Introduction
In this article, we discuss the effect of shaped laser beam profiles on melt thermal flow. This discussion is based on the research conducted by the scientists at University West and Institute for Photonics and Nanotechnologies. Fusion welding is made possible by the employment of laser beam heat sources because they allow for non-contact operation, precision work with tightly concentrated heat input, managing complex joint geometries, and generally quick post-process operation durations. The physics of laser beams and their effects on fusion welding are important. When the power density of the incident laser radiation (i.e., the amount of power per unit volume) is increased, the conduction mode, the transition mode, and the keyhole mode are all consecutively detected. The conduction mode is when the heat transfer almost happens by thermal conduction. The keyhole mode is usually identified by strong vaporization. The transition mode is the transition from the thermal to the keyhole mode.
Description of the transition mode highlights the modest rate of growth of the bead depth-to-width ratio as a result of the moderate metal vaporization that increases with the laser power density. As a result, keyhole and conduction mode properties are combined in the weld seams. The amount of vaporization caused by the conduction mode used in this study is little. It causes a small loss in alloying components that are essential for strong mechanical qualities, and it often results in high process stability with minimal porosity and spatter.
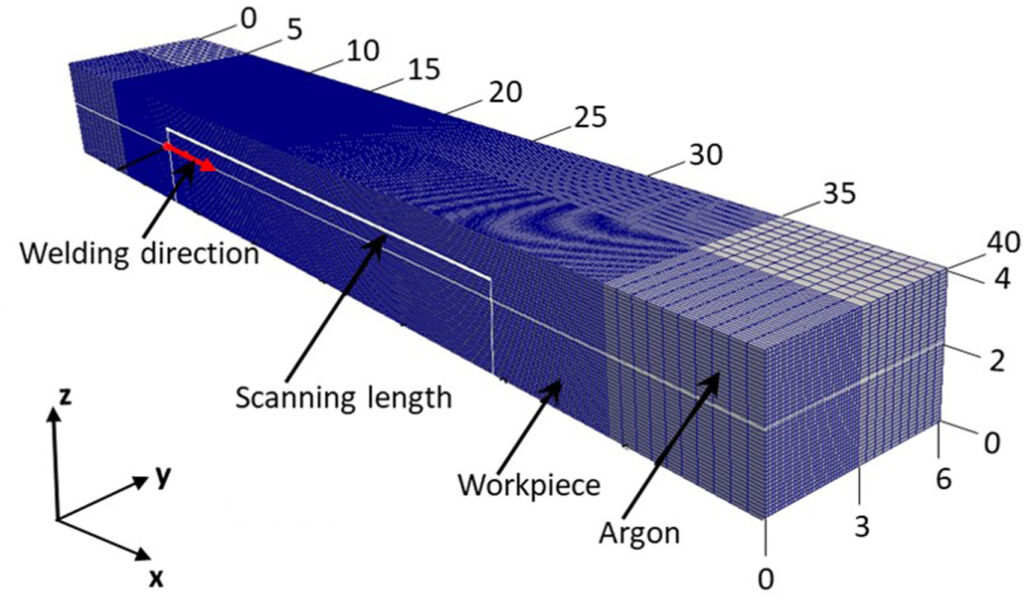
Figure 1: Schematic of a computational domain for laser study. Photo courtesy of Elsevier
There are a few disadvantages to using laser heat sources for welding. The emitted laser point downstream of the fiber is axially symmetric in a section normal to the beam axis. This circular form isn’t always appropriate to achieve the correct seam geometry, as it can lead, for example, to acute toe angles. When a filler wire is fed into a laser beam for welding (or additive manufacturing), the wire frequently obstructs the beam and casts a shadow on a portion of the workpiece in the interaction zone; this shadow effect can cause process instability. Butt joint welding gives an additional example of the disadvantage. The low laser beam width, when combined with robotized manipulation, can result in the creation of weld flaws, which often lack side wall fusion and have insufficient weld strength. One way to study these disadvantages is to use numerical tools (see e.g., Figure 1).
