Introduction and motivation
Additive manufacturing (AM) is the method of creating products from digital 3D models by fusing together successive layers of materials. Without the need for additional tooling, this method can produce parts with intricate internal and external geometries. Additionally, AM has demonstrated considerable promise as a manufacturing technology to replace established manufacturing processes including subtractive and joining procedures. In this article, we discuss the effect of selective laser melting (see Figure 1) on the fatigue features of steel (see Figure 2). This article is mainly based on the research carried out by the scientists at Lappeenranta University of Technology in Finland.
Despite its popularity, AM has not yet been fully understood and applied; as a result, traditional subtractive techniques continue to account for the majority of the industrial market globally. On the one hand, AM has a number of benefits over its subtractive rivals. For instance, AM is typically a straightforward one-step process. Although it has a high specific energy consumption index (the amount of energy used in the manufacture of a material unit), it benefits sustainability by shortening supply chains, lowering material wastes, and improving part geometries. On the other hand, it has a number of drawbacks, such as issues with regulating the characteristics of its end product and tolerances. To get around these restrictions, there are some options. The majority of these ideas is still in their infancy and requires more research to advance.
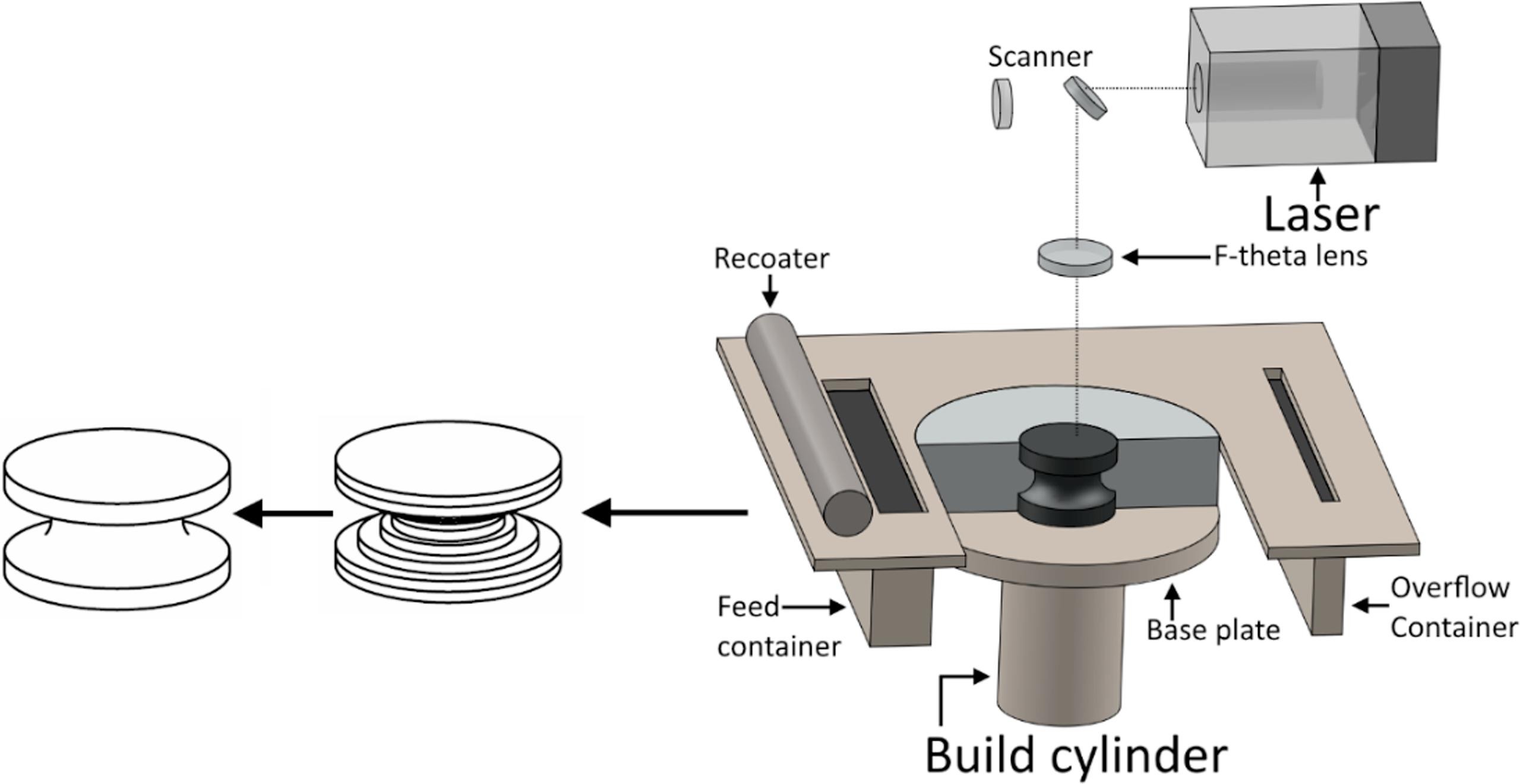
