TLC Summit Gen-5 Mechanical Glass-Cutting Machine
Description
The TLC Summit Gen-5® High-Accuracy Mechanical Rectilinear/SHAPES Glass Cutter is feature-rich equipment designed for versatility, long-term production and close dimensional tolerance afterbreak edges that require little or no polish/grind processing.
It is a low-cost, single head, simple-to-operate, easy-to-maintain glass cutting machine. Rectilinear (X-Y), circular, and curvilinear single sheet or laminated glass/substrate parts are quickly and easily processed with high afterbreak yields.
TLC Summit Gen-5 Mechanical Glass-Cutting Machine
Specifications |
|
---|---|
Working Area (X): | 1160 mm |
Working Area (Y): | 1460 mm |
Working Area (Z): | -- mm |
Max Travel Speed: | 45.7 m/min |
Max Working Speed: | 45.7 m/min |
Features
- Greater tolerance cutting control in circular/curvilinear parts, with the advantage of encoder feedback for higher quality and accuracy.
- The 46" x 58" / 1160 mm x 1460 mm square stage is stationary (does not rotate) - maintains overall flatness for a long period of use.
- Better real estate utilization of costly substrates by "nesting" of same or multiple shapes on one substrate.
- Microsheet and thinner glass/substrate processing with a mechanical wheel.
- Enhanced positioning to align circular, curvilinear, as well as linear and multilinear configurations.
- Elimination of cutting only continuous line shapes with step repeatability.
- AutoCAD® drawings (.dxf) allow a third color (red) to be used to lift the head and move it to the next designated point. This allows for greater shape cutting capabilities including corner cropping.
- Free software upgrades (flash upgradeable), if no mechanical change is required.
- Small footprint (68" X 94"/1727 mm x 2388 mm) and stand-alone design allows easy incorporation in any start-up or full production process line.
Applications
- Flat panel displays (FPDs)
- Microdisplays
- Dichroic/color filters
- Camera lenses
- Hot/cold mirrors
- Cosmetic mirrors
- Heat control filters
- Optical components
- Lenses/viewfinders
- Mini hard disks
- Navigation/guidance controls
- Polarizing filters
- Photovoltaic (solar) cells
- Electrochromic mirrors
- Medical imaging panels (digital X-rays)
- Entertainment lighting gobos
- Sensors
- Touchscreens
- Welding shields Medical/laboratory microslides/slipcovers
For pricing, technical or any other questions please contact the supplier
- No registration required
- No markups, no fees
- Direct contact with supplier
-
Ships from:
United States
-
Sold by:
-
On FindLight:
External Vendor
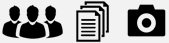
Claim TLC International Page to edit and add data
Frequently Asked Questions
The applications of the TLC Summit Gen-5 Mechanical Glass-Cutting Machine include flat panel displays (FPDs), microdisplays, dichroic/color filters, camera lenses, hot/cold mirrors, cosmetic mirrors, heat control filters, optical components, lenses/viewfinders, mini hard disks, navigation/guidance controls, polarizing filters, photovoltaic (solar) cells, electrochromic mirrors, medical imaging panels (digital X-rays), entertainment lighting gobos, sensors, touchscreens, welding shields, and medical/laboratory microslides/slipcovers.
The features of the TLC Summit Gen-5 Mechanical Glass-Cutting Machine include greater tolerance cutting control in circular/curvilinear parts, better real estate utilization of costly substrates, enhanced positioning to align circular, curvilinear, as well as linear and multilinear configurations, elimination of cutting only continuous line shapes with step repeatability, and free software upgrades.
The cutting stage size of the TLC Summit Gen-5 Mechanical Glass-Cutting Machine is 46" x 58" / 1160 mm x 1460 mm square stage, which is stationary (does not rotate) and maintains overall flatness for a long period of use.
The TLC Summit Gen-5 Mechanical Glass-Cutting Machine has a small footprint of 68" X 94"/1727 mm x 2388 mm and a stand-alone design that allows easy incorporation in any start-up or full production process line.
The TLC Summit Gen-5 Mechanical Glass-Cutting Machine is a feature-rich equipment designed for versatility, long-term production, and close dimensional tolerance afterbreak edges that require little or no polish/grind processing.