Hybrid steel-and-aluminum structures are essential for creating lightweight components with high rigidity. Due to its higher welding-brazing speed, smaller heating area, and high automation, the laser welding-brazing technique is widely used to fabricate Aluminum-Steel hybrid structures. For instance, the industry is able to obtain an industrial-grade laser welded-brazed Al/steel coach peel junction. Thus, the study of different welding laser beam shapes becomes critical in understanding what creates high quality joints. In this blog post we will explore the effects of single vs dual-beam laser modes on welded joints.
Different welding laser beam shapes and their roles
The typical welding-brazing process is carried out at a speed of 100 mm/s without the use of additional flux. The interfacial intermetallic compound (IMC) and weld formation are crucial to the ultimate mechanical characteristics in the laser welding-brazing of dissimilar metals such as aluminum and steel.
The laser welded-brazed Al/steel butt joint’s tensile strength can be negatively impacted by the discontinuous appearance and shallow undercut at the front surface. The effect of wetting length and wetting angle on the shear strength of a laser welded-brazed Al/steel lapped joint have been extensively studied by researchers. In particular, researchers discovered that larger wetting lengths and smaller wetting angles are advantageous for the enhancement of shear strength.
Configuration of dual laser beams
Most dual alloy welding-brazing applications utilize a single laser beam but dual beam configurations are shown to exhibit certain advantages. Due to relatively large heating area in dual-alloy forming joints, a dual laser beam configuration can enhance the wettability and spreadability of molten filler metal at the brazing interface. For instance, one may compare the wetting durations of molten filler metal produced by single and dual laser beams on welded-brazed Al/steel lap junctions.
Effectiveness of dual laser beams
It turns out, dual laser beams can significantly reduce the extent of produced porosity in the Al/steel junction. Despite using higher laser intensity, the IMC formed in the joint by the cross dual laser beam is thinner than that produced by the in-line dual laser beam. Moreover, the dual beam laser welding-brazing of an aluminum/steel butt joint makes it easier to stamp the resulting joint afterwards.
In this blog post we will look at how different laser beam models – single, cross, and in-line dual – affect the welding-brazing characteristics of an aluminum-steel butt joint. This article is mainly based on the research article by the scientists at Harbin Institute of Technology and Osaka University.
Selected materials for studying welding laser beam shapes
The metals used in their study are sheets of AA6061 aluminum alloy and DP590 dual phase steel. Deep drawing is used to create the non-galvanized DP590 dual phase steel. Aluminum alloy AA6061 is in the T6 condition (Solid Solution Treatment + Artificial Aging). Figure 1 displays the microstructure of the base metals.
