Introduction
In precision engineering, motorized linear stages have become an indispensable tool for controlling the movement of objects with a high degree of accuracy and repeatability. These stages provide precise and controlled linear motion in a variety of applications, from semiconductor manufacturing to biomedical research. They are designed to move loads along a linear, single axis, path with sub-micron accuracy and can be integrated with different types of motors, such as stepper or servo, to provide the required motion profile. Motorized linear stages are highly configurable and can be customized to meet specific application requirements, making them a versatile solution for many different industries. In today’s post we will explore the basics of motorized linear stages, including their design, operation, and key features that make them a valuable tool for precision engineering.
Before we move on, this post is sponsored by Zolix Instruments – A designer and manufacturer of scientific instruments and analytical solutions for material science and other applications. You can check out their motorized stages on FindLight here.
The Importance of a Motorized Linear Stage
The motion of typical objects can be characterized by their ability to rotate along three axes, which amounts to six degrees of freedom. The motorized linear stage restricts the load, in this case, an object, to motion along a single axis, effectively reducing its degrees of freedom to one. This restriction is extremely useful in precision engineering applications where it is necessary to control the motion of the object with high accuracy and repeatability.
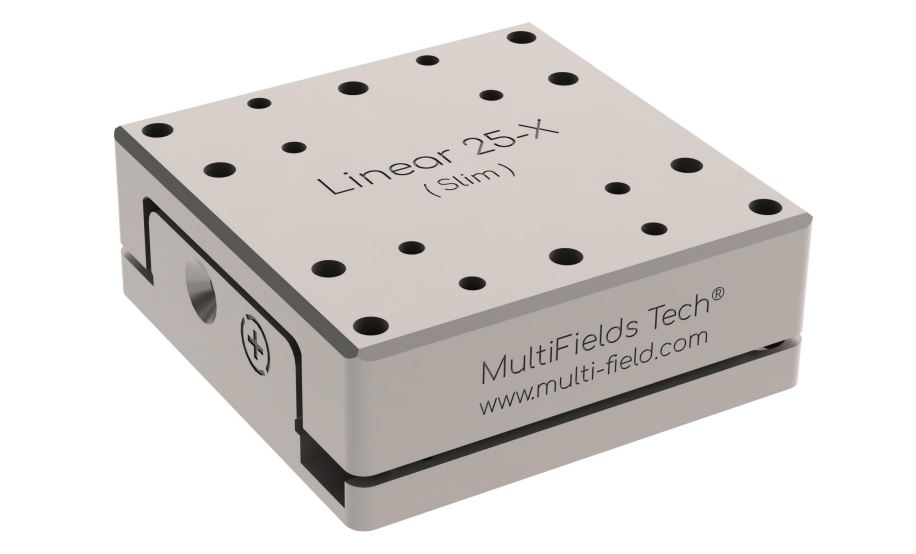
Compact and precise, the Linear 25-x series piezo stage offers exceptional motion performance for nano-positioning applications. Built with non-magnetic materials, it operates flawlessly in ultra-high vacuum and very low-temperature environments.
Motorized linear stages play a crucial role in a variety of industries that require precise and repeatable positioning, making them an essential tool for modern manufacturing processes. For instance, in the semiconductor industry, motorized linear stages are used for the production of semiconductors to precisely position wafers during the manufacturing process. In the biomedical industry, they are used to move specimens under a microscope for analysis or to position samples for high-throughput screening. In the automotive industry, motorized stages are used to position parts during assembly and testing processes. While, in the aerospace industry, they allow accurate positioning in the manufacturing and assembly of aircraft components.
Internal Components and Mechanisms
Motorized linear stages are constructed with several internal components and mechanisms that work together to achieve accurate and precise linear motion. The most important of these components would be the linear bearing system, which allows for the load to move along a linear path. These bearings can be made of various materials, such as steel or ceramic, and are designed to minimize friction and ensure smooth motion.
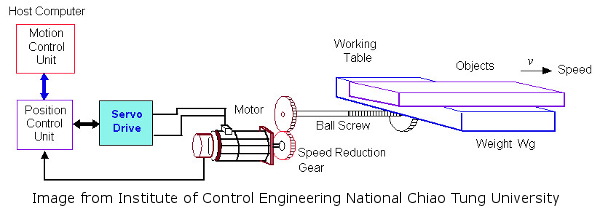
The block-diagram of a motorized linear stage system. Image Courtesy of National Chiao Tung University in Taiwan
The drive mechanism is another critical component that converts rotary motion from the motor into linear motion of the stage. The stage also includes a feedback mechanism, which provides position feedback to the controller to ensure accurate positioning. Additionally, the stage may include a braking mechanism to prevent unwanted motion or provide a locking feature. Overall, these internal components and mechanisms work together to provide precise and reliable linear motion for a wide range of applications. Let’s look into each of these components with more in-depth view below.
