Efficiency and productivity are critical for success in the manufacturing industry. Lean manufacturing principles offer effective strategies to optimize processes and reduce waste. In this article, we present five key strategies to boost productivity and efficiency in your manufacturing operations. By examining challenges, investing in smart tools, implementing the 5S action plan, maintaining equipment, and automating processes, you can achieve significant improvements in your workflow.
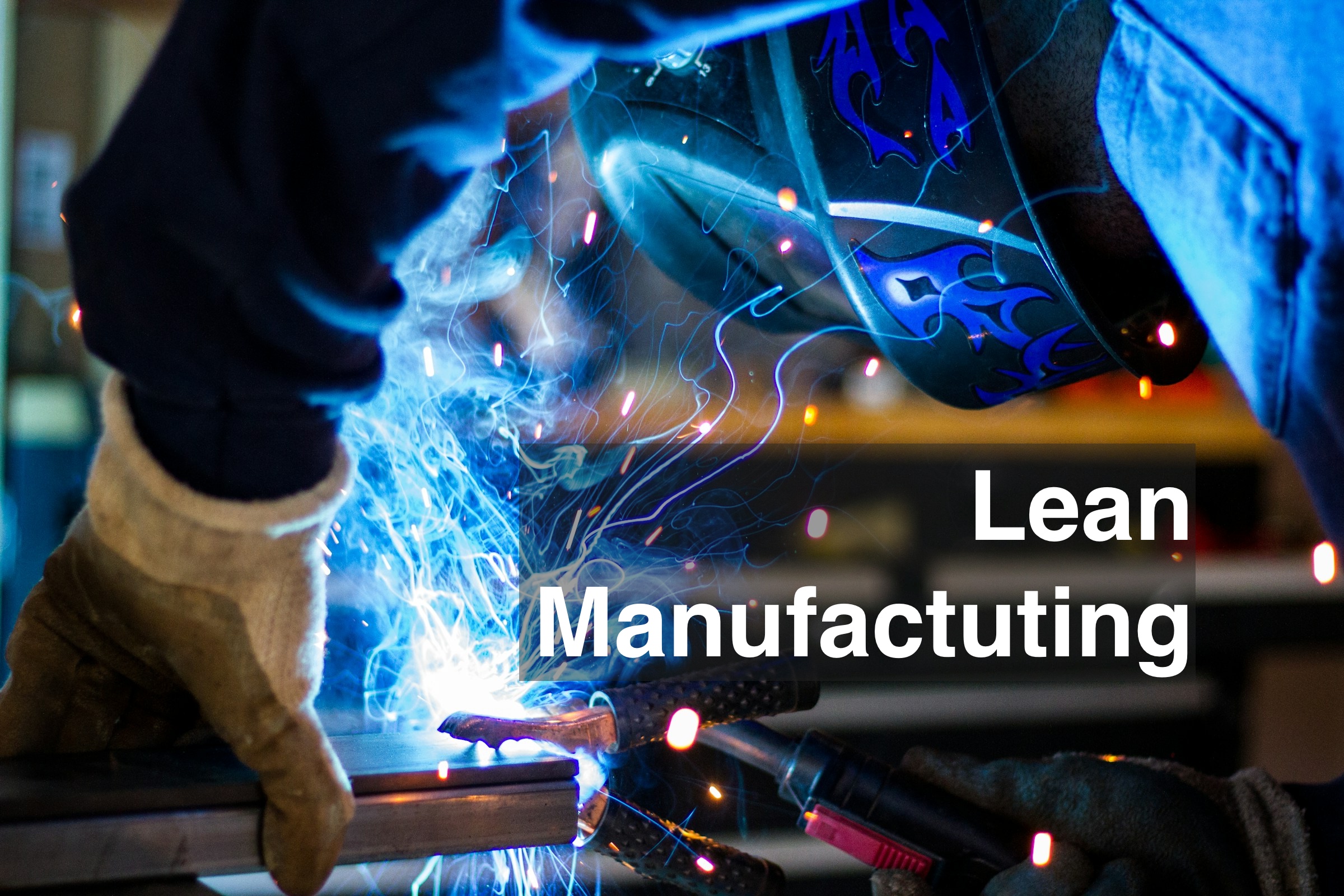
A factory worker welding, showcasing the principles of lean manufacturing to enhance productivity and efficiency. Image courtesy of Rob Lambert.
1. Identify and Assess Challenges
Identifying and addressing existing problems in your workflow is crucial for improving manufacturing efficiency. Start by thoroughly examining each stage of your process to pinpoint bottlenecks and inefficiencies. Engage your team to gather input and perspectives, as they often have firsthand insights into daily operations.
Key steps to identify challenges include:
- Assess Workflow: Map out the entire manufacturing process to identify areas where delays or errors occur.
- Gather Team Input: Hold regular meetings with employees to discuss pain points and potential improvements.
- Analyze Data: Review production data to spot trends and recurring issues.
Ask critical questions during this assessment:
- Do we have the right personnel for each task?
- Are we maintaining consistent quality standards?
- Are we using the best available technology and equipment?
By systematically identifying and assessing challenges, you can create targeted strategies to enhance productivity and efficiency in your manufacturing operations.
2. Conduct a Thorough Factory Audit
Factory audit services are crucial for enhancing efficiency in manufacturing processes. By thoroughly evaluating production facilities, these audits identify bottlenecks, inefficiencies, and non-compliance issues that can severely affect performance. Armed with this valuable insight, manufacturers can streamline processes, reduce waste, and optimize resource utilization, leading to a notable increase in productivity.