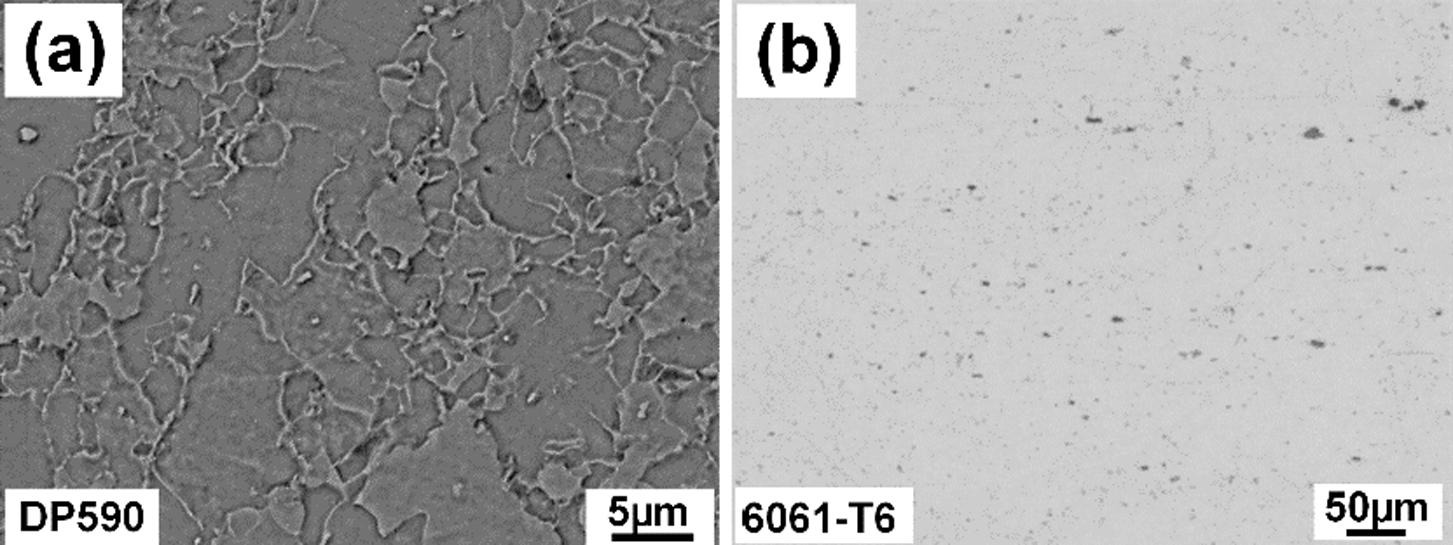
Figure 1: Two selected base metals: (a) DP590 dual phase steel and (b) AA6061–T6 aluminum alloy. Photo courtesy of Elsevier
Experimental setup
Figure 2 shows the experimental setup. A splitting module is fitted in the welding head to divide the single laser beam into the dual laser beam, as shown in Figure 2(b). To assure the stability of the molten pool, the filler wire is fed in front of the welding direction. The top and the rear of the welded-brazed work-piece receive protective gas flow to prevent oxidation of the hardened weld seam. The defocused distance of the laser beam is fixed and it was directed vertically at the work-piece.
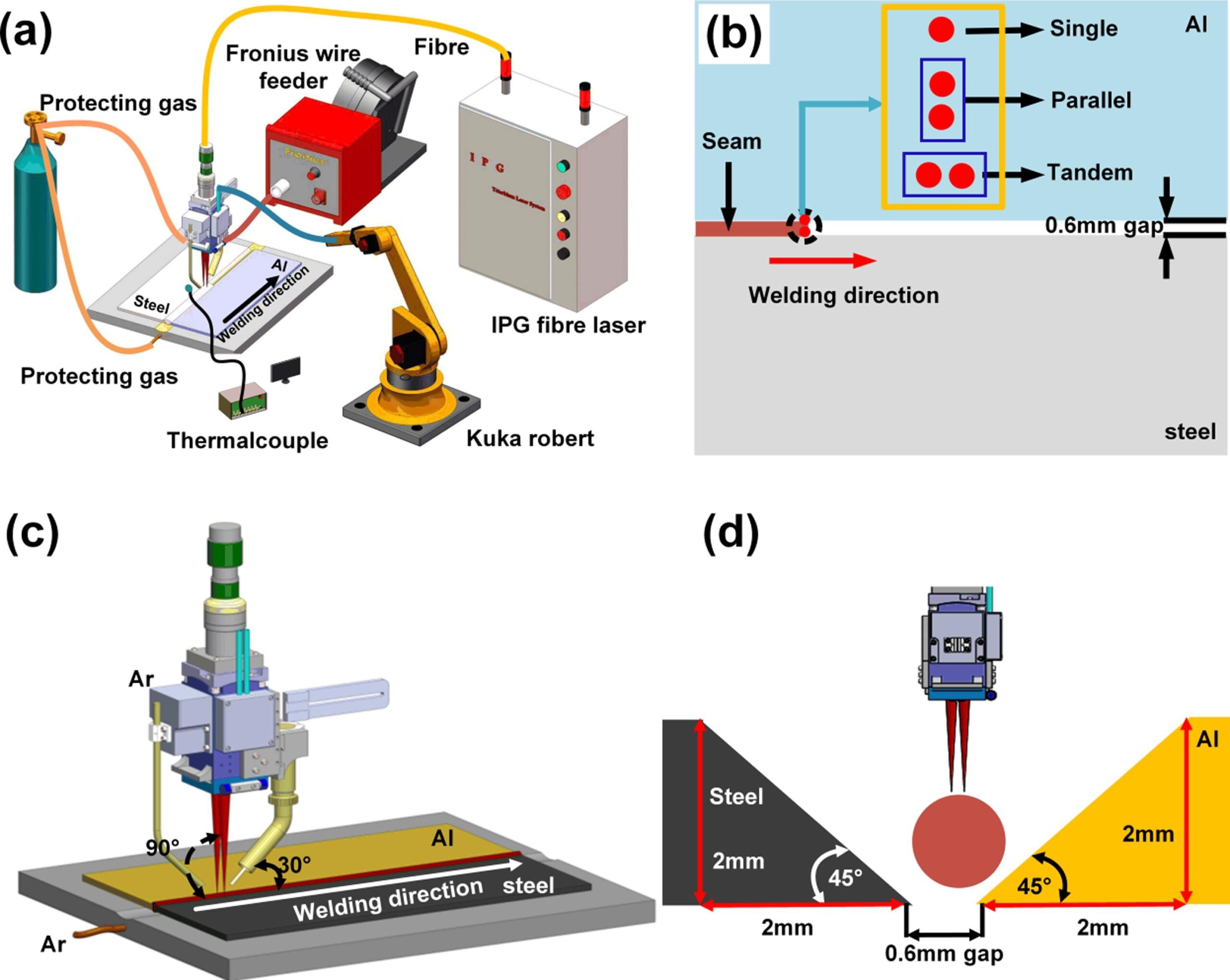
Figure 2: Schematic of the experimental system. Photo courtesy of Elsevier
The defocused laser beam has a diameter of roughly 0.56 mm and a 60° angle with the wire feed nozzle. The distance between the base metals is fixed at 1.0 mm to facilitate the creation of the back weld. Figure 2(c) provides a schematic diagram of the laser welding and brazing process. When the grooves are created, sandpaper is used to polish the grooves to a smooth surface.
Numerical simulations
Using a commercial finite-element program (see Figure 3), the temperature cycles and residual stress along the brazing interface are assessed. In Figure 3, the numerical models are displayed. To reduce the calculation time while maintaining acceptable accuracy, the computational domains are split into the fusion and outer regions, respectively.