1. The Drive of a Motorized Linear Stage
The drive mechanism is a critical component of a motorized linear stage, responsible for converting rotary motion from the motor into linear motion of the stage. There are several types of drive mechanisms used in motorized linear stages, including lead screws, ball screws, and linear motors. Lead screws are the simplest and most cost-effective option, but have limited accuracy and speed capabilities. Ball screws offer higher accuracy and faster speeds than lead screws, but are also more expensive. The choice of drive mechanism depends on the specific application requirements, including the required accuracy, speed, and load capacity of the stage.
The drive mechanism is typically controlled by a servo or stepper motor, which provides precise and repeatable motion control. By choosing the appropriate drive mechanism and motor, motorized linear stages can provide the necessary accuracy and speed for a wide range of applications. Choosing the right servo drive manufacturer is critical for ensuring reliable and efficient performance in your application, whether it’s in industrial automation, robotics, or other precision control systems.
2. Encoders of a Motorized Linear Stage (Feedback Devices)
An encoder is a feedback mechanism that provides position information to the controller. It is made up of a sensor and a scale. The encoder is typically attached to the drive mechanism and provides precise position feedback to ensure accurate positioning of the stage. Encoders can be either linear or rotary, depending on the type of motion being controlled. Linear encoders provide position feedback for linear motion, while rotary encoders provide position feedback for rotational motion. The resolution of the encoder determines the accuracy of the position feedback, with higher resolutions providing greater accuracy.
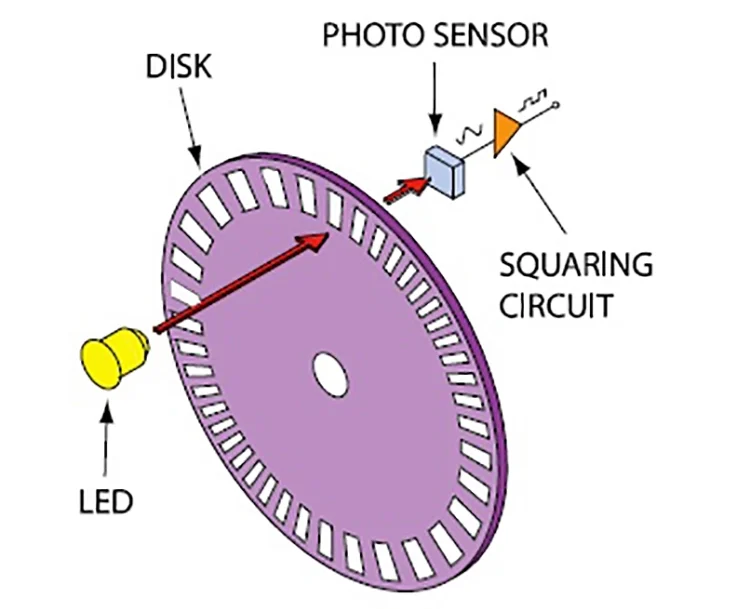
Analog Rotary Encoder. Image Courtesy of Analog IC Tips
Once the sensor generates the electrical signal, it is further processed by the encoder to generate digital or analog signals that represent the position of the load. These signals can then be used to provide digital readouts, such as the position displayed on a digital readout screen, or analog signals that can be used for feedback control of the motorized linear stage.
3. The Controller of a Motorized Stage
The controller is the brain of the motorized linear stage and is responsible for controlling the motion of the stage based on user input and feedback from the encoder. It receives input from the user, such as the desired position or velocity, and uses this information to control the drive mechanism. The controller can be either an open-loop or closed-loop system. In an open-loop system, the controller sends a signal to the drive mechanism based on the user input, without feedback from the encoder. In a closed-loop system, the controller uses feedback from the encoder to adjust the position of the stage and ensure accurate positioning. Closed-loop systems provide higher accuracy and repeatability than open-loop systems, making them the preferred option for precision engineering applications.
