Optical fibers have become an integral part of the telecommunications industry, as well as the photonics market. While silica fibers are most commonly used for such applications, there may be a better alternative fiber material like ZBLAN. ZBLAN fiber, though introduced in the 1970s, has only recently been gaining traction.
Silica Fibers
For optical fiber communication, the standard fiber is made of silica glass. A basic optical fiber has a core (the silica glass component), cladding (made of a higher index material), and coating. There is also a buffer around the core to keep out water that must be stripped when splicing. Light containing information is coupled into the fiber and travels down it in modes to be received at the other end. This light propagation down the fiber is typically described using a model that uses the signal as the input at a specified angle which undergoes total internal reflection until it is received at the other end. This model is not entirely accurate, but helps visualize how the light travels and provides a good approximation.
Glass fibers tend to be compared to copper wiring in the telecommunications industry. Fibers can provide a wider bandwidth than copper wires thanks to multi-mode fibers. Fibers exhibit lower signal losses at long distances than copper wiring, though signals still become attenuated. Other advantages of optical fiber include their durability and lack of interference. Since fiber optics are not made of conductors, they do not interfere with other electromagnetic signals. Optical fibers are light based, relying on photons rather than electrons to carry information, so they also propagate signals more quickly than their copper counterparts.
These advantages have made silica fibers the material of choice for many telecommunication applications and beyond, but what about comparing silica-based fibers to other glasses? There are alternative materials and methods being explored that would create fibers that out-perform the widespread silica-based ones One such alternative is the ZBLAN fiber.
ZBLAN Fibers
ZBLAN fibers, fibers made of doped zirconium fluoride, barium fluoride, lanthanum fluoride, aluminum fluoride and sodium fluoride, have an even wider transmission window than the silica fiber. Silica fiber cuts off at around 2 microns, whereas ZBLAN cuts off much closer to 3 microns, leaving room for numerous applications in the mid-IR range for medical uses, military uses, and beyond. In theory, ZBLAN fibers also have much lower attenuation in the wavelengths commonly used for telecommunications than silica fibers—some predictions have ZBLAN fibers suffering a loss of only one-tenth the amount of silica fibers. Matching the ZBLAN fiber performance to the predicted model in practice, however, is a different matter altogether.
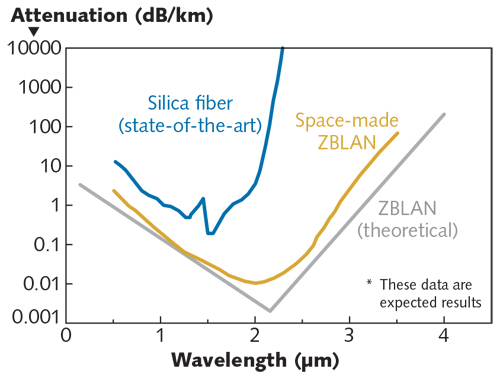
This compares the optical window of silica-fiber, the space-made ZBLAN fiber, and the theoretical model of ZBLAN. Courtesy of LaserFocusWorld
Due to the material makeup of the fibers, they should have properties conducive to improved telecommunication capacity in the near-/mid- IR range. However, there are limiting factors that have prevented ZBLAN fibers from becoming widely used for communication purposes. One factor contributing to losses is impurities in the ZBLAN glass. Since it is made from so many different elements, their differences tend to cause phase separation in the material.
The second is the structure of ZBLAN itself. ZBLAN forms as a lattice. On Earth, this lattice is unable to from correctly due to the gravitational pull and crystallization. This imperfect lattice induces scattering losses. Obviously, it is difficult to mass produce quality ZBLAN fibers here on Earth if gravity is what is causing the problem. This is especially the case, as in fiber manufacturing, fibers are typically drawn in vertical tower-like structures with gravity aiding with the pulling of the fiber.
ZBLAN Testing and Production
Interestingly, these fibers have been manufactured in a gravity-free environment. NASA explored pulling fibers in microgravity in 1994 and again in 1996. They produced ZBLAN preforms during the microgravity phase of a parabolic aircraft flight and compared them to the ones created on Earth. Though neither attempt yielded the theoretically predicted structure, it did reveal that the crystallization was minimized when the fiber was produced in a microgravity environment, and that they had “significantly superior properties” than those made terrestrially.

The leftmost photo is ZBLAN fiber created in micro-gravity and the rightmost photo is ZBLAN fiber created on Earth. Courtesy of Upward
More recently, a company, Made In Space (MIS), which has a goal of making space a ready environment for living and working, has taken on ZBLAN fiber experimentation. This company has created zero-gravity 3D printers for the International Space Station (ISS). ZBLAN fibers of good quality were able to be produced in a micro-gravity environment aboard the ISS. MIS, in conjunction with Thorlabs, has created a sealed, fully-automated fiber-drawing system for the ISS that is roughly the size of a microwave. MIS has produced ZBLAN on, at least, four occasions in space now and is looking to find a way to make it more commercially compatible.
Pros and Cons
While ZBLAN fiber has advantages over silica fiber, there are factors (besides manufacturing in space) that limit its current availability and usage. Cost considerations limit the length of ZBLAN fiber for manufacturing. Some 700m lengths are commercially produced, but range in price from $150/m to $300/m compared to silica fiber prices that can be as low as around $20/m. Silica fibers are the clear winner in terms of cost and manufacturing—there is no problem creating usable fibers here on Earth. Thorlabs has produced ZBLAN fibers of higher than average quality with high quality preform in optimal conditions, but still not as well-performing as those of worse quality preform pulled in micro-gravity.
Still, ZBLAN fibers are attractive because of their information capacity. They could be an improvement of special interest for underwater cables that span between continents since they would require less repeaters and provide a wider bandwidth than silica fiber.
Conclusion
Further research is being taken on to figuring out ways to make ZBLAN fibers more cost-effective and manufacturing-friendly. This is not unlikely to be achieved, as companies taking advantage of the commercialization opportunities of space continue to grow.
This post was sponsored by DataRay Inc. – world leader in laser beam profiling solutions.