Wire stripping said simply, is the removal of insulation covering electrically conducting wires. But what is the most efficient and cost-effective way to go about doing it? Laser Wire Strippers are a modern technology that automates and gives precision to this process.
What are Laser Wire Strippers?
The general process of wire stripping involves the removal of sections of shielding surrounding wires and cables. But the execution must be careful so as to not damage the components beneath. This process is vital in nearly any electrical project since it’s used to provide more electrical contact points across a conductor. Standard wire strippers, resembling a pair of household pliers, are shown in Figure One.
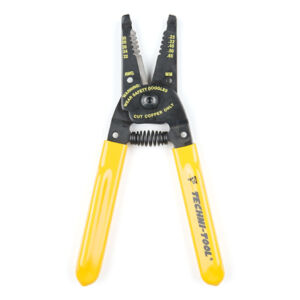
Figure 1: A typical household wire stripper
These were the typical tools of choice for the task prior to technical advancements.
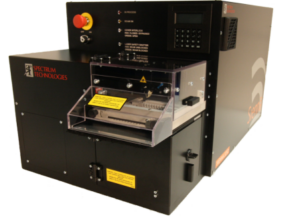
Figure 2: Laser Wire Stripper
Laser Wire Strippers were first created and tested by the National Aeronautics and Space Administration in the nineteen-seventies. The machines were initially created to overcome problems encountered in the electrical development of the first Space Shuttle, Enterprise. They later became exceedingly popular in the aeronautical, defense, and medical markets across a variety of electrical projects. The lasers allowed for new levels of precision and control, during a process that was once considered extremely tedious.
The Technology
Introduction
At the core of laser wire strippers is the process of melting and ablating insulation coating by a laser beam. As the laser’s energy is absorbed by the surrounding insulating material, it vaporizes under intense heat and pressure. To achieve a precise cut, the laser beam must first be focused onto the very exact position where it is needed. This is done by special lenses which direct and focus the laser beam precisely onto the area to be stripped.
Next, the laser moves along the circumference of the wire, stripping the desired area of insulation from the conductor. Alternatively, depending on the type of machine, the cable can rotate while the laser remains stationary. If a more complex strip form is desired, the wire will then angle itself in accordance with the desired cut.
Heavier insulators require higher-powered stripping systems, entailing more modern methods that can execute complex strip patterns. These complicated strip patterns are ideal for fiberglass or cloth materials. The laser wire stripper, shown in Figure 2 above, is an example of one of these further advanced systems. That system is a benchtop unit with a dual axis, which enables it to execute these intricate strip patterns at any point along the length or circumference of the wire. Bigger units like these increase efficiency rates and save time since they can process multiple wires and/or cables simultaneously.
When to use Laser Wire Strippers
Lasers are a perfect alternative to manual wire stripping when using thinner wires of higher monetary value. It executes a quick and precise cut with no residue, perfect for very fine wires used in important medical devices like catheters or pacemakers, where conduction reliability is vital. Aside from cutting high-quality cables, laser wire strippers are practical in scenarios with an abundance of labor-intensive wire cuts. More labor-intensive instances typically involve complicated wire shapes, bonded insulators, ribbon cables, or other wires. These wires stray from the stereotypical shape and functionality.
The possibilities are seemingly endless regarding projects that could involve laser wire stripping. These projects could easily range from simple electrical circuits as found in your home, to life-saving medical devices, or even complex astronautical machines that will someday leave the planet. Regardless of the ultimate need for these machines in any job, they exhibit major benefits in comparison to conventional methods.
Advantages and Disadvantages of Laser Wire Strippers
Benefits
The benefits of laser wire strippers surpass that of traditional wire strippers, particularly when taking into account their feasibility and quality of execution. They currently provide the highest achievable strip quality out of any products on the market, eliminating the possibility of previous manual errors that could cause delays and additional expenses in a variety of projects. The laser apparatus itself cannot damage the metal conductor, so with nearly complete elimination of error, this could maximize yields and ultimately reduce overall costs.