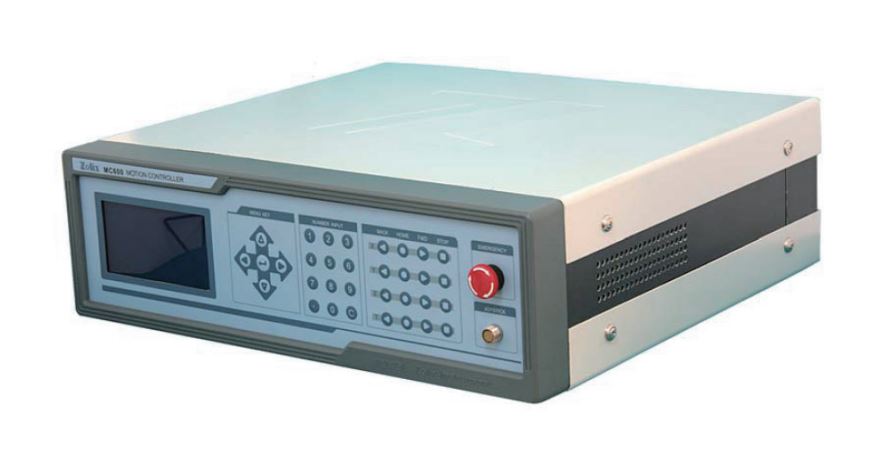
A typical controller for a linear motorized stage. Many Controllers come with multi-axis and various interface protocols (USB, RS-232, etc.) Courtesy of Zolix Instruments as seen on FindLight Marketplace
On the other hand, the controller and the drive mechanism work together to ensure the proper movement of the motorized linear stage. The controller is responsible for converting software commands and system parameters into a control signal for the motor driver or amplifier. It takes feedback signals from the servo motor and/or mechanical stage to ensure accurate positioning and corrects for any errors in intended motion. The controller may also include features such as speed and acceleration control, position presets, and limit switches to prevent over-travel or damage to the stage. The choice of controller and drive mechanism depends on the specific application requirements and desired level of precision and control.
4. Motors
The selection of a motor for a particular application is dependent on various factors such as torque, speed, and precision requirements. For instance, a DC servo motor may be preferred for applications requiring high precision and accuracy, while a stepper motor may be suitable for applications requiring precise positioning and low speeds. Similarly, linear motors may be suitable for high-speed and high-acceleration applications where traditional rotary motors are not suitable. It is essential to understand the specific requirements of the application and choose the appropriate motor accordingly to ensure optimal performance and efficiency.
5. DC Servo Motors
DC servo motors are a popular choice for motorized linear stages, as they offer high precision and accuracy in positioning. They operate using a closed-loop control system that constantly adjusts the motor’s position based on feedback from the encoder. This allows for precise control over the movement of the load and ensures that it reaches the desired position accurately and reliably.
6. Stepper Motors
Stepper motors are another type of motor that can be used for motorized linear stages. They operate using a series of electromagnetic coils that turn the motor shaft in small, precise increments. While stepper motors are less precise than DC servo motors, they are often less expensive and simpler to operate. They are a good choice for applications where high precision is not required, but cost and simplicity are important factors.
7. Linear Motors
Linear motors are a relatively new technology that is gaining popularity in motorized linear stages. Unlike traditional rotary motors, linear motors operate by producing a magnetic field that moves the load along a linear track. This provides smooth, precise motion with high accuracy and repeatability. Linear motors are often used in high-speed applications where traditional motors would not be able to keep up.
Conclusion
In conclusion, motorized linear stages are an essential tool for precision engineering, enabling controlled and precise linear motion in a wide range of applications. Their ability to provide sub-micron accuracy and repeatability makes them indispensable in industries such as semiconductor manufacturing and biomedical research. The design of motorized linear stages includes critical components such as linear bearing systems, drive mechanisms, encoders, and controllers, which work together to achieve accurate and precise linear motion. By understanding the basics of motorized linear stages, including their design, operation, and key features, engineers can select and customize the right stage to meet their specific application requirements.
Quick Links to Motion Control Products on FindLight
Are you in the market for Linear Motorized Stages. If you are, we have a dedicated category with 100+ different models from various suppliers around the world. This might just be the best place to do comparative shopping.
For your convenience we have summarized a few relevant quick links to various motion control products on FindLight here:
Motion Control: The group of categories on various Motion Control Products. Here you can find all the various types of products from Linear and Rotary Stages to individual components.
Manual Stages: Our Manual Stages can be found here. Here you can find both linear and rotary manual stages as well as goniometer and tilt stages.
Z-Jacks: If you are in the market for Z-Jacks or Vertical Manual Stages, you can find them here.
Motorized Stages: Our category on various motorized stages is here, where you can find linear, vacuum-compatible, rotary and vertical motorized stages.
Motors and Actuators: You can find a large selection of Linear Actuators, Stepper Motors, Piezo Actuators and Brushless Motors in this category.
External Sources on Motorized Linear Stages
https://www.griffinmotion.com/the-importance-of-a-linear-stage-in-a-precise-motion-system/