Shaped laser beam and its spot area
By modifying the beam spot area, shape, power density distribution, or any combination of these characteristics, the shaped laser beam can enhance process stability and seam geometry (see Figure 2 and Figure 3). It can be accomplished by tilting the beam to investigate the impact of the beam incidence angle on keyhole-welded butt joints. Defocusing the beam spot can also be done, to examine the impact on the direction of re-crystallization at the free surface of the mushy zone. The range of beam spot power density distributions can be expanded with the aid of beam shaping equipment.
The initial advancements in welding with beam shaping for customizing the weld seam geometry were reviewed. When welding with two- and three-spot beam profiles, researchers created a unique multi-spectral zinc sulfide beam shaping optic to enhance the seam surface in-process. Researchers recently investigated welding using laser beam shaping for customizing microstructures. There are already several beam shaping techniques available, from specialized systems like the multi-spot optic. However, creating profiles that produce the desired results is still a major challenge. Understanding how the form of the beam affects the stability of the welding process and the quality of the welded seam is necessary for this.
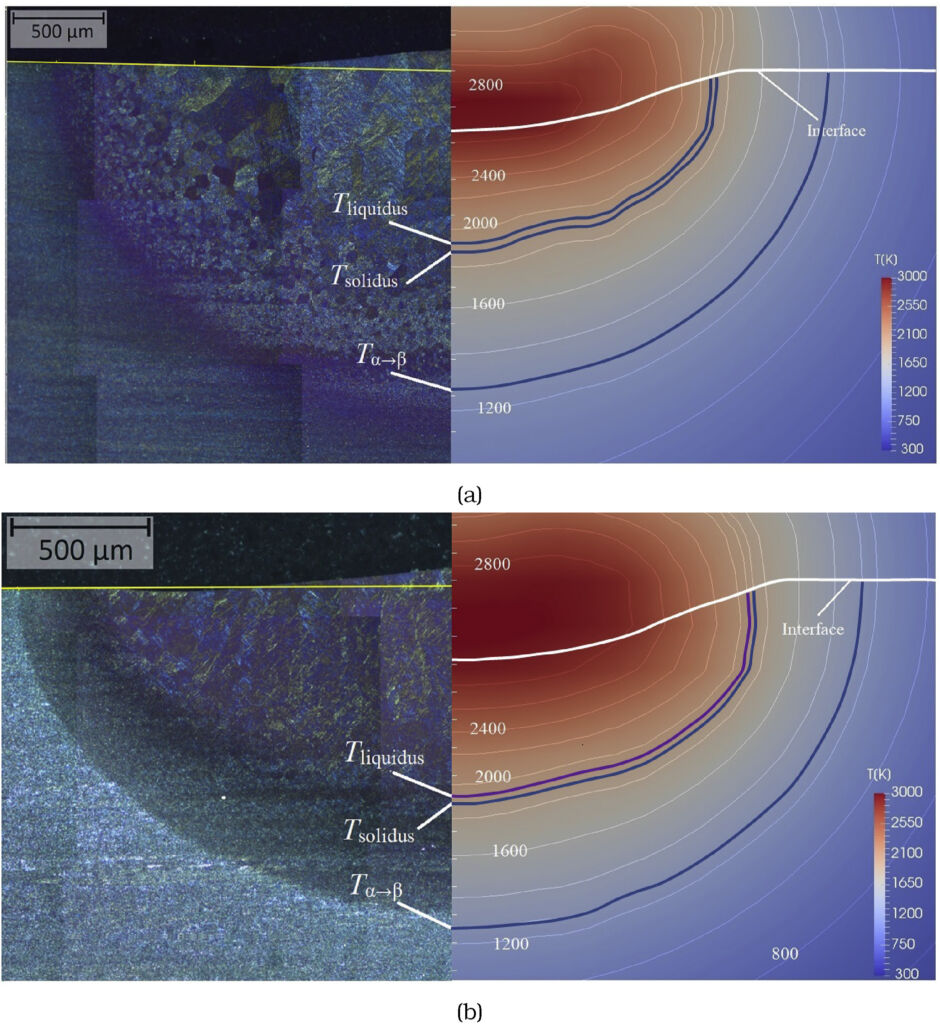
Figure 2: A comparison between the metallographic of the post-solidification melt pool shape (left) and the predicted melt thermal flow pool isotherms (right). Photo courtesy of Elsevier
Researchers recently conducted an experimental study to determine the impact of tilting the processing laser to extend a beam spot shape in various directions. Apart from the orientation, the elongation produced Gaussian-elliptic profiles with a major to minor axis ratio of roughly 1.4. They specifically examined how using the transverse and longitudinal Gaussian-elliptic spot profiles led to increased/decreased seam width and depth that were balanced by one another. The volume of the melt thermal flow pool should remain constant when the spot orientation is changed, they deduced from the energy conservation principle.