Laser wire strippers are practical for essentially all current insulator materials, with stripping capabilities for Silicone, PVC, Fiberglass, Nylon, Polyurethane, Polyester, Epoxy, Polyethylene, and countless others. Compatible cable forms include but are not limited to Single Core Wires, Twin Leads, Twisted Pairs, Ribbon Cables, Multi-Conductor Cables, and Coaxial Cables, a few of which are depicted below.
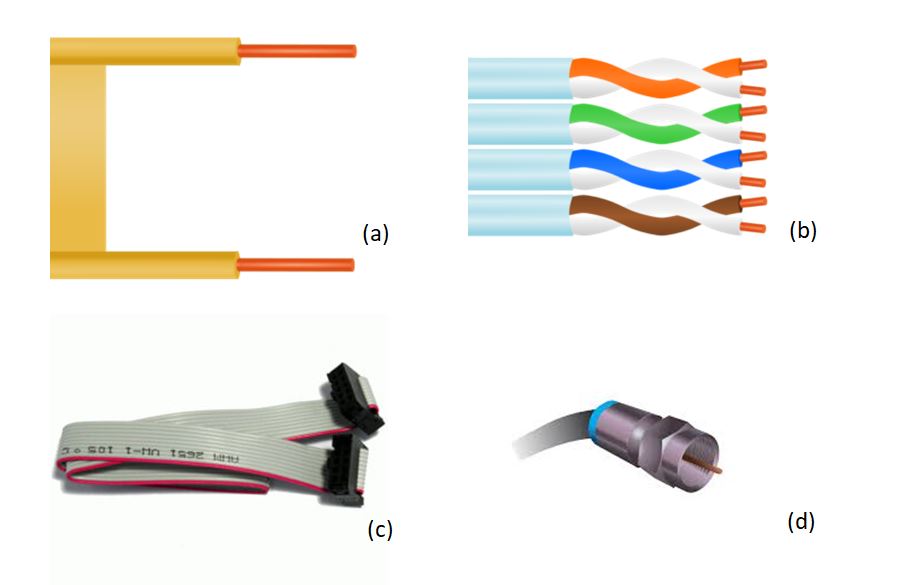
Different types of wires that can be striped using laser wire strippers: (a) Twin Leads Cable; (b) Twisted Pairs Cable; (c) Ribbon Cable; (d) Coaxial Cable
Capabilities
Apart from their extremely wide range of material compatibility, laser stripper’s advanced programming allows for a variety of strip patterns previously unachievable by manual methods. These unique cuts can come in numerous forms, the more elementary of which are described below.
- Cross Cuts: standard length cuts around the entire circumference of the cable, typically placed closer to the end of the wire.
- Cross Cut Slit: traditional cross-cut, with a connecting slit along the conductor that reaches to the very end of the wire (only on a portion of the insulator, not the entire circumference).
- Window: removal of a larger section of insulation along the length of the wire, leaving more area for conductor exposure.
- Angled Cuts: cuts in insulation that are not exactly perpendicular to the conductor but rather at a slight angle.
A final benefit presented by laser wire strippers is their ability to process multiple wires simultaneously. This is important in electrical projects requiring a copious number of stripped wires, or even tasks with stricter time constraints to abide by. The machines effortlessly increase productivity and cut back manufacturing times.
Limitations
The limitations of Laser Wire Strippers amount to very few, although their disadvantages could prove strenuous to some. The relatively large mass of optics in the machine somewhat limits the maximum possible acceleration or speed of the laser. Nevertheless, the ability of the machine to cut numerous wires at once somewhat negates this drawback of slower execution rates. One of the only other commonly noted downsides to laser wires strippers is their expense in comparison to manual strippers. Although the cost may only be unfeasible to project funds on a smaller scale.
With that said, the substantial benefits of laser wire strippers truly outweigh those of any previously used manual methods. But similar to their inferior competitors, the superiority of these machines will also be subject to the tests of time and comparison to further technological advancements.