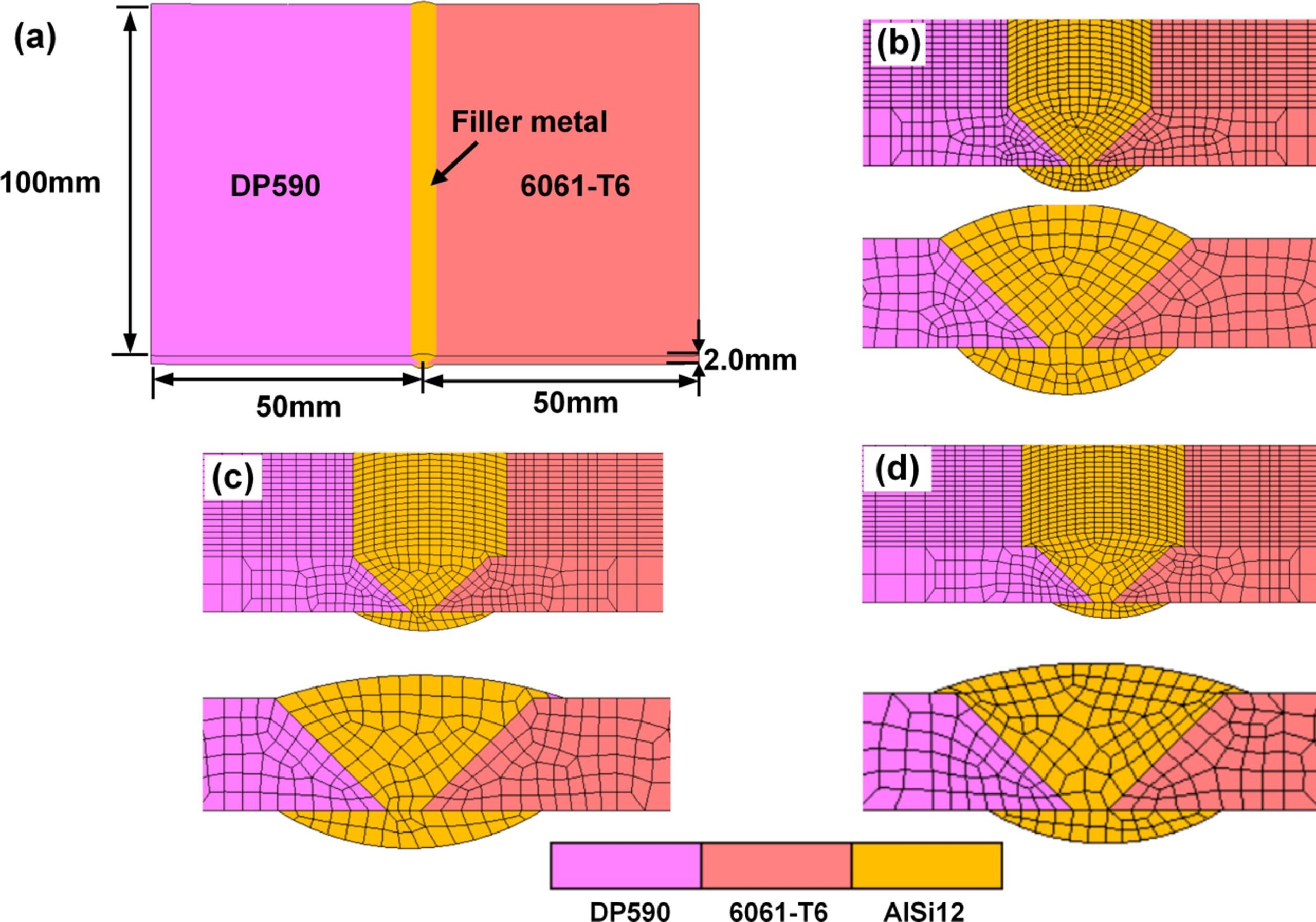
Figure 3: Numerical models for the laser welded–brazed Al/steel joints. Photo courtesy of Elsevier
Results
In this section, we list some important results obtained by the researchers. The weld structures created by various laser beam models are depicted in Figure 4 and Figure 5. These three junctions generated continuous weld-like appearances, as can be seen in Figure 4 and Figure 5. The corresponding cross sections for these three joints were shown in Figure 4 and Figure 5.
Dual beam vs single beam laser welding
When the laser beam model was a single laser, it resulted in poor wettability and spreadability of molten filler along the top surface of steel. Porosity was also discovered in the weld seam. Joints made with in-line and cross dual laser beams resulted in adequate weld forms with good packing of molten filler along the brazing interface.
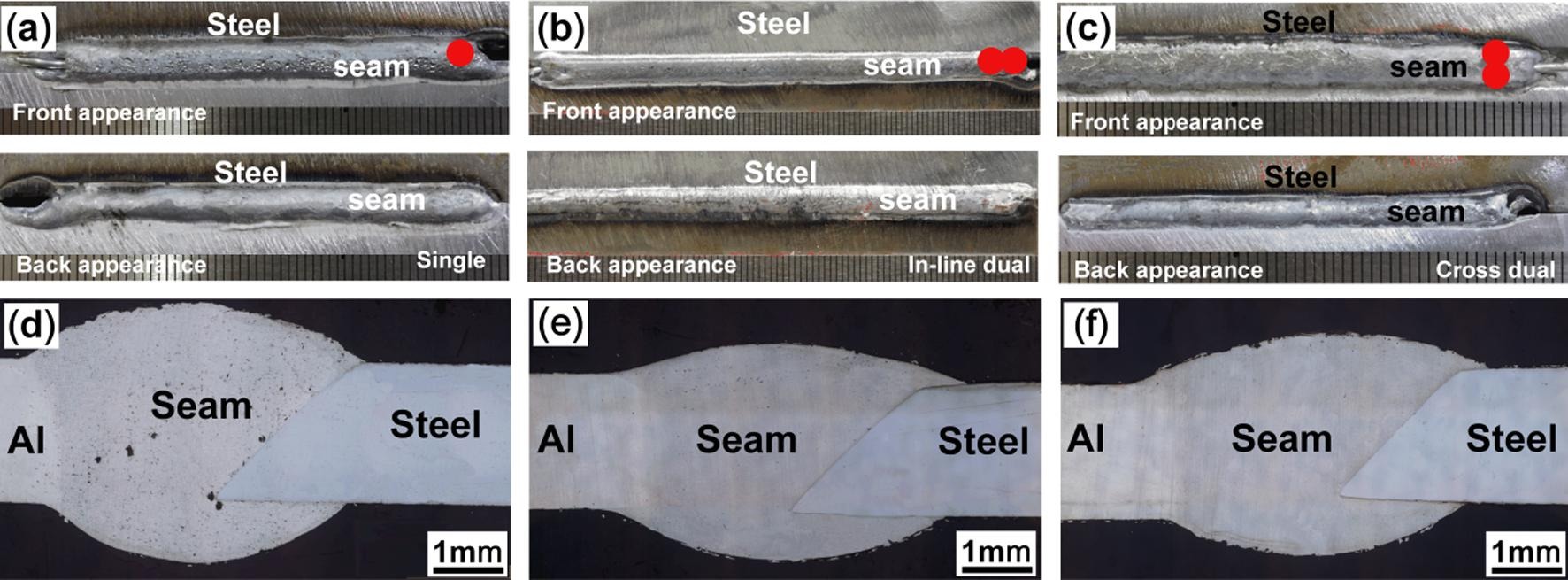
Figure 4: Weld formations of Al/steel joints. Photo courtesy of Elsevier
The extensive melting of Al base metal was the reason why the molten filler for the joint created by a single laser beam had poor wettability and spreadability. Due to the single laser beam model’s smaller heating area than that of in-line and cross dual laser beams, higher peak temperatures would be produced.
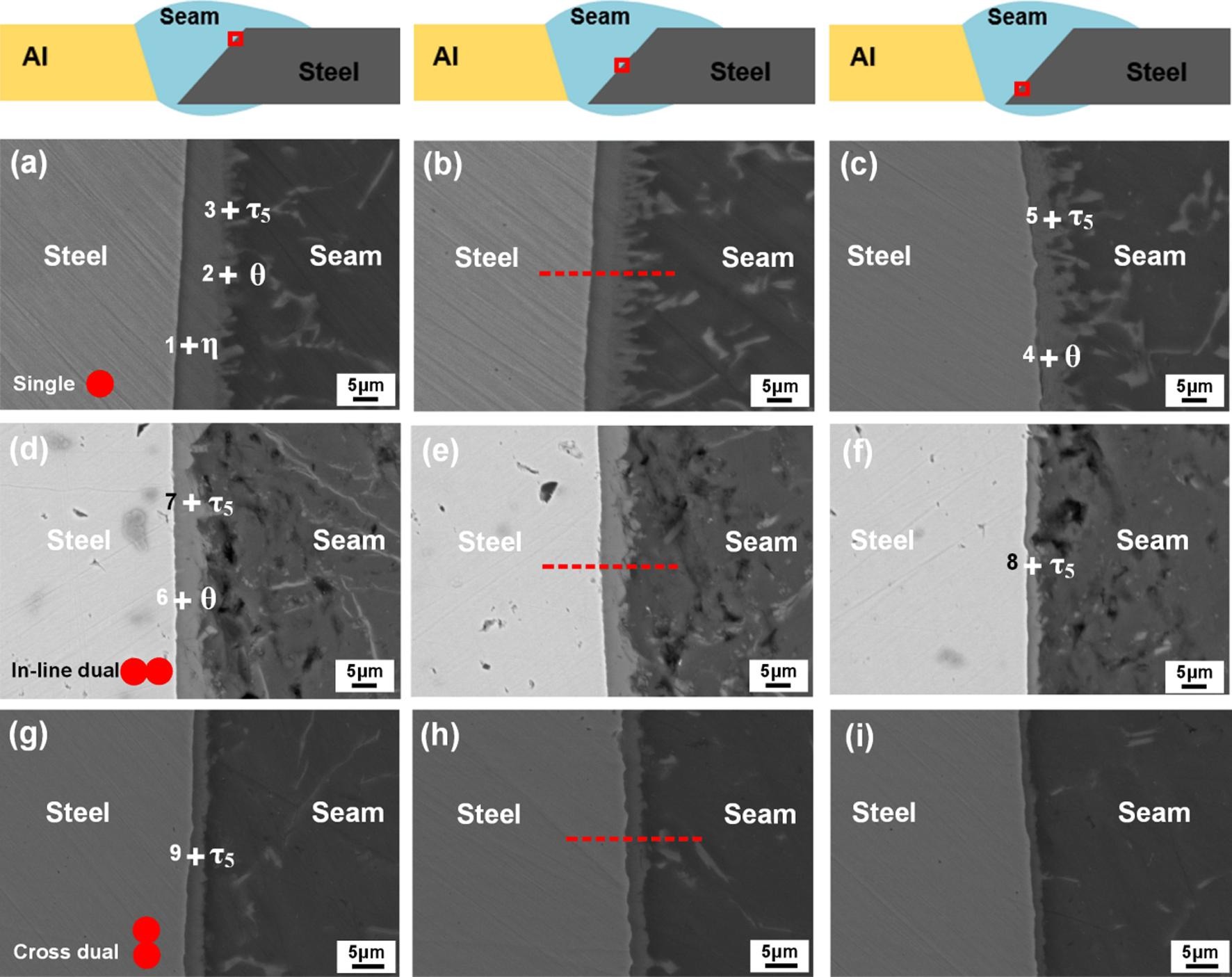
Figure 5: Interfacial microstructure of Al/steel joints. Photo courtesy of Elsevier
Role of wettability
