manufacturers have performed on their lasers. Information about the listed points can conveniently reflects the reliability of laser product:
- HALT (Highly Accelerated Lifetime Testing):. This is a methodology used by many manufacturing organizations to uncover the weak links of a product under stress conditions including: high temperature, high pressure and high voltage etc.
- HAST (Highly Accelerated Stress Testing): This is a scenario to test the reliability of laser components when working in humid environments.
- MTBF (Mean Time Between Failures): A term that provides the average number of failures per million hours. It is a common inquiry about a product’s life span.
- MTTR (Mean Time To Repair): This term represents the average time needed to repair or replace a failed laser device/module. As a usual part of a maintenance contract, it is important for the buyers to make sure whether delays like administration and technician transportation etc are included.
- Mechanical and Thermal Testing: These tests investigate the mechanical integrity and thermal endurance of a laser device. Through test details, buyers can determine the lasers that fit best for their specific situations, since some may need lasers that can be stored at extreme temperatures while others probably want lasers that can work in a large temperature range; some might prefer lasers that can withstand strong instantaneous shock while others desire lasers immune to constant shear. Here is a humorous video showing how the famous laser manufacturer Laser Quantum tests the robustness of their gem laser products.
- Field Data: For some very expensive laser devices like fiber lasers, even though it is understandable that related test data are rare, buyers can still expect the laser manufacturers to disclose field data of laser reliability and relevant policies about how they dedicate to meet customers’ needs seamlessly.
In a word, the most efficient way to select a proper laser device is to clarify the working situations, and then ask the manufacturers whether they have satisfactory data in their reliability tests and customer feedbacks.
[…] lasers are of high reliability and almost maintenance-free, and since the optical path is enclosed within protective cladding […]
Interesting and worthwhile article about the reliability of lasers and laser-based systems in industrial and research environments, but not one single word about safety-related issues. Addressing these issues on one of the places where laser professionals need to up their game Niel
This is a great suggestion Niel. Perhaps we will devote one of the future articles to laser safety issues.