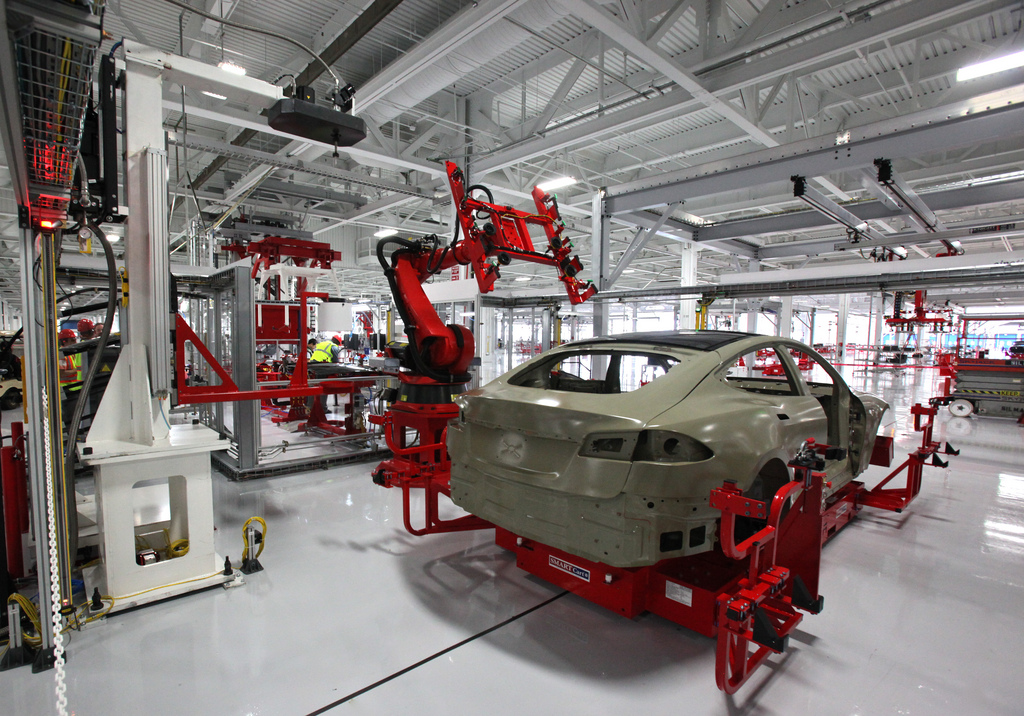
Pictured above are robotic assembly tools being used in a Tesla manufacturing plant. Automobiles are on of the first products to experience the benefits of automated assembly. Metrology is what allows robotic arms to gauge distance from the vehicle. Photo courtesy of Steve Jurvetson via Flickr.
The manufacturing industry has come a long way from Ford’s car plants that spurred innovation in the U.S. The assembly line was a revolutionary tactic for efficiency, but modern manufacturing is much more complex. The modern factory often requires more precision than human hands or eyes are capable of. Metrology is the next step to standardize production, and reduce defects in these complicated parts.
Factories in 2018 are building Internet of Things (IoT) appliances, cars with sensors and onboard computing, as well as nanoscopic electronics like semiconductors. To produce highly intricate parts, manufacturers use dimensional metrology.
Metrology is broadly defined as the science of measurement. Dimensional metrology is more specifically the science of using equipment to quantify measurements (dimensions) of a surface. Measuring machines and 3D vision cameras allow factory machines to take precise measurements and quantify them. This allows human operators to produce a greater range of complex products, and in many cases allows robotic manufacturing tools to produce them automatically.
Connectivity and data collection are permeating most modern industries, and manufacturing is no different. Advanced optics in new metrology tools and techniques are intersecting with fiber optic connectivity to change the business model of manufacturers. This linkage creates a “smart factory” in which the tools for each step of the assembly process collect data along the way.
Dimensional metrology tools and their applications
Coordinate measuring machines (CMMs) are metrology devices that measure an object’s exact geometry and proportions. They use either a mechanical or optical probe to sense points the surface of the object. On their own, CMMs are manually operated using a controller. They are suspended above assembly lines, or on the ground floor in the form of a mechanical arm.
Earlier tools were primarily used for quality inspection post-production, whereas new tools are being used in the assembly line. With better connectivity, computing and software tools, metrology users are identifying defects in earlier development stages to prevent failure. These improvements come in the form of optical digitizers and scanners (ODS) that are being used in conjunction with CMMs to enhance their measurements. ODS use laser or white light scanning depending on their applications.