Higher peak temperature caused more aluminum base metal to melt, which ultimately created more room to store the molten filler metals. As a result, additional molten filler metal was used to fill this space, while not enough of it was used to ensure that the steel’s top surface was wettable and spreadable.
Entrapped gas or burning loss of alloying materials were two possible sources of the produced porosity in the weld seam. The molten pool fluctuated greatly during the laser welding and brazing operation, and some gas (air or protective gas) would be added to the molten pool.
Due to the single laser beam model’s restricted degassing capacity, the implicated gas was difficult to remove. Additionally, due to its higher peak temperature in the molten pool, an alloying element with a low boiling point, could evaporate under the single laser beam model.
Temperature and molten pool
The molten pool fluctuated greatly during the laser welding and brazing operation, and some gas (air or protective gas) would be added to the molten pool. Due to the single laser beam model’s restricted degassing capacity, the implicated gas was difficult to remove.
Additionally, due to its higher peak temperature in the molten pool, an alloying element with a low boiling point could evaporate under the single laser beam model. When the welding-brazing process was complete, these trapped gases or evaporated metallic vapor could be caught in the weld seam, which contributed to the creation of porosity.
Solid weld formation with a single laser beam
At the end, they mentioned that that a solid weld formation can also be achieved with a single laser beam. For instance, at a laser power of 2200 W, it is possible to achieve a qualifying weld formation. However, a dual laser beam model required 2500 W of laser power, which was more than a single laser beam model required, in order to make a successful weld. This demonstrated that the weld formation was less susceptible to the laser power under the dual laser beam model, supporting the expansion of the laser’s effective power window during the welding-brazing process.
Conclusions and messages for welding laser beam shapes
This research sheds some important light on the use of dual beam configuration on the quality of joints in dual-alloy structures. Let’s summarize the following key takeaways form the study:
- Due to the higher heating regions of the in-line and cross dual laser beams, an acceptable weld formation could be achieved, whereas undercut occurred for the joint generated by the single laser beam.
- Dual laser beam could homogenize the distribution of interfacial IMC in addition to reducing the overall thickness of it. Cross dual laser beam created the most homogeneous IMC because it had the lowest peak temperatures and the smallest temperature gradient along the brazing contact.
- The best tensile characteristics of the Al/steel joint created by the cross dual laser beam were the result of satisfactory weld formation and more acceptable interfacial IMC distribution.
This blog post was sponsored by RPMC Lasers – Leading Supplier of Laser Technologies in North America