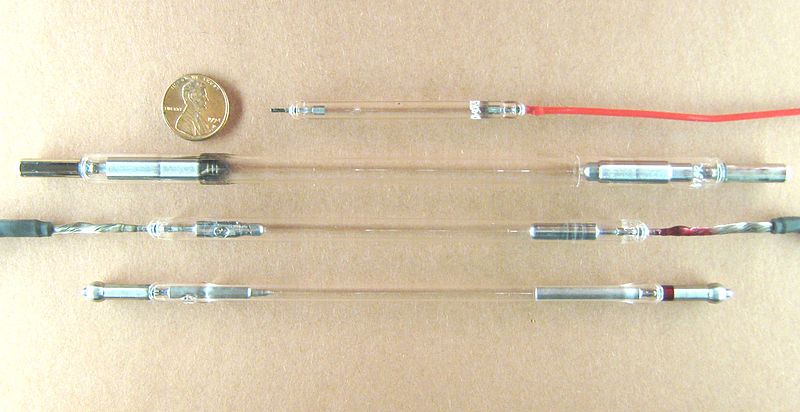
LPSS lasers utilize flash lamp pumping as the act of energy transfer from an external source into the gain medium of a laser. Courtesy of Wikimedia Commons.
Basics of Lamp-Pumped Solid State (LPSS) Lasers
As the trailblazer for many modern day laser designs, LPSS lasers are a mature technology that have been around since the invention of the first laser. The ruby laser, invented in 1960 by Theodore Maiman, employed lamp-pumping as a fundamental operating principle.
Due to their high intensity and brightness at short wavelengths, flash lamps are ideal for optically pumping solid state lasers. Most solid state lasers require pumping to transfer energy into a gain medium. Using this method, the medium absorbs the energy and produces excited states in its atoms. Excited electrons rising and falling energy levels result in the emission of photons, which allows the laser to function. While several different methods of optical pumping exist, one of the most familiar is lamp pumping via arc or flash lamp.
The flash lamp design allows for the production of extremely intense and full-spectrum white light for short periods of time. Flash lamps operate using an electric current discharged through a gas-filled quartz tube, resulting in the generation of hot plasma. The plasma radiates intense light which is then coupled into a laser crystal, thus exciting the laser media. Nd:YAG, a type neodymium-doped crystal, is the most common type of gain medium in LPSS designs.
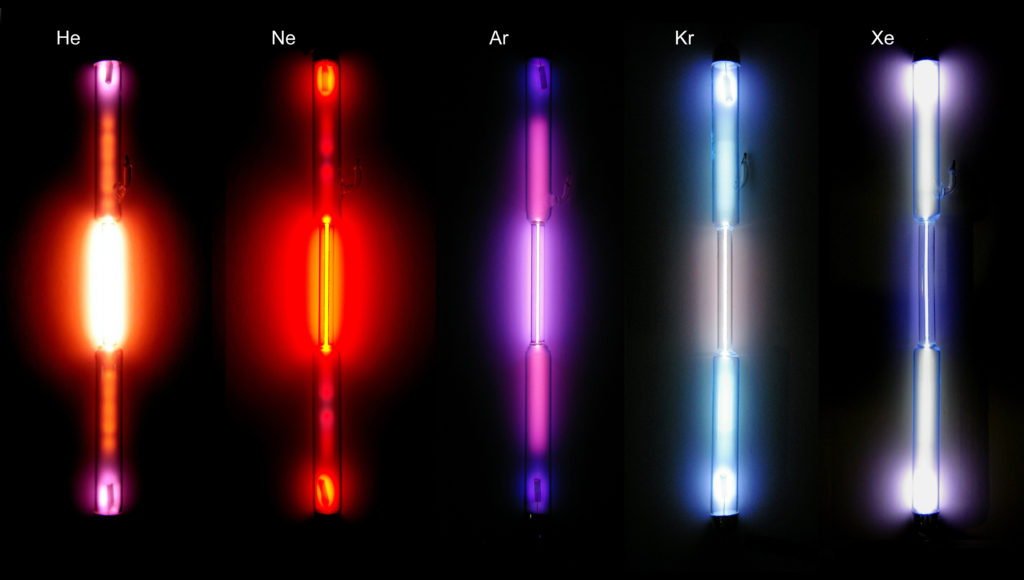
In flash lamps, noble gases are the most efficient at radiating wavelengths that the laser crystal is able to absorb. Courtesy of Wikipedia.
Lamps filled with noble gases, such as Xenon and Krypton, are the most efficient at radiating wavelengths of light that the crystal can absorb. Additionally, they can produce light of high radiant intensities and generate light over a continuous spectrum from ultraviolet to infrared. Flash lamps, operated in pulsed mode, are able to produce microsecond and millisecond duration pulses at high repetition rates.
Advantages Over Other Laser Types
LPSS lasers offer several different advantages over other laser types. As one of the most mature laser technologies, LPSS lasers are robust, inexpensive and well-suited for many different applications.
Additionally, the price per watt of generated pump-power is much lower for lamps than diode pumped solid state (DPSS) lasers, establishing LPSS lasers as one of the most affordable designs on the market. They are relatively inexpensive in terms of initial investment and are generally easier and less costly to repair. In comparison to DPSS lasers, LPSS designs are superior at producing high energy pulses at a lower cost.
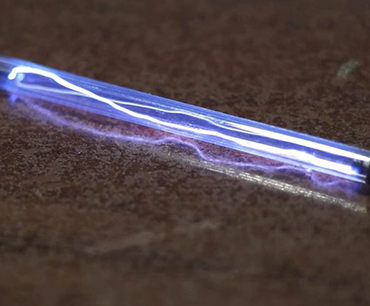
While many consider the LPSS laser an older technology, it still provides several advantages over competing designs. Courtesy of Scantech Laser.