3D laser scanners are a commonly used ODS with both fixed and portable CMMs, as well as on their own. Laser scanners can measure much more finely detailed surfaces and make wider ranged measurements than a standalone CMM. This makes ODS a go to tool for measuring complex, hard to reach parts like pipes. ODS are especially helpful for non-destructive applications, in other words, for parts that are too fragile to be measured with a mechanical probe.
The introduction of ODS can potentially phase out the need for other metrology tools (like the form measuring machine) in the design process. At one time, FMMs were vital in perfecting aerospace, automotive, electronic, and medical devices. However, the linkage of ODS and CMM can perform many of the same measurements. Designers can easily produce 3D models of their product and use a variety of computer aided design tools. This means a fully digital inspection process, much quicker than manual.
Robotic guidance in manufacturing
Metrology researchers hope to use laser and white light scanners to fully automate the metrology and manufacturing process. In-line CMMs already penetrate the automobile and consumer electronics assembly process to handle convoluted parts. This makes ODS the most cost-efficient step for factories when it comes time to upgrade their aging CMMs. However, most producers are waiting for costs of installation to come down, and ODS to become more portable.
Aerospace, electronics and automobile manufacturing are all industries that are in dire need of more efficient robotic guidance solutions. They have labor intensive processes that require expensive equipment and workers. In these spaces, machines must identify and repair tiny defects as early as possible, since they can result in catastrophic failure. In line metrology is the best solution to create a standardized production process that limits defects and optimizes assembly time.
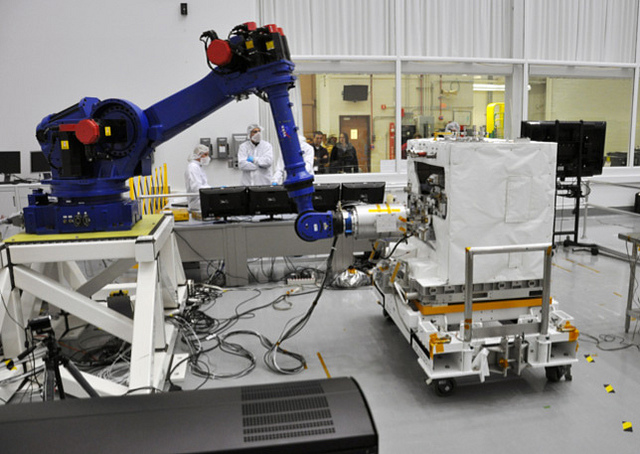
Pictured is one of the many different robotic arms that are used for in-line manufacturing. This one is designed for aerospace applications. Robotic arms like these are typically a combination of a CMM, along with some form of ODS like a laser scanner, or 3D vision camera. Photo courtesy of NASA Goddard Space Flight Center via Flickr.
As equipment producers more efficiently integrate portable scanners and machine vision cameras into factory arms they will need progressively less human guidance. This is the factor that is driving ODS development and integration with robotics. ODS outfitted tools need a precise cycle time to measure and store data on the assembly line, where fast paced production occurs.
Rise of the smart factory
The final goal of equipment manufacturers in these spaces is to make an end-to-end product to be used in factories. One where distributed fiber optic sensors track and collect data to relay to an overarching software suite that connects the entire factory. It is the interconnection of IoT, Cloud services, robotics and advanced optics that provide a perfect storm for optimized manufacturing. This system is referred to as the smart factory.
Dimensional metrology and the concept of a smart factory may seem far removed from each other at first. However, metrology’s applications have moved past simple design or quality control, and on to collect data about assembly. Connecting each assembly process would not be possible without optic sensors and their handiness in transferring data. Enhancements from ODS have forever changed the way metrology is used in manufacturing, because of the opportunities created by data collection.
Focus will soon shift towards optimizing these factories with data analysis. Existing metrology scanners will be able to model defects and identify the criteria for these problems quicker. As defect studies become more developed, equipment makers will be able to offer both their software, and the insights that it produces as a service.
Roughly 80% of the automobile manufacturing process will be automated by 2025. This fact stirs up plenty of controversy due to its effects on employment. However, given the complexity and volume modern parts are produced at, it is not feasible to use human production in many cases. An economy’s transition from manufacturing to services is a hallmark of development, and will not be stopped any time soon.
Nice Post! thanks for the info and can you share some details in quality control