Figure 1: Schematic diagram for the technique of selective laser melting; Image courtesy of Elsevier
Microstructure of products and selective laser melting
Since the quality of AM’s final products are influenced by their processing history and multiple production parameters, further research is still needed to recognize its full potential as a manufacturing technique. Therefore, one of the important areas of research in this field is the development of models to relate the microstructure, characteristics, and performance of the finished products.
The creation of new powders and the enhancement of their quality are two additional intriguing aspects of AM. One of the top focuses of AM studies is creating a data collection of mechanical characteristics for materials made using additive manufacturing. The best properties of AM parts can be produced more easily thanks to this data bank. AM methods can be broken down into a number of different categories depending on the manufacturing process and the energy source used. Powder feed, wire feed, and powder bed systems are the three main groupings.
Directed energy deposition techniques, commonly known as powder and wire feed systems, are appropriate for both manufacturing and maintenance. These methods make it feasible to repair worn-out, outdated pieces by depositing fresh layers of materials on top of them. The majority of the time, powder bed systems can be utilized for production; but, with more restrictions, they can also be taken into consideration for repair and maintenance.
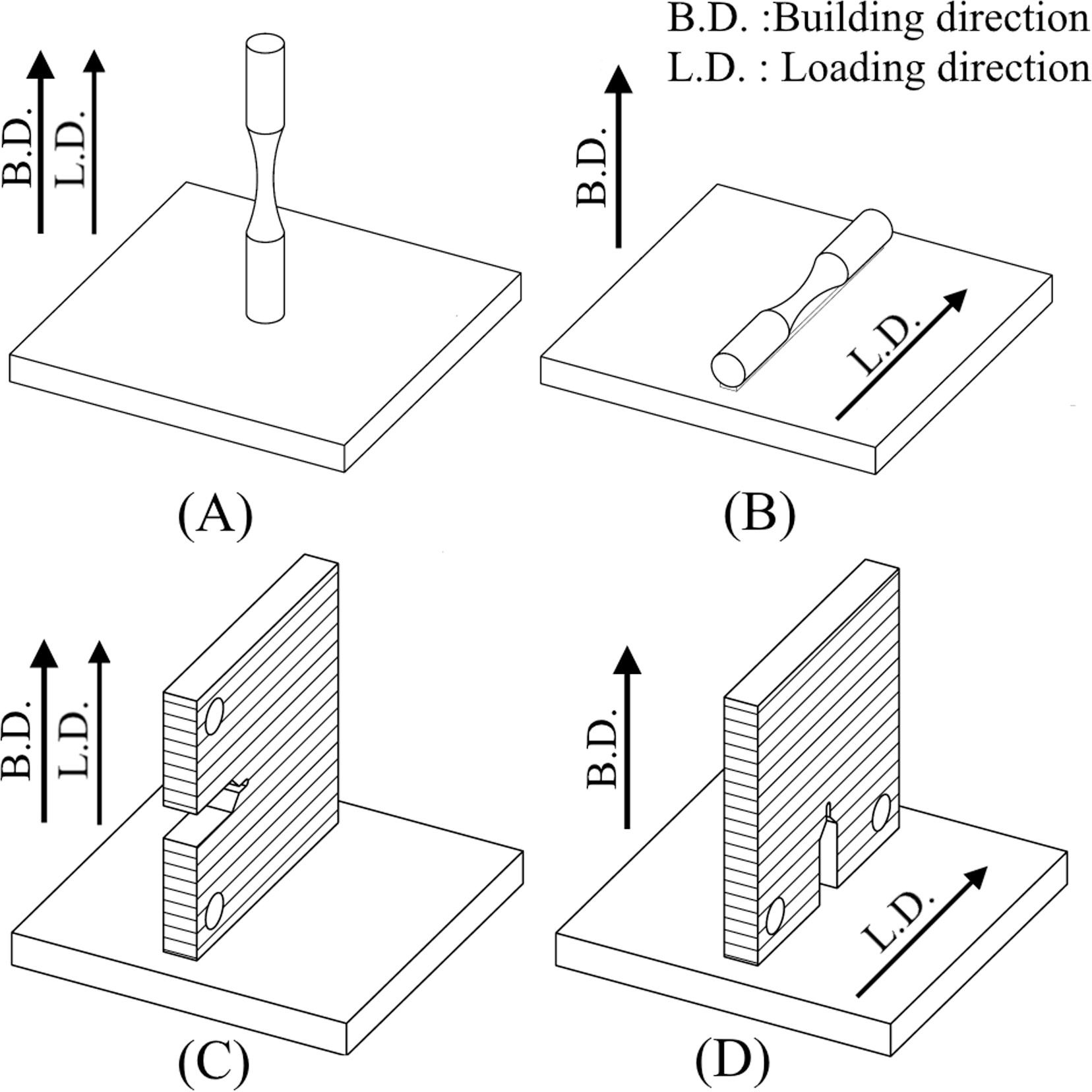
