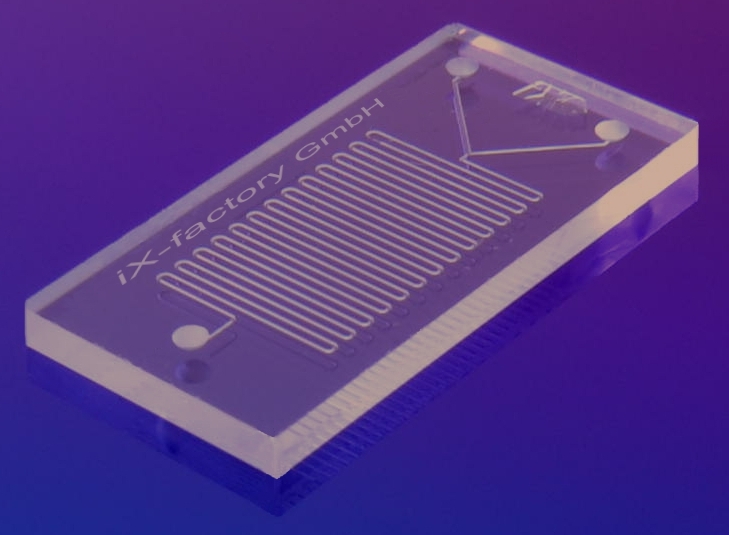
Microfluidic devices are small devices used to observe the properties of fluids at a micro-level. The image above shows a microfluidic chip, one example of a microfluidic device. Image courtesy of Wikimedia Commons.
Microfluidics is the field of science and engineering that involves itself with fluids at a sub-millimeter scale. Many biological, chemical, and physical processes either occur or can be simulated at such a small scale. Microfluidic devices, therefore, are tools that analyze, manipulate, and study these fluids and their behaviors. Currently, manufacturing microfluidic devices from a glass substrate is a time-consuming and complicated process, involving the use of multiple techniques and tools. Therefore, a team from Herriot-Watt University in Edinburgh devised a glass substrate microfluidic device manufacturing technique involving the use of laser-processing. Their process drastically cut down the time of manufacturing, and with further modifications, could efficiently be used in the industrial and scientific fields.
Why use Laser-Manufacturing?
Laser manufacturing and processing have, in recent years, completely changed many manufacturing and processing techniques. A laser is used to modify and shape a specific substrate material. Laser manufacturing is often more precise than traditional mechanisms, as the laser can be controlled very specifically in all 3 axes. Furthermore, one laser can be compatible with multiple types of materials, and the set-up needs little modification between materials or designs. Oftentimes, to modify a laser manufacturing or processing technique, only the wavelength and power of the laser need to be changed. Finally, products processed via the use of a laser often do not need retouching, and are of higher quality than those processed via the use of traditional processing techniques. It can also be noted that laser manufacturing frequently cuts down on time required for manufacturing and finishing a product.
Because of the high levels of specificity required to create the small-scale channels, patterns, and ports used in microfluidic devices, laser manufacturing was identified as an ideal candidate for the processing technique.
Micro-Machining & Micro-Welding
The main tool used throughout the entire laser manufacturing process, as described in the Herriot-Watt University paper, was a 50 watt picosecond laser. Manufacturing was divided into two stages: micro-machining and micro-welding. For micro-machining, the laser had a wavelength of 515 nanometer. The maximum pulse repetition frequency (PRF) was 100 kHz. At this stage, patterns and inlet and outlet ports were generated onto the glass substrates. Channels of different depths were achieved by modifying the laser’s peak fluence, as well as the number of laser passes. Very deep channels were achieved by repeating the laser scan.
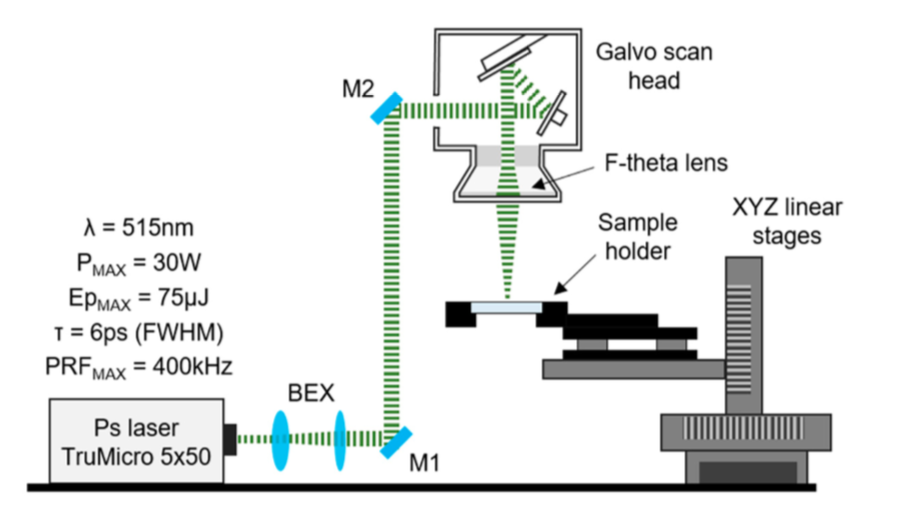
The figure above displays the schematic of the laser device used to micro-machine the glass substrate. Image courtesy of Micromachines.
The laser’s wavelength was set to 1030 nanometers for the second stage, micro-welding. At this stage, the PRF value was 400 kHz. Cleaning the glass plates was necessary prior to the micro-welding, as dust contamination would prevent sufficient optical contact. After the two glass plates were cleaned in a hydrofluoric acid bath, a force was applied to achieve optical contact. The laser beam was focused 80 micrometers below the glass-glass interface. This positioning generated a weld seam across the interface. Weld seams were achieved via multi-photon absorption and plasma generation. As the plasma expands, glass in the area would melt and fill in the gap between the two plates. Upon cooling, this melted glass solidified to form the weld. This was effective for any gaps smaller than 3 micrometers.