Gaussian-elliptic spot profiles for a shaped laser beam
This hypothesis makes the implicit assumption that when transverse and longitudinal Gaussian-elliptic spot profiles are used, the heat convection pattern in the melt pool is similar (apart from being rotated). This assumption needs to be verified because the melt pool volume was not accessible for experimental observation.
Diffractive optical elements (DOE) were utilized to examine the line, aligned point, and ring laser spot profiles. They determined that the rear portion was difficult to predict until using melt pool simulation or experimental observation (see Figure 3 and Figure 4), and they observed a non-linear effect of the beam form on the geometry of the re-solidification front at the melt tail area. The process window can be significantly extended toward a high travel speed thanks to the ring profile, which was created by imposing a non-uniform power density distribution to weaken the thermocapillary flow. The width and total power density of the elongated line and point profiles in the travel direction were identical.
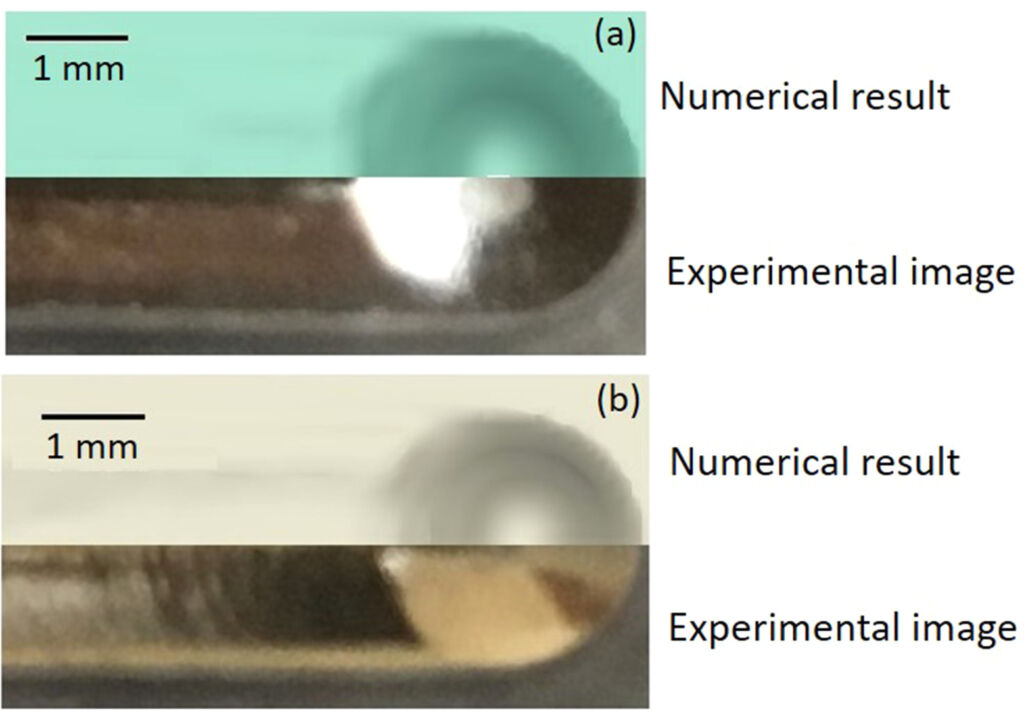
Figure 3: A comparison between numerical study and experiment for a workpiece after solidification. Photo courtesy of Elsevier
However, compared to the points profile, the line profile generated deeper and narrower seam geometry. Scientists explained these variations in bead geometry by claiming that the presence of a significant wave in the line profile encouraged better absorption of the shaped laser beam energy. A wave’s presence suggests that heat convection was possibly also somewhat different for these two profiles. However, in these two cases, the melt thermal flow was not examined.