Figure 2: SLM fatigue specimens: (A) vertical fatigue test specimen; (B) horizontal fatigue test specimen; (C) vertical fatigue crack growth specimen; and (D) horizontal fatigue crack growth test specimen; Image courtesy of Elsevier
Selective laser sintering and selective laser melting
The most widely used methods for metal additive manufacturing are powder bed systems, which include selective laser sintering (SLS) and selective laser melting (SLM). On the one hand, SLS does not always require metallic powders unless it is necessary to create porous products since it uses sintering (solid state diffusion) rather than total melting. SLM, on the other hand, is not as material-limited as SLS because it is based on the entire melt and solidification of powder materials.
In order to minimize time-consuming post-processing steps, SLM is also designed to produce products that are nearly entirely dense and have mechanical properties comparable to those of raw materials. Selective laser melting is a manufacturing technique with its own distinct advantages and disadvantages.
For instance, it can typically produce finished parts without the need for additional processing. To melt the powder material, this technique needs a given amount of heat input and a specified caliber of beam. Repeated melting and solidification cycles can also cause imperfections like porosity (see Figure 3), as well as increased residual stresses and shrinkage in the finished product.
SLM is less constrained in terms of material choices than SLS and can handle metals and alloys with strong weldability. The range of its material choices is still more restricted due to additional metallurgical considerations and challenges brought on by the quick melting and solidification cycles of SLM.