Thanks to their high brightness, high power capability, and low cost per hour of operation, LPSS lasers find many different applications, specifically in industry and manufacturing. They are ideal for applications that demand high power, such as deep marking or engraving. LPSS designs are one of the oldest laser technologies, and despite their age, are still preferred for many industrial applications. Their immunity to voltage and current spikes make LPSS lasers a robust and rugged option for the consumer. Additionally, their low cost of repair and availability make them highly applicable in remote locations where more developed technology is not yet feasible.
Applications of LPSS Lasers
As previously stated, LPSS laser systems are especially appropriate for applications demanding higher energies. This is especially helpful in high-precision applications in industrial, medical, and research fields.
In general, LPSS lasers are capable of producing very high peak power pulses. This makes LPSS lasers an excellent option for applications involving metals and is useful for operations like marking, drilling, and spot welding. Overall, LPSS lasers offer an increased output power, fast performance, and extremely high efficiency to achieve consistent and excellent quality results.
Due to their high intensity and brightness, LPSS lasers are also ideal for medical applications such as ophthalmic laser surgical procedures, dental procedures, gall stone removal, and a variety of aesthetic procedures. The gain medium used determines the output wavelength, thus defining the absorption behavior and light penetration depth into various materials.
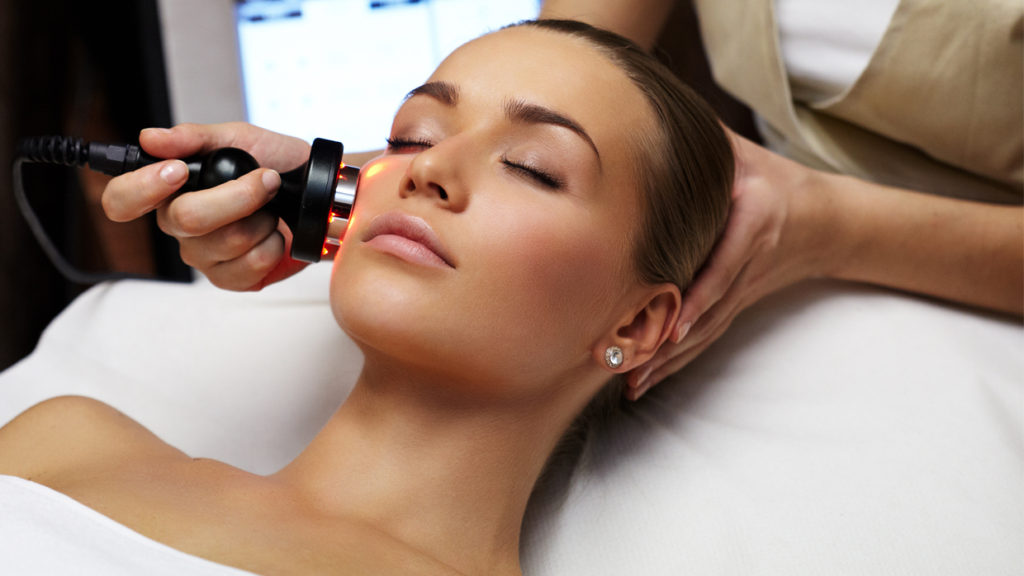
LPSS lasers find several applications in skin care and related fields. Courtesy of Revive Medical Spa.
The Er:YAG laser, which utilizes Erbium as it’s gain medium, harnesses lamp-pumping technology to achieve a 2940nm wavelength laser output. This wavelength has strong water absorption properties and is ideal for applications requiring higher water selective absorption, like skin care. For example, laser skin resurfacing treatments utilize Er: YAG lasers to reduce wrinkles, scars, and blemishes.
Additionally, LPSS lasers consistently find application throughout many fields of research like imaging, holography, remote sensing, and more. One of the most impressive uses of the LPSS laser is in the research area of Light Detection and Ranging (LIDAR), a detection system operating on the principles of radar, but using light from a laser. LIDAR is extremely useful in data collection regarding agriculture, mapping, oil and gas exploration, astronomy, and many more. Indirectly, the doors opened by LPSS lasers have propelled advancements and discoveries that benefit society as a whole.
Future of LPSS Lasers
Although LPSS lasers are still used today, technological advancement in competing laser designs has caused the market share of these lasers to decline. While the LPSS design is robust and relatively easy to use, characteristics like poor beam quality and limited lifetime have prevented LPSS lasers from advancing alongside high-tech industries.
Many applications are phasing out the LPSS laser for the higher beam quality and compactness offered by the DPSS laser. The DPSS laser shares many advantages of the LPSS laser, while in addition exhibiting high wall-plug efficiency and long lifetime. New welding applications are phasing out LPSS lasers and transitioning to diode-based laser systems. Additionally, existing military applications primarily use laser diodes now as well. Today, higher performance LIDAR and range-finding technologies employ DPSS lasers, whereas LPSS lasers are now on their way out.
However, not all is lost as LPSS lasers will still remain in the market and in certain applications indefinitely, particularly those demanding high peak power. Many medical lasers and industrial cutting and marking still require the peak output power provided by the LPSS design. One example is in the laser aesthetic market. Experts project the global laser aesthetic market to reach USD 1,132.7 Million by 2021 from USD 697.6 Million in 2016. Given the demand for aesthetic treatments, these lasers will continue to be relevant in a variety of fields. Furthermore, they will remain in demand for end users who require the familiar technology and accessibility of the LPSS design.
You may want to change attribution of the Ruby Laser to Theodore (TED) Maiman, not Thomas. Otherwise, nice article.
Done, thank you, Doug!