Future researches for improving numerical simulations
Researchers emphasized that altering the laser beam’s form was a difficult undertaking that was primarily accomplished through experimentation and trial and error. They proposed that it might be backed up by numerical models that might foresee the impact of the beam shaping on the weld. These models would offer data that measurements can’t yet reach, as well as a better knowledge of how processes work, which might cut down on the number of experimental trials.
There is currently a lack of numerical simulation (see Figure 4) to enable beam shape design and optimization. These authors concluded that a heat conduction model was too oversimplified to accurately mimic the geometry of a melt thermal flow pool and assist in shaping a beam. They did predict that one key physical phenomenon that was crucial to describe was the impact of thermal convection on the seam shape. A few researchers employed a thermo-fluid dynamics model more recently to include estimated melt thermal flow pool temperature and surface evaporation pressure to experimental observation.
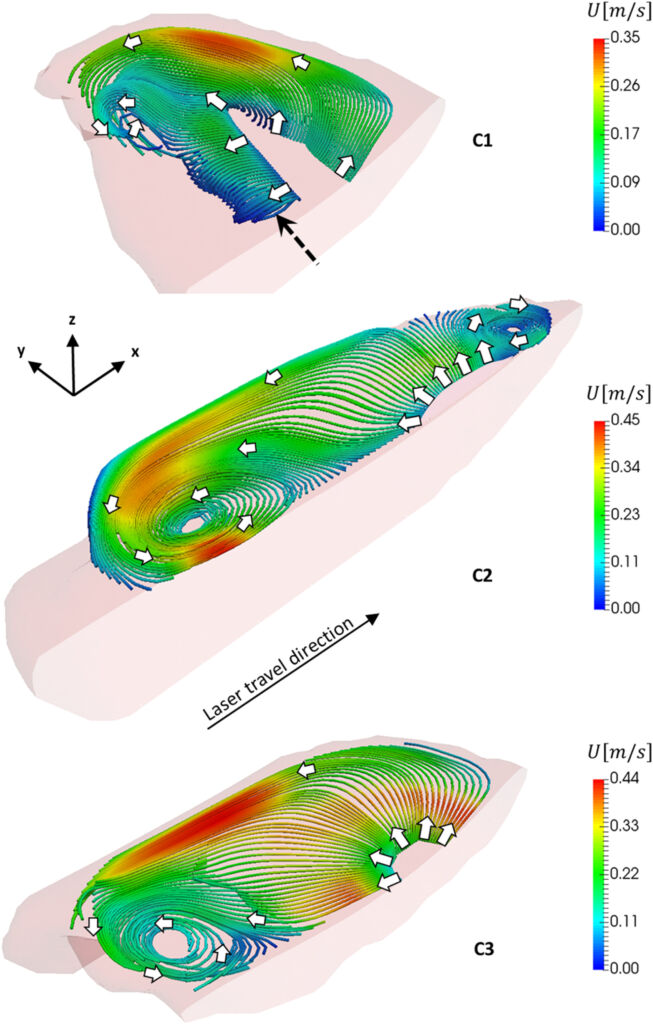
Figure 4: Streamlines in the melt thermal flow pool. Photo courtesy of Elsevier
From the foregoing, it is obvious that there is very little information currently available on the impact of curved laser beam profiles on heat convection through the melt thermal flow dynamic. To be able to develop and optimize beam forms for a particular purpose, it is crucial to have this expertise. Therefore, additional research is required to develop this understanding.