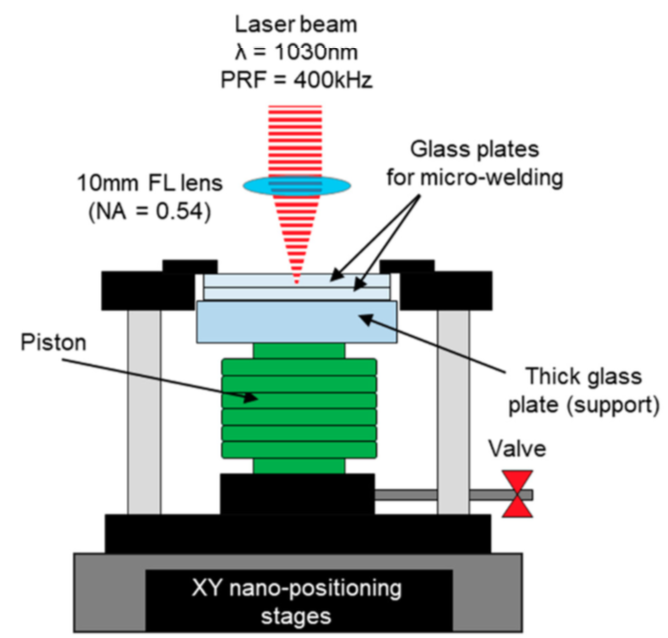
The above figure displays the laser schematic for the micro-welding of the glass plates. Image courtesy of Micromachines.
Testing the Devices
Following manufacturing using the process detailed above, the microfluidic devices were tested for their viability as devices in the industrial and scientific fields. The welds formed via micro-welding had to be tested for their capabilities in limiting fluid flow. First, air was used to fill the microfluidic channels. Next, deionized water was allowed to flow through the device, while observations would be made on potential water leakage. Finally, nitrogen was added to remove the water in the device.
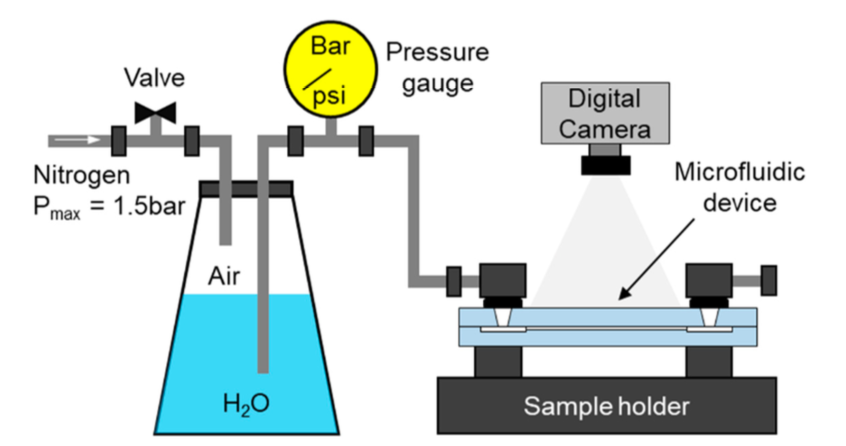
The figure above displays the set-up of the technique used to test the microfluidic devices following laser manufacturing. Image courtesy of Micromachines.
Results and Conclusion
The entire manufacturing time was 2 hours, which is far less time than required in traditional manufacturing of microfluidic devices. Testing of the device revealed no areas of water leakage, indicating that the welds held strong. Additionally, injections of the nitrogen at various high pressures did not cause damage to the device or to the channels. However, injections of water at high pressures greater than 1.5 bar did cause minute deformations to the glass, and not all the water was capable of being dispelled by the nitrogen injections. Future possibilities explored by the authors to improve their manufactured devices was to use stronger and stiffer glass, applying an external pressure to the device to compensate for the internal pressure, and creating additional weld regions. All three of these fixes would potentially increase manufacturing time.
The authors concluded that laser-manufacturing was an efficient technique to use for the rapid manufacture of enclosed microfluidic devices. It was effective in creating the nano-pores and channels necessary to test and observe fluids at the micro-scale. The micro-welding process, in particular, was ideal to close gaps in between glass plates and to confine fluid flow to the manufactured channels. It is a far superior technique than the currently used techniques of anodic and thermal bonding.
Following a few modifications and testing of different materials, a laser manufacturing process could easily be used in the scientific and industrial fields for the manufacture of microfluidic devices.
To read more about this novel process, the paper detailing the Herriot-Watt University’s team’s findings can be read here.
That’s cool to see that it took far less time to manufacture microfluidic devices using micro-machining than when using tradition methods. This would be good for businesses that need to get their products out quickly since they could produce more in less time. It would be good for a business to find a service that can do this process and hire them to make their products since they’ll know how to work the machine to make the process even faster. https://laserod.com/
I agree Hazel, as this becomes more and more mainstream – the speed of production will become a central focus in manufacturing environment. I see that your company is in the business too. Please feel free to sign up as a supplier on our marketplace website and promote your products/services: https://www.findlight.net/register
Microfluidics is a branch of science that deals with the manipulation and controlling of micro fluids. Micro fluids are fluids which range from something as small as tens to even something even smaller as hundreds of millimeters in length. The microfluidics devices used in this technique are made of glass, silicon or polymer.
Read more @ https://www.marketindustryreports.com/microfluidics-market/15