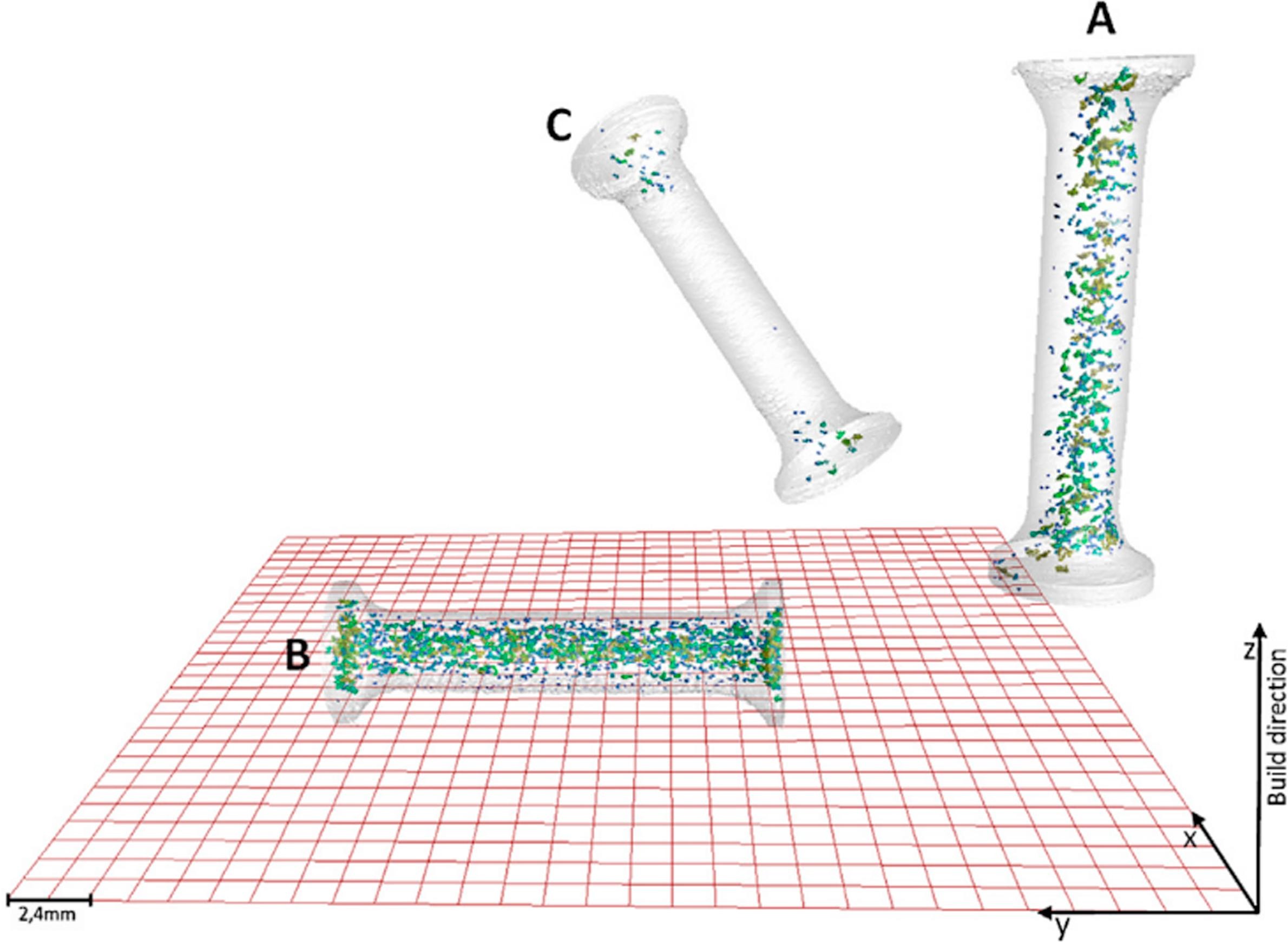
Figure 3: 3D visualization of porosities in samples with different building directions; Image courtesy of Elsevier
Currently, SLM has been used to process a variety of materials successfully, including stainless steel, tool steel, cobalt-chromium alloys, titanium and its alloys, aluminum alloys, nickel alloys, and some precious metals, including pure silver and gold. Steel among these materials offers a wide variety of adaptable qualities to cover a sizable number of applications. Because it provides an excellent balance of high strength, good ductility, affordability, and recycleability, it is frequently utilized in modern industrial and household items.
Construction (such as suspension cables), transportation (such as engine components), energy (such as turbine blades), medicine, and several other industrial appliances are only a few of its applications.
Steel is one of the most used and researched materials in SLM investigations as a result. To distinguish them from the ordinary cast and rolled steels, steels produced by SLM are referred to as SLM steels from now on in this work. Even though a variety of studies have been done on the mechanical characteristics of SLM steels, their fatigue qualities are still not fully understood.