Moreover, factory audits ensure compliance with industry standards and safety regulations. This not only fosters a safer workplace but also reduces the risk of costly legal complications. Through regular audits and the implementation of corrective actions, manufacturers can boost product quality, enhance workplace safety, and increase customer satisfaction. This, in turn, strengthens market competitiveness and drives business growth.
3. Invest in Smart Tools and Technology
Investing in smart tools and technology is essential for enhancing manufacturing efficiency. “Better tools” don’t necessarily mean expensive; they refer to equipment that is efficient, reliable, and capable of optimizing your operations.
What Constitutes “Better Tools”?
- Efficiency: Tools that streamline processes and reduce manual effort.
- Reliability: Equipment that minimizes downtime and maintenance needs.
- Scalability: Technology that can grow with your business and adapt to increasing demands.
Examples of Smart Tools:
- Automated Assembly Lines: Reduce human error and increase production speed.
- Predictive Maintenance Systems: Use sensors and data analytics to anticipate equipment failures and schedule timely repairs.
- ERP Software: Integrate various business processes to improve data flow and decision-making.
Continuous Investment in Technology:
- Staying competitive requires ongoing investment in the latest technologies.
- Regularly upgrading tools and systems ensures your operations remain efficient and up-to-date.
- Investing in employee training for new technologies maximizes the benefits of your investments.
By adopting smart tools and continually upgrading your technology, you can fill process gaps, prevent malfunctions, and significantly boost productivity in your manufacturing operations.
4. Implement 5S Action Plan for Lean Manufacturing
The 5S methodology is a foundational aspect of lean manufacturing, designed to create an organized, efficient, and safe work environment. The 5S principles are: Sort, Set in order, Shine, Standardize, and Sustain.
Overview of the 5S Methodology:
- Sort: Remove unnecessary items from the workspace to reduce clutter and improve focus.
- Set in Order: Arrange tools and equipment logically to enhance workflow and efficiency.
- Shine: Keep the workplace clean and orderly to prevent accidents and improve morale.
- Standardize: Establish uniform procedures and standards to maintain consistency.
- Sustain: Continuously review and improve practices to ensure long-term success.
Benefits of Implementing the 5S Plan:
- Increased Efficiency: Streamlined processes and reduced waste lead to faster production times.
- Improved Safety: A clean and organized workspace minimizes the risk of accidents.
- Enhanced Morale: Employees work better in an orderly environment, boosting overall productivity.
- Better Quality Control: Standardized procedures ensure consistent product quality.
Practical Steps to Apply the 5S Principles:
- Conduct a Workplace Audit: Identify areas needing improvement and categorize items based on necessity.
- Create Organizational Schemes: Designate specific places for tools and materials, labeling them clearly.
- Establish Cleaning Routines: Implement daily or weekly cleaning schedules to maintain a tidy environment.
- Develop Standard Operating Procedures (SOPs): Document best practices and train employees to follow them.
- Foster a Culture of Continuous Improvement: Encourage feedback and regularly review processes to sustain 5S practices.
By implementing a 5S plan, you can achieve a more efficient, safe, and productive manufacturing environment, aligning with lean manufacturing goals.
5. Prioritize Equipment Maintenance
Regular equipment maintenance is crucial for ensuring smooth operations and achieving cost savings in manufacturing. Neglecting maintenance can lead to unexpected breakdowns, costly repairs, and significant downtime, all of which can disrupt your production schedule.
Effective equipment maintenance strategies include routine checks and professional servicing. Conducting regular inspections helps identify potential issues before they become major problems. Scheduling professional servicing ensures that machinery operates at peak efficiency and complies with industry standards. These preventive measures not only enhance equipment reliability but also extend its lifespan.
The long-term benefits of maintaining machinery are substantial. Reduced downtime means your production lines remain active, avoiding delays and meeting delivery deadlines. Extended equipment life translates to lower capital expenditures on new machinery, providing significant cost savings. Additionally, well-maintained equipment consistently produces high-quality output, contributing to overall productivity and customer satisfaction.
6. Automate Key Processes
Automation plays a pivotal role in enhancing business operations within the manufacturing sector by streamlining workflows, reducing human error, and increasing overall productivity. Numerous processes in manufacturing can be automated, such as assembly lines, automated systems for repetitive tasks, quality control with automated inspection systems, inventory management through automated tracking systems, and packaging and labeling with automated machines ensuring consistency and efficiency.
The benefits of automation are significant: increased efficiency as automated processes operate faster and more reliably than manual ones, improved quality by reducing the risk of human error, and happier clients due to reliable and high-quality production. By automating key processes, manufacturers can achieve greater efficiency, maintain high quality, and meet customer demands more effectively, driving overall business success.
Conclusion: Achieving Lean Manufacturing Efficiency
In summary, achieving lean manufacturing efficiency involves five key strategies: identifying and assessing challenges, investing in smart tools and technology, implementing the 5S action plan, prioritizing equipment maintenance, and automating key processes. By systematically applying these strategies, you can streamline operations, reduce waste, and enhance productivity.
The long-term benefits of these practices are substantial, including increased operational efficiency, reduced downtime, cost savings, and improved product quality. These improvements not only boost your bottom line but also contribute to greater customer satisfaction and a stronger competitive edge.
Take actionable steps today to implement these lean manufacturing principles and drive your business toward sustained productivity and efficiency improvements. By committing to continuous improvement and leveraging these strategies, you can achieve lasting success in your manufacturing operations.