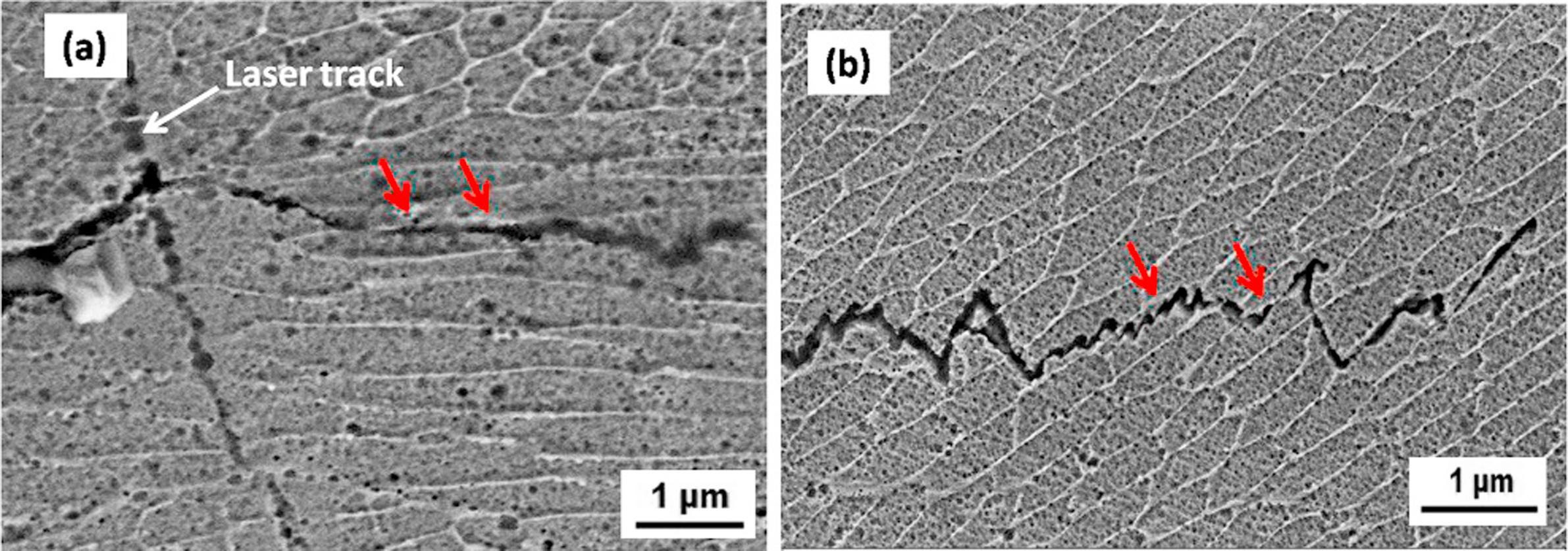
Figure 4: Fatigue crack propagation through the microstructures; Image courtesy of Elsevier
Additionally, SLM steels are frequently utilized in the aerospace, energy, and medical sectors, all of which involve extremely high dynamic loading conditions (applications such as dental implants, mold inserts, and marine propellers). Therefore, from a practical standpoint, the fatigue properties of SLM steels are crucial(see Figure 2 and Figure 4). As a result, the objective of this study is to give the reader a critical overview of the fatigue properties of SLM steels, previous investigations, and existing knowledge gaps.
Selective laser melting method differs from conventional AM methods in three ways: one, it uses a laser beam as its energy source, two, the powder material is entirely melted and solidified, and three, the powder bed fusion method is used (see Figure 1).
Summary and conclusions
SLM steels are subjected to dynamic loading circumstances in a variety of applications; therefore, estimating their fatigue life under such loading situations requires an understanding of their fatigue behavior and properties. However, there isn’t much research in the literature discussing the fatigue properties of SLM steels. Additionally, the existing studies are not set up to be employed in the creation of numerical equations and models that forecast fatigue life.
To understand the fatigue behavior of different SLM steels, thorough and systematic future research is needed. According to recent studies, construction orientation, heat treatment, surface quality, and beam energy density all have an impact on the fatigue life of SLM steels.
Despite all of the work that has gone into finding and studying the fatigue properties of SLM steels, there are still many questions that need to be answered. These include establishing numerical/microstructural models to assess and research the fatigue endurance of SLM steels and offering novel techniques for further enhancing fatigue strength (see Figure 4 and Figure 5).
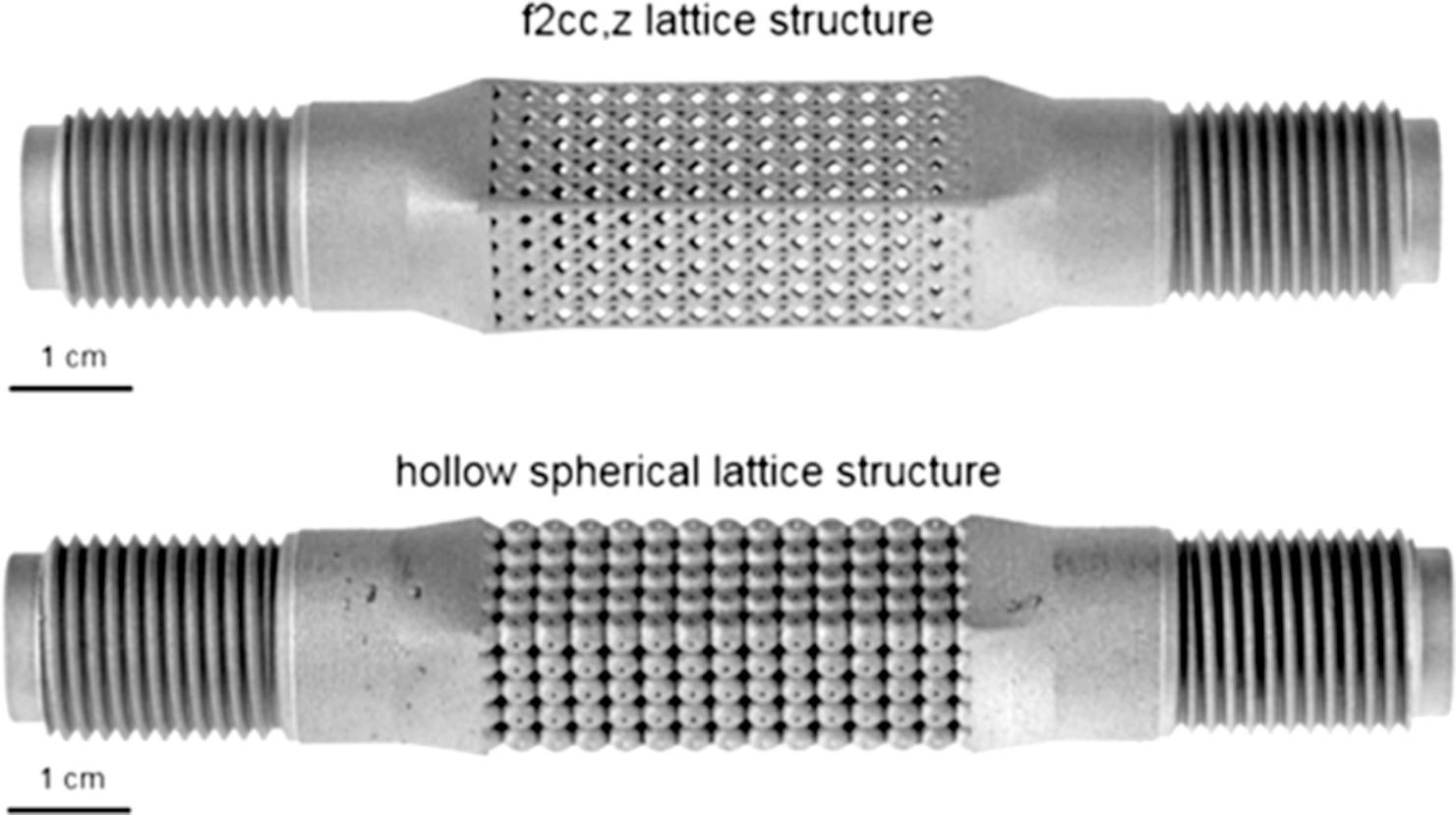
Figure 5: Fatigue specimens with cubic and spherical lattice structure; Image courtesy of Elsevier
This article is brought to you by RPMC Lasers, a distributor of